Analyzing Anodic Metals: Properties and Applications
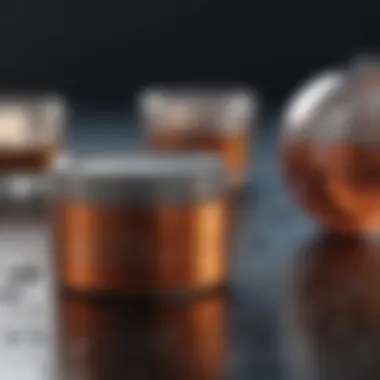
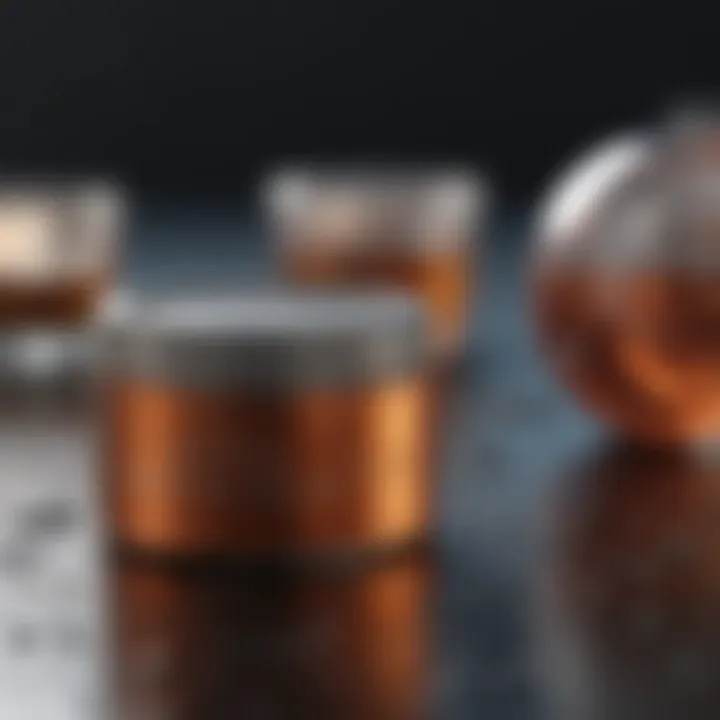
Intro
In the realm of materials science, anodic metals present a fascinating area of study due to their unique electrochemical properties and wide range of applications. Anodic metals are specifically valued for their behavior in anodic processes, where they undergo oxidation, releasing electrons and thus affecting various reactions crucial to many industries. Understanding these characteristics and their implications is essential for anyone involved in engineering, research, or education.
This analysis intends to shed light on anodic metals, covering everything from their fundamental properties to their significant roles in advanced technological applications. The exploration will include a discussion of their importance in electrochemical industries, specifically in energy storage systems and strategies to combat corrosion. The goal is not only to inform but to provide a structured framework to help readers navigate the complexities of anodic metals.
Through careful examination, we aim to elucidate the criteria for selecting appropriate anodic metals based on environmental conditions and the underlying mechanisms of anodic reactions. This comprehensive approach will culminate in an understanding of the future potential of these metals in technological advancements, particularly as they relate to modern engineering practices.
Preface to Anodic Metals
The topic of anodic metals is crucial in understanding various technological processes, particularly those related to electrochemistry and material science. Anodic metals exhibit distinct behaviors when subjected to anodic processes, which can significantly affect their applications in real-world scenarios. This section introduces the concept, characteristics, and significance of anodic metals, highlighting their benefits in different industries and areas of research.
Definition and Characteristics
Anodic metals refer to a category of metals that undergo oxidation during anodic processes, typically occurring within an electrolytic cell. The primary characteristic of these metals is their ability to form a protective oxide layer on their surface, enhancing their corrosion resistance. This process is not only important for preventing deterioration but also extends the lifespan of products that use these metals.
Common examples include aluminum, titanium, and zinc. Each of these materials has unique properties that influence their effectiveness in specific environments. For instance, aluminum alloys are known for their lightweight and high strength, making them ideal for aerospace applications. Titanium, on the other hand, is valued for its strength-to-weight ratio and resistance to corrosion, especially in harsh marine environments.
Historical Context
The recognition of anodic metals can be traced back to the early 20th century. The development of anodizing processes gained momentum with aluminum, which became widely used after World War II. The desire for lightweight yet durable materials in construction and transportation led to extensive research on the anodizing of aluminum. This era marked a significant shift in how industries approached material selection, moving towards metals that not only met mechanical requirements but also offered enhanced longevity.
Additionally, the understanding of the electrochemical processes behind anodizing continued to advance. Researchers explored how different parameters of the anodizing process, such as voltage and electrolyte composition, impact the quality of the oxide layer formed on the metals. This deepened historical perspective illustrates the evolving relationship between anodic metals and material technology.
Importance in Material Science
In material science, anodic metals hold a prominent position due to their properties and applications across diverse fields. They are fundamental in creating durable components that can withstand corrosive environments, making them invaluable in industries like aerospace, automotive, and marine engineering.
Several factors contribute to the importance of these metals:
- Corrosion Resistance: The protective oxide layers formed during anodizing prevent further oxidation, prolonging service life.
- Functional Versatility: Anodic metals can be tailored for specific applications through careful control of anodizing processes, enhancing their usability in various environments.
- Energy Efficiency: The lightweight nature of anodic metals reduces the energy consumption during operations, particularly in transportation.
- Sustainability: Many anodic metals can be recycled without loss of quality, contributing to sustainable manufacturing practices.
"Anodic metals represent a convergence of material properties and innovative processing techniques that enhance performance and sustainability in modern engineering."
With this foundational understanding, the article will now move into the mechanisms that govern the anodic reactions, further illuminating this vital area of study.
Mechanisms of Anodic Reactions
Understanding the mechanisms of anodic reactions is essential to grasp the behavior of anodic metals in various applications. This section covers the fundamental electrochemical principles involved, the processes of oxidation that occur, and the impact of various anodizing techniques. Each component plays a crucial role in determining the performance and utility of anodic metals in different industrial contexts.
Electrochemical Principles
Electrochemical principles form the bedrock of anodic reactions. When a metal is subjected to an external electric field in a solution, it undergoes oxidation. This oxidation occurs at the anode, where metal atoms lose electrons. The resultant positive ions may enter the solution, emphasizing the need for a conductive medium.
The Nernst equation can be applied here; it describes the relationship between the concentration of ions and the electrode potential. The understanding of these principles allows for accurate predictions on how anodic metals will perform under different conditions.
Oxidation Processes
Oxidation processes in anodic metals are complex and depend on surface conditions and solution chemistry. During the anodic oxidation, a protective oxide layer often develops, significantly enhancing corrosion resistance. This layer acts as a barrier that prevents further oxidation of the underlying metal.
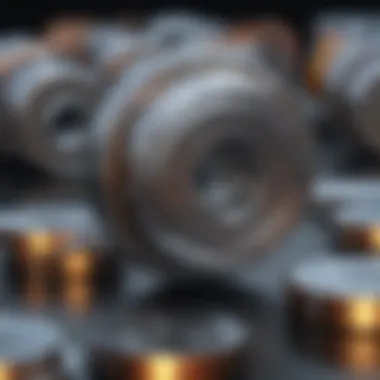
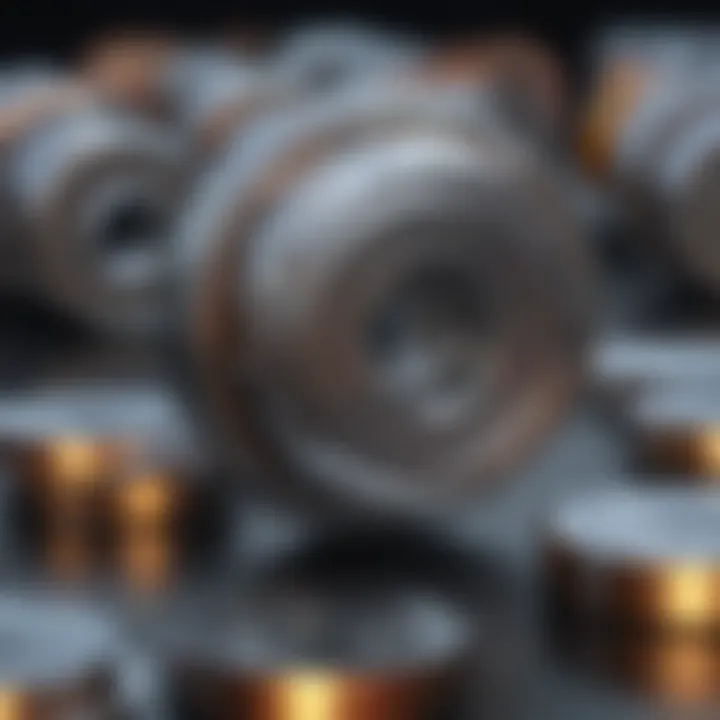
In a controlled environment, initiating an anodic reaction contributes to surface energy states. Factors such as temperature and pH can markedly influence these reactions. It is essential to consider the thermodynamics involved to improve the efficiency of anodizing.
Impact of Anodizing Techniques
Anodizing techniques directly affect the properties of anodic metals. Different anodizing methods, such as sulfuric acid anodizing or hard anodizing, produce varying thicknesses and compositions of the oxide layer. Each approach has its advantages and limitations. For example, sulfuric anodizing offers good corrosion resistance and coloration ability, while hard anodizing provides enhanced wear resistance.
The choice of technique relies on the intended application. For instance, in aerospace applications, the requirements for strength and resistance to wear are paramount, guiding the choice of anodizing process. Therefore, comprehending the impact of these techniques enables researchers and engineers to optimize performance in their specific contexts.
"The choice of anodizing technique is critical to achieving the desired properties in anodic metals."
In summary, the mechanisms of anodic reactions are fundamental in understanding how anodic metals function in diverse applications. Essential concepts include electrochemical principles, oxidation processes, and the impact of anodizing techniques. A solid grasp of these topics enhances the ability to select appropriate materials and processes for various engineering and research endeavors.
Types of Anodic Metals
The selection of anodic metals is pivotal in both research and industry due to their unique properties and extensive applications. Understanding the different types of anodic metals allows professionals to make informed choices based on performance requirements, environmental conditions, and desired outcomes in various processes. Here, we examine several key types of anodic metals, focusing on aluminum alloys, titanium and its alloys, zinc-based materials, and magnesium alloys. Each of these materials has unique characteristics that impact their usability in different applications.
Aluminum Alloys
Aluminum alloys are widely recognized for their excellent corrosion resistance and lightweight properties. These characteristics make them suitable for a variety of industries, including aerospace and automotive. Anodizing aluminum not only enhances its resistance to environmental factors but also improves aesthetic appearance through the creation of a protective oxide layer. The thickness and quality of this layer can vary based on factors such as alloy composition and anodizing techniques.
- Benefits of Aluminum Alloys:
- Exceptional strength-to-weight ratio
- Customizable surface finish
- High electrical conductivity
- Good thermal properties
Although aluminum alloys have many advantages, they also come with limitations. Certain alloys can exhibit reduced strength at elevated temperatures or may become brittle over time. Understanding these factors is crucial for engineers designing components that rely on the mechanical integrity of aluminum alloys.
Titanium and its Alloys
Titanium is known for its remarkable strength and resistance to corrosion, making it a valuable material in medical, aerospace, and chemical processing applications. Its anodization process can enhance its natural protective oxide layer, further improving its performance in harsh environments. Titanium alloys, such as Ti-6Al-4V, utilize aluminum and vanadium to achieve a balance among strength, ductility, and weldability.
- Advantages of Titanium and its Alloys:
- High strength-to-weight ratio
- Excellent biocompatibility for medical implants
- Resistant to high temperatures and chemicals
However, titanium alloys are often more expensive and more difficult to process compared to other metals. These factors must be carefully considered by professionals when selecting materials for specific applications.
Zinc-Based Materials
Zinc-based materials also play a role in anodic applications, particularly in galvanizing processes. Zincβs ability to corrode preferentially protects the underlying metal from degradation. Anodizing can further enhance zinc's resistance to corrosion by adding a protective oxide layer. Zinc-aluminum alloys, for example, are commonly used in die-casting applications because they offer improved mechanical properties and better corrosion resistance than pure zinc.
- Key Attributes of Zinc-Based Materials:
- Cost-effective with good antifungal properties
- Better ductility than pure zinc
- Suitable for outdoor applications where humidity and exposure to the elements are concerns
Nevertheless, zinc-based materials may not be as durable as other metals, especially under extreme conditions. Understanding their performance limits is essential in selecting the appropriate use cases.
Magnesium Alloys
Magnesium alloys are among the lightest structural materials available, making them an attractive option for industries where weight reduction is critical. Anodizing magnesium can improve its natural resistance to corrosion, but the process requires careful control to ensure quality and longevity of the anodized layer. Common applications for magnesium alloys include automotive components and portable electronics due to their excellent strength-to-weight ratios.
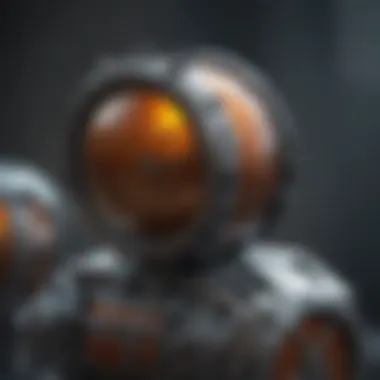
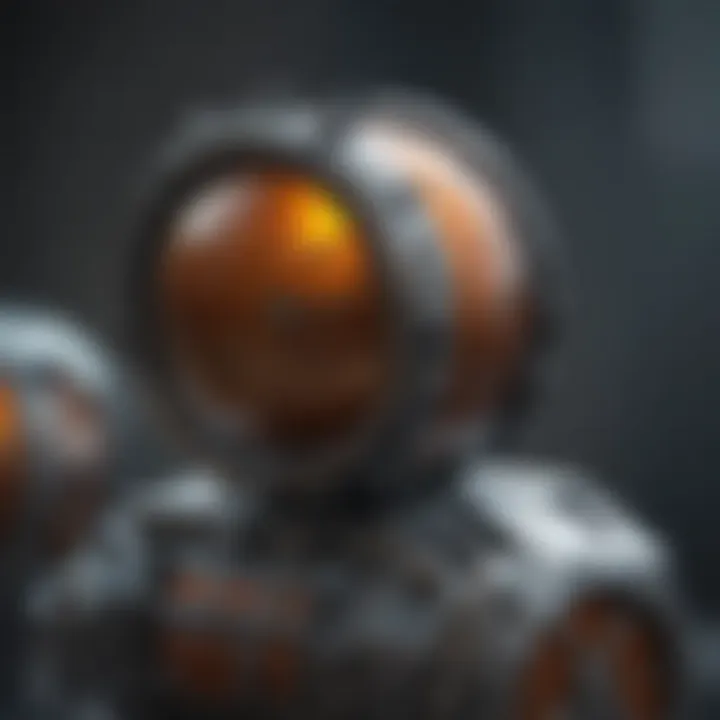
- Benefits of Magnesium Alloys:
- Very light with good mechanical properties
- High damping capacity, advantageous in reducing vibrations
- Excellent machinability
However, magnesium alloys are more prone to corrosion compared to other anodic metals. Their use in corrosive environments should be evaluated thoroughly to prevent premature failure.
Applications of Anodic Metals
The significance of anodic metals extends far beyond their electrochemical behavior. Understanding their applications is crucial in fields ranging from aerospace to renewable energy. These metals exhibit properties that make them outstanding choices for various high-tech functions. Here, we delve into specific areas where anodic metals make a remarkable impact.
Corrosion Resistance
Corrosion is a major challenge for many industries, leading to significant economic losses and safety hazards. Anodic metals, particularly aluminum alloys and titanium, are noted for their excellent corrosion resistance. When anodized, these metals form a protective oxide layer that acts as a barrier against corrosive environmental factors. This process not merely enhances their durability but also extends their lifespan in applications where exposure to harsh elements is inevitable.
- Anodized aluminum is widely used in the automotive and aerospace industries due to its lightweight and anti-corrosive properties.
- Titanium, known for its high strength-to-weight ratio and exceptional resistance to corrosion, finds applications in marine environments, chemical processing, and medical implants.
"The effective anodization of metals not only protects against corrosion but enhances aesthetic values, contributing to the material's appeal in consumer products."
In Energy Storage Systems
The demand for efficient energy storage solutions continues to rise with advancements in technology. Anodic metals play a critical role in this sector, especially in the development of batteries.
- Aluminum-based anodes are increasingly used in lithium-ion battery technologies. The anodic process promotes better conductivity and enhances battery performance.
- Research suggests that anodized anodes can improve battery life and energy density, making them a focal point in developing more efficient batteries.
Electrochemical Capacitors
Electrochemical capacitors, or supercapacitors, are devices designed to store and release energy rapidly. Anodic metals are essential in this context because they provide the conductive pathways needed for charge storage.
- Materials such as activated carbon and titanium dioxide, when anodized, have shown improved charge storage capabilities. This leads to better performance in terms of energy and power density.
- The high surface area achieved through anodizing techniques allows for more efficient ion transport, making them crucial components in various electronic devices.
Construction and Structural Applications
Anodic metals are prevalent in construction and structural applications due to their strength, durability, and resistance to corrosion. They are ideal for use in a variety of building materials and frameworks.
- Anodized aluminum is commonly used in facades, windows, and roofing materials, contributing to the longevity and aesthetic of buildings.
- The use of anodized titanium in structural applications also showcases its strength and lightweight characteristics, making it suitable for high-performance environments like bridges and aerospace structures.
Challenges in Using Anodic Metals
Anodic metals bring significant advantages to various fields, but they also present unique challenges. Understanding these challenges is crucial for minimizing their impact on applications and for developing innovative solutions. This section highlights three main areas of concern: material limitations, processing difficulties, and environmental considerations.
Material Limitations
Anodic metals exhibit specific characteristics that can hinder their application. One major limitation is their susceptibility to wear and tear. While anodizing enhances corrosion resistance, it may not always provide sufficient abrasion resistance. In high-friction environments, anodic layers can wear down quickly, making materials like anodized aluminum less ideal.
Another limitation is the thickness of the anodized layer. A thicker layer provides better protection but can compromise the metal's mechanical properties. This trade-off affects overall performance and may lead to failure in demanding applications. Moreover, certain anodic metals, like magnesium alloys, are limited in high-temperature applications due to their reduced structural integrity. Thus, choosing the right anodic metal for specific situations is of utmost importance.
Processing Difficulties
The processing of anodic metals is intricate and requires precise control. This makes it challenging to achieve consistent results in large-scale production. Anodizing parameters, such as voltage and temperature, must be meticulously calibrated. Any deviation can affect the quality of the anodized layer, leading to inferior performance in applications.
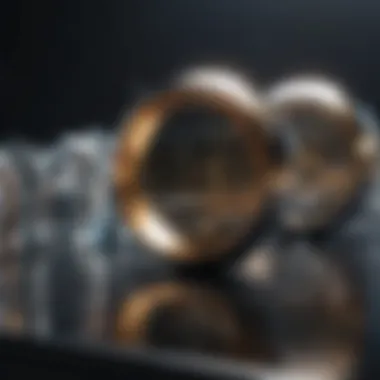
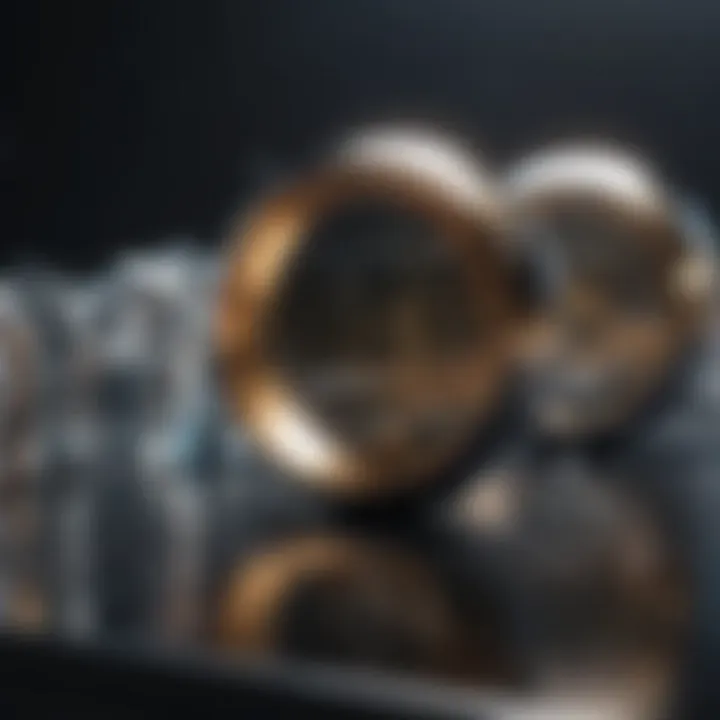
In addition, removing anodized coatings can be problematic. Traditional methods often involve hazardous materials, which pose environmental and safety concerns. New techniques are being developed, but they are still in the experimental stage. As such, processing difficulties can contribute to higher costs and prolonged lead times in production.
Environmental Considerations
The environmental implications of using anodic metals cannot be overlooked. The anodizing process often employs toxic chemicals, which can lead to pollution if not handled properly. Facilities must comply with strict regulations to minimize their environmental footprint, and this can create additional operational burdens.
Furthermore, the lifecycle of anodic metals warrants attention. During disposal, certain anodic metals may leach harmful substances into the ecosystem. Proper recycling and disposal methods are critical to mitigate these risks. Minimizing the environmental impact of anodic metals is not just a regulatory challenge; it is a moral obligation for sustainable engineering practices.
"Understanding the challenges of anodic metals is essential for advancing their applications in technology and sustainable development."
In summary, awareness of these challenges is essential for researchers and engineers. Proper selection and processing of anodic metals can convert potential problems into solutions, ensuring their successful application across industries.
Future Directions in Research
The area of anodic metals continues to evolve, making research into this topic increasingly significant. Investigating future directions in this field can illuminate unknown potentials and pave the way for innovative applications in technology and engineering. As we look forward, several critical aspects warrant attention, including advancements in anodizing techniques, emerging anodic materials, and their integration with modern technology. Each of these elements holds the promise of enhancing the existing capabilities of anodic metals and broadening their applications.
Advancements in Anodizing Techniques
Recent years have seen considerable advancements in anodizing techniques. Traditional anodizing methods, while effective, often face limitations concerning uniformity and thickness of the anodic layers. New processes such as hard anodizing, micro-arc oxidation, and plasma electrolytic oxidation (PEO) are gaining prominence. These techniques offer superior performance characteristics such as increased hardness, improved wear resistance, and enhanced corrosion protection.
Moreover, the development of environmentally friendly anodizing solutions is garnering attention. Traditional anodizing often relies on harmful chemicals. The adoption of safer electrolytes not only meets regulatory standards but also aligns with sustainability goals. This shift could significantly reduce the environmental impact of anodizing operations, making them more acceptable to modern industrial practices.
Emerging Anodic Materials
The exploration of emerging anodic materials presents exciting opportunities. While aluminum, titanium, and magnesium have long been at the forefront, researchers are increasingly investigating other alloys and composites. For instance, there are ongoing projects focused on developing aluminum-lithium alloys which promise reduced density and increased specific strength. Such materials could lead to lighter structures in aerospace applications.
Additionally, the combination of anodic metals with conductive polymers is generating interest. This synergy can enhance the electrochemical performance which is vital for applications in energy storage systems. Identifying and characterizing these new materials will be key to their future applications in various sectors.
Integration with Modern Technology
As technology continues to advance, integrating anodic metals with modern systems is essential. Topics like smart materials and IoT (Internet of Things) open avenues for using anodic metals in innovative ways. Developing sensors that incorporate anodic layers could lead to advancements in monitoring and control systems.
Furthermore, the integration of anodic metals within energy systems, such as battery technologies and capacitors, is a critical area of focus. Optimizing these materials for energy efficiency and performance can contribute significantly to developing sustainable energy solutions.
In summary, the future of anodic metals is promising. Ongoing research into anodizing techniques, emerging materials, and integration with modern technologies holds the potential to redefine their role in contemporary engineering. Producing more efficient, sustainable, and versatile anodic materials will not only enhance their applications but also contribute to global technological advancements.
Closure
The conclusion of this article serves as a vital consolidation of the insights gathered on anodic metals. This section emphasizes not only the significance of the findings but also how they fit into the broader landscape of material science and engineering.
Summarizing Key Findings
Anodic metals are integral components across various industries due to their unique properties and versatility. Key findings include:
- Electrochemical Behavior: Anodic metals exhibit distinct behaviors when subjected to electrochemical processes, enhancing their applicability in energy storage systems and corrosion protection.
- Types and Applications: Aluminum alloys, titanium and its alloys, zinc-based materials, and magnesium alloys each exhibit specific characteristics making them suitable for particular applications, from aerospace to automotive industries.
- Challenges and Innovations: Despite their advantages, these metals face challenges, including material limitations and processing difficulties. Ongoing research is addressing these issues, paving the way for advancements in anodizing techniques.
The integration of anodic metals into modern technology showcases their importance in engineering, especially as industries advance towards sustainable solutions.
Final Thoughts on Anodic Metals
The exploration of anodic metals reveals their critical role in the ongoing development of various technologies. As industries increasingly focus on sustainability and efficiency, the demand for materials that demonstrate resilience and performance continues to grow. Anodic metals stand out due to their corrosion resistance and adaptability.
In the future, we may see new anodization processes emerge, enhancing the characteristics of these metals. The research realm is wide open, promising to unlock further potential as we combine these materials with modern applications. The significance of anodic metals, coupled with innovative approaches to their use, firmly establishes their standing in contemporary engineering practices.
"The advancement in anodic materials and techniques will determine their competitive edge in the market as technology evolves."
By synthesizing all this information, it becomes clear that anodic metals are not just materials of the present; they are pivotal to the future of technological advancement.