Conductive Plastic Film: A Comprehensive Overview
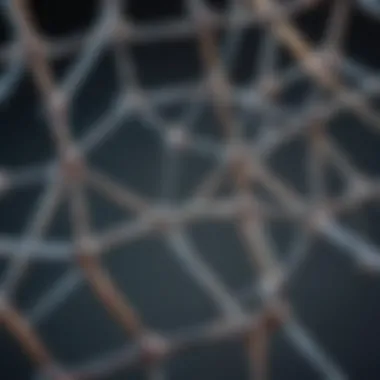
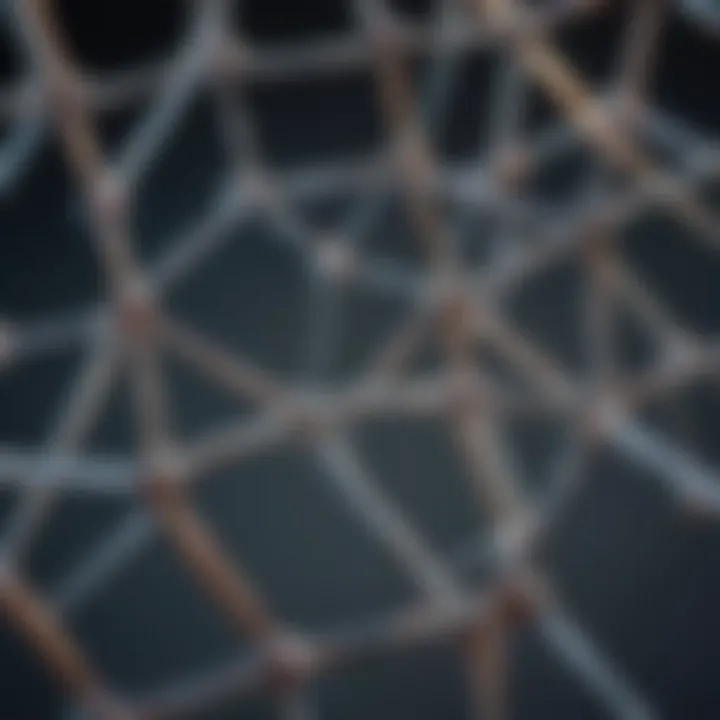
Intro
Conductive plastic film represents a significant advancement in modern materials science, combining the advantages of plastic substrates with electrical conductivity. This material has emerged due to the growing demand for lightweight, flexible, and versatile solutions across various industries. The integration of conductive polymers within plastic matrices allows for a wide range of applications, from electronic devices to energy solutions.
The unique properties of conductive plastic film open up opportunities for innovation in sectors such as consumer electronics, automotive, medical devices, and beyond. As the technology evolves, understanding the fundamental aspects of this film, including its composition, production methods, and applications, is crucial.
With the rapid advancement in related technologies, it is imperative to explore how conductive plastic films are influencing industry patterns. This article aims to provide a comprehensive analysis of the material and its implications.
Prolusion to Conductive Plastic Film
Conductive plastic films represent a remarkable blend of functionality and innovation. In today's technological landscape, these materials have gained significant attention from various sectors including electronics, energy storage, and biomedicine. Understanding conductive plastic films is crucial due to their potential to revolutionize existing systems and create new applications.
The growing interest in sustainable materials and advanced technologies drives the relevance of this topic. Conductive plastic films offer unique properties such as flexibility, lightweight composition, and ease of processing. These characteristics not only enhance performance but also push the boundaries of how we conceive material applications.
Definition and Characteristics
Conductive plastic films are thin sheets made from polymers that possess electrical conductivity. They combine polymeric matrix with conductive additives, making them suitable for various applications. The base materials typically include polymers such as polyethylene, polypropylene, or polyimide.
Their conductivity can be attributed to the presence of conductive additives like carbon black or metallic particles. The level of conductivity varies according to the type and concentration of these additives. The films can be engineered to exhibit specific properties, such as transparency or flexibility, which are essential in applications like touch screens or flexible circuits.
Historical Context
The development of conductive plastic films dates back to the mid-20th century. Researchers explored the potential of polymers to conduct electricity, which led to significant breakthroughs in material science. In the 1960s, the introduction of conductive polymers marked a turning point in this field. Initially used in niche applications, advances in manufacturing processes allowed for broader usage.
By the 1980s, conductive plastic films began to find applications in consumer electronics and automotive industries. The demand increased as industries recognized the advantages of lightweight materials with good conductivity. Today, these films play vital roles in everyday technologies and are subject to continuous research and development.
Composition of Conductive Plastic Film
Understanding the composition of conductive plastic film is crucial for grasping its functionality and applications. The material's performance hinges on its core components: base materials, conductive additives, and the polymer matrix. Each of these elements play a pivotal role in defining how the film behaves in various conditions and during specific applications. By optimizing the composition, manufacturers can create films with specific properties that meet the diverse needs of modern industries.
Base Materials
The base materials in conductive plastic film are primarily polymers, which provide the foundational structure. Common choices include polyvinyl chloride (PVC), polyethylene (PE), and polycarbonate (PC). Each of these polymers has its unique attributes, such as flexibility, resilience, and temperature resistance.
- Polyvinyl Chloride (PVC): This is a widely used plastic due to its affordability and versatility. It offers decent mechanical strength and can be easily processed.
- Polyethylene (PE): Known for its chemical resistance, PE is lightweight and flexible. This makes it suitable for applications that require bending and movement.
- Polycarbonate (PC): With high impact resistance, PC is ideal for applications demanding durability and optical clarity.
Using the right base material enhances not just the mechanical properties of the film but also its compatibility with conductive additives that will be introduced in the next section.
Conductive Additives
Conductive additives are essential for imparting electrical properties to the otherwise insulating plastics. These additives can be metallic or non-metallic and are mixed into the polymer matrix to create pathways for electron flow. The choice of additive significantly influences the final product's conductivity, cost, and processing ease.
- Carbon Black: A popular and cost-effective choice, it enhances conductivity without compromising flexibility. It is commonly used in applications that require moderate electrical conductivity.
- Silver Nanoparticles: These offer high conductivity but are more expensive. Silver nanoparticles are often used in applications needing superior performance, like certain high-tech electronics.
- Conductive Polymers: Materials like polyaniline or polypyrrole can also be used. They provide good conductivity and can be processed in similar ways as traditional plastics, aiding in ease of manufacturing.
Incorporating conductive additives must be done carefully to balance cost and functionality, as well as to maintain processing characteristics during manufacturing.
Polymer Matrix
The polymer matrix serves as the host for all other components and plays a critical role in determining overall film properties. The selection of the polymer matrix influences overall chemical resistance, thermal stability, and mechanical integrity of the final product.
- Compatibility with Additives: The polymer must be compatible with the chosen conductive additives to ensure even dispersion. Poor dispersion can lead to hotspots of conductivity, which can adversely affect the film’s performance.
- Thermal Properties: It's important for the polymer matrix to withstand temperatures during both production and end-use. The thermal degradation of the base material can lead to compromised film integrity.
- Mechanical Properties: The chosen polymer matrix should ensure that the film retains flexibility, strength, and stability during usage. High-quality polymers can significantly extend the life of the film in demanding applications.
Choosing the correct polymer matrix is vital for ensuring that the conductive plastic film can perform in its intended applications. The interplay between base materials, conductive additives, and the polymer matrix defines the functionality and performance of the film.
Understanding these components is essential for advancing applications in electronics, energy storage, and biomedicine.
By exploring the intricate composition of conductive plastic films, we lay the groundwork for appreciating their applications and performance in the next sections.
Properties of Conductive Plastic Film
Understanding the properties of conductive plastic film is crucial for grasping its functionality and relevance across various industries. This section examines three key properties: electrical conductivity, mechanical strength, and thermal stability. Each of these elements plays a significant role in determining the material's performance and application scope.
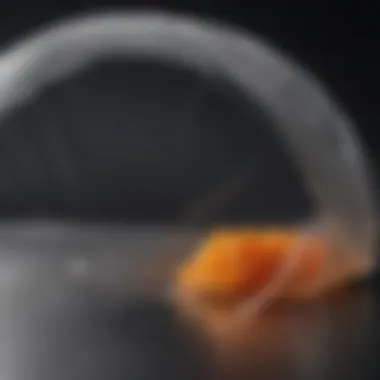
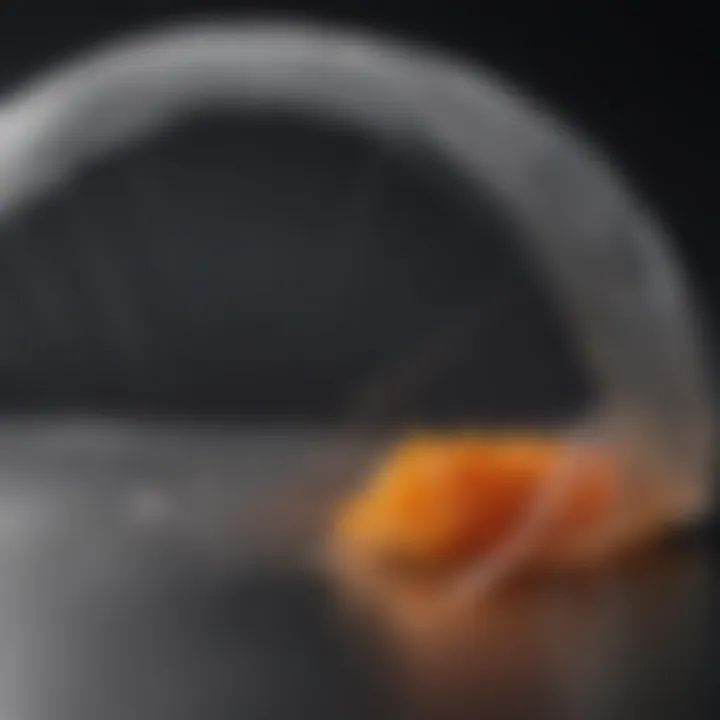
Electrical Conductivity
Electricity is a fundamental aspect of modern technology, and conductive plastic films are designed to possess significant conductive properties. This conductivity arises from the incorporation of conductive additives such as carbon black or metal powders into the polymer matrix. The level of conductivity can be fine-tuned based on the type and amount of these additives, allowing for customization according to specific application requirements.
The importance of electrical conductivity cannot be overstated. In consumer electronics, conductive plastics serve as essential components in touchscreens, flexible circuit boards, and sensors. Enhanced conductivity leads to improved performance, reliability, and energy efficiency in electronic devices. Moreover, the ability to combine flexibility with conductivity opens new avenues in design, making it possible to create thinner and lighter devices without sacrificing function.
Mechanical Strength
While electrical conductivity is vital, the mechanical strength of conductive plastic film is another essential characteristic. This property enables the material to withstand physical stresses and strains during handling, installation, and use. Mechanical strength refers to how well a material can resist deformation or failure when subjected to forces such as tension, compression, or bending.
The mechanical properties of conductive plastic films are influenced by the base polymers used and the formulation of the conductive additives. For instance, incorporating additives into a high-strength polymer matrix can yield a film that is both conductive and mechanically robust. This combination is crucial for applications where the film must endure harsh environments, such as in automotive or aerospace applications.
A notable feature of conductive plastic films is their ability to combine lightweight characteristics with high strength, enabling advanced engineering solutions.
Thermal Stability
Thermal stability represents another critical aspect of conductive plastic films. This property determines how well a material can maintain its performance and integrity at elevated temperatures. In many applications, particularly those in electronic devices, materials often encounter variations in temperature due to energy flow or external conditions. If a conductive film degrades under heat, it can lead to failures or reduced efficiency.
To achieve high thermal stability, manufacturers focus on using heat-resistant polymers and optimizing the formulation of conductive additives. Films with good thermal stability can withstand high processing temperatures during manufacturing and maintain functionality in operational conditions.
Production Methods
Production methods for conductive plastic film are critical as they directly impact the material's properties and its overall performance in various applications. The techniques employed in manufacturing these films can influence electrical conductivity, mechanical strength, and durability. In this section, we will cover three primary production methods: extrusion techniques, coating processes, and chemical vapor deposition. Each method offers unique advantages and considerations that contribute to the effectiveness of conductive plastic films across diverse industries.
Extrusion Techniques
Extrusion techniques are among the most widely used methods for producing conductive plastic film. This process involves forcing a heated mixture of base polymers and conductive additives through a die to create thin sheets or films. One of the primary benefits of extrusion is its efficiency. It allows for continuous production, resulting in lower production costs and higher output.
Extrusion can be finely tuned to produce films with specific thicknesses, which is essential depending on their intended use. A thinner film may be required for applications in flexible electronics, whereas thicker films could be beneficial in energy storage devices to enhance mechanical properties.
The choice of polymers and the type of conductive filler significantly determine the final film's conductivity. Common fillers include carbon black or metal particles, which enhance the material's electrical properties. Adjustments in processing parameters, such as temperature and extrusion speed, can also impact how well the additives are integrated, affecting the performance features of the resultant films.
Coating Processes
Coating processes involve applying a conductive layer onto a substrate material. This method is particularly beneficial for imparting conductivity to non-conductive base materials. Techniques such as dip coating, spray coating, or roll-to-roll coating are employed, depending on the desired thickness and uniformity of the conductive film.
One of the key advantages of coating processes is the versatility they offer. They can be used to modify existing materials, enabling manufacturers to enhance the properties of less expensive or less functional substrates without starting from scratch. This capability is particularly important in industries where cost-efficiency is vital, such as in consumer electronics.
Careful control of the coating parameters is essential, as it can have a significant impact on factors like adhesion and conductivity. The choice of coating solution also plays an important role, with aqueous or solvent-based solutions being common options. The final performance of the coated films must meet the specific requirements of their applications, such as flexibility or transparency.
Chemical Vapor Deposition
Chemical vapor deposition (CVD) is a sophisticated production method used for applying thin conductive films. This technique involves the chemical reaction of gaseous precursors to create a solid film on a substrate. CVD is well-regarded for producing films with excellent uniformity and purity, making it suitable for high-performance applications.
One of the primary benefits of CVD lies in its ability to deposit conductive materials at atomic or molecular levels. This precision can lead to films that exhibit remarkable electrical properties. Additionally, CVD films can be applied to intricate shapes and surfaces, making them ideal for complex electronic components.
However, the costs associated with CVD can be higher compared to other production methods. The equipment needed for this process requires significant investment and maintenance. Moreover, the skill level required to operate CVD systems demands specialized training, which can complicate implementation in some settings.
"The method selected for production can substantially influence not only the function but also the sustainability of conductive plastic films across various industries."
In summary, the choice of production method plays a vital role in defining the quality and applicability of conductive plastic films. Extrusion techniques offer cost-effective solutions for high-volume production, coating processes provide versatility for enhancing existing materials, and chemical vapor deposition allows for precision and performance in specialized applications. Each method has its unique place in the market, catering to the diverse demands of consumers and industries alike.
Applications of Conductive Plastic Film
The applications of conductive plastic film span a diverse range of industries. Their significance lies in the unique properties of conductive plastics, which make them suitable for various technological advancements. This section explores how these films are pivotal in transforming multiple sectors by improving functionality, efficiency, and sustainability.
Consumer Electronics
In consumer electronics, conductive plastic film plays a crucial role. It is used in touchscreens, flexible circuit boards, and other vital components. The films' lightweight nature contributes to the design of slim and portable devices. For example, smartphones and tablets benefit from the enhanced flexibility and durability that conductive plastics offer. Moreover, these films can reduce production costs while improving performance. Their application brings about a faster response time in touch interfaces, which is a key factor in user satisfaction.
Flexible Displays
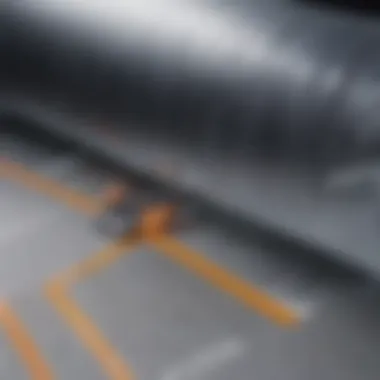
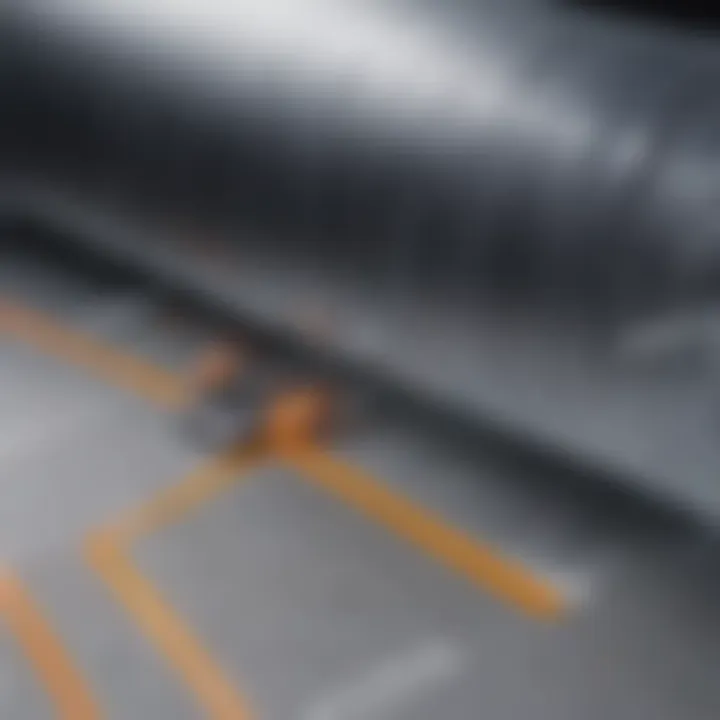
Flexible displays are another promising application. Conductive plastic films enable screens that can bend and conform to various shapes. This flexibility revolutionizes the design of devices, allowing for innovative products like rollable TVs and wearable tech. The films not only provide electrical connectivity but also contribute to the overall lightweight properties of displays. As the demand for adaptable technology increases, conductive plastics are positioned to meet these needs effectively.
Energy Storage Devices
In the sector of energy storage, conductive plastic films are used in batteries and supercapacitors. Their conductivity enhances the efficiency of charge and discharge cycles. By integrating conductive plastics, manufacturers can create devices that are more compact, with improved performance metrics. This is especially important for electric vehicles, where weight and space are critical. Furthermore, the use of these films can lead to an increase in the cycle life of the energy storage systems, promoting sustainability in technology.
Biomedicine Applications
Biomedicine is another field where conductive plastic films show significant promise. These films are utilized in medical sensors, wearable health monitors, and implants. The ability to create flexible and biocompatible devices opens new possibilities for patient monitoring and health diagnostics. Conductive plastics in biomedicine can lead to better integration with the human body, enhancing comfort and functionality. The films also allow for the development of disposable devices that maintain sterility, which is essential in healthcare settings.
"Conductive plastic films are at the forefront of technological innovation, transforming key industries and enhancing everyday products."
Market Trends and Future Outlook
The landscape of conductive plastic film is evolving. Understanding the market trends and future outlook is crucial for stakeholders, investors, and businesses involved in this field. The continuous demand for innovative materials that offer flexibility, durability, and conductivity drives research and production. The application of conductive plastic film across various sectors, such as electronics, automotive, and healthcare, highlights its versatility and transformative potential.
Emerging Markets
Emerging markets present significant opportunities for conductive plastic film. Regions such as Asia-Pacific are witnessing rapid technological advancements. Countries like China and India show increased spending on electronics and renewable energy solutions. These developments stimulate the demand for advanced materials, including conductive plastics. Moreover, the flexible nature of this film meets the requirements of various applications, from touchscreens to solar cells. This growing interest creates a fertile ground for manufacturers and suppliers to introduce innovative products and expand their market presence.
Research and Development Directions
In the field of conductive plastic film, research and development is a critical driver of advancement. Current focus areas include enhancing electrical conductivity, improving mechanical properties, and exploring new polymer blends. Scientists are engaging in interdisciplinary collaboration, integrating insights from materials science, chemistry, and engineering. This collaboration fosters innovation in production techniques as well. The emergence of nanotechnology, for instance, has opened avenues for achieving superior conductivity and functionality. Companies investing in R&D can gain a competitive edge, making this an essential focus for future progress.
Sustainability Considerations
Sustainability has become a vital consideration in the production and application of conductive plastic films. Concerns about plastic waste and environmental impact are prompting manufacturers to adopt greener practices. Research is underway to develop biodegradable conductive films. These films could mitigate ecological footprint while maintaining functionality. Furthermore, companies face pressure to comply with regulatory standards on sustainability. Adopting eco-friendly materials not only meets consumer demand for responsible manufacturing but also enhances brand reputation. Thus, sustainability will play a significant role in shaping the future trajectory of the conductive plastic film market.
Challenges and Limitations
Understanding the challenges and limitations of conductive plastic film is vital for both its development and practical applications. While this material offers significant advantages, several hurdles must be addressed to fully realize its potential. These challenges can influence manufacturing processes, performance in various conditions, and the overall sustainability of conductive plastic films. Properly addressing these issues not only improves the material's functionalities but also broadens its market appeal and usage.
Durability Issues
Durability is a critical factor when considering any material for practical applications. Conductive plastic films can face various threats that impact their longevity. These include mechanical stress, environmental exposure, and exposure to chemicals. Often, over time, the conductivity may decrease as a result of structural degradation.
Manufacturers are actively seeking to enhance durability through various means, such as optimizing the polymer matrix and experimenting with different conductive additives. The challenge remains to strike a balance between flexibility and strength. Many users require films to flex without breaking, but this flexibility can result in wear and tear with prolonged use.
Cost Factors
Cost is an ever-present consideration in material science. The production of conductive plastic films can sometimes be more expensive than traditional materials. This is especially true when utilizing high-quality conductive additives or advanced manufacturing techniques. Both factors impact the final price point, which might limit the accessibility and adoption of this technology.
Budget-conscious companies might avoid using high-performance conductive plastic films due to their price. This reluctance can stall innovative applications in sectors like consumer electronics or biomedicine. It is crucial for ongoing research to focus on cost-efficient production methods that do no compromise on quality.
Environmental Impact
The environmental impact is another essential factor to consider. The production and disposal processes for conductive plastic films can pose environmental challenges. For instance, the polymers involved might not decompose easily, contributing to plastic waste. Furthermore, the extraction of raw materials for these films may also have detrimental environmental effects.
As sustainability becomes increasingly vital for consumers and researchers, there is a pressing need to ensure that conductive plastic films adhere to environmental standards. Efforts are being put into developing biodegradable alternatives and recycling processes. Addressing these environmental concerns will be crucial not only for regulatory compliance but also for appealing to a socially conscious market.
"In the pursuit of innovation, it is imperative to not lose sight of sustainability and ethical practices in production."
Comparative Analysis with Other Materials
The comparative analysis of conductive plastic film with other material classes is significant in understanding its unique properties and advantages. It allows for a critical evaluation of how conductive plastics measure against traditional materials like metals, carbon-based substances, and ceramics. Each material presents distinct benefits and limitations that influence their application and functionality across various industries. Given the rapid advancements in technology, such analysis is also crucial in guiding future research and development with a focus on efficiency, sustainability, and performance.
Metal Conductors
Metal conductors have long been the standard in the field of conductivity. Materials like copper and aluminum offer excellent electrical conductivity, making them the first choice for many applications.
Benefits of Metal Conductors:
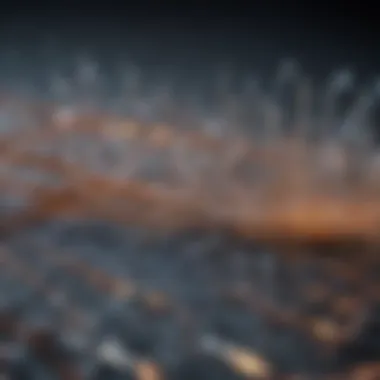
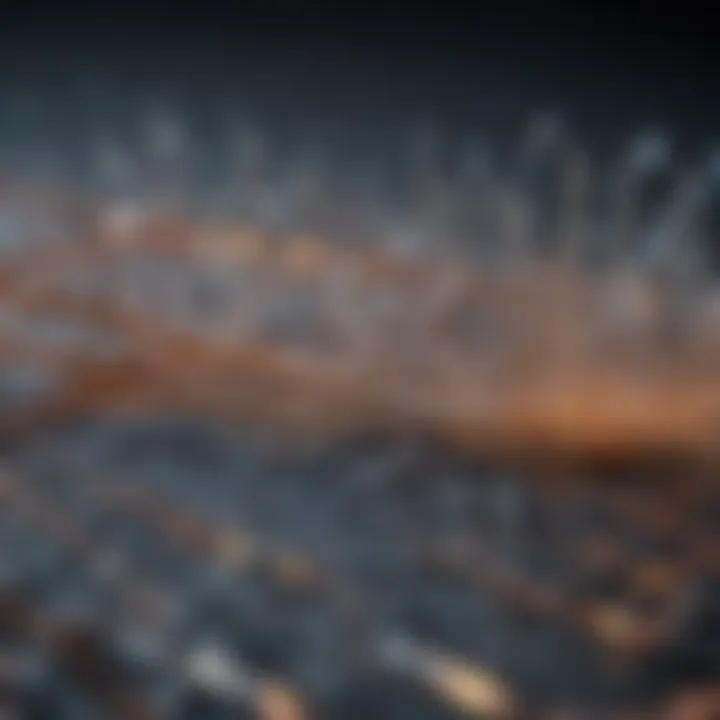
- High electrical conductivity
- Robust mechanical strength
- Well-established manufacturing processes
However, they do have drawbacks. Metals are generally heavier than conductive plastics and can also be prone to corrosion over time. Moreover, their rigidity can pose challenges for applications requiring flexibility. The production process of metals typically entails high energy consumption and environmental impact, which conductive plastics can mitigate due to their lighter weight and potentially lower manufacturing costs.
Carbon-Based Materials
Carbon-based materials, such as graphene and carbon nanotubes, have emerged as strong contenders in the field of conductive materials. These materials are known for their impressive electrical performance and light weight.
Advantages of Carbon-Based Materials:
- Exceptional electrical conductivity
- High mechanical strength and flexibility
- Lightweight characteristics
Nonetheless, carbon-based solutions can be expensive and often face challenges in mass production. The complexity in their processing can lead to inconsistent quality, limiting their use in commercial applications. In contrast, conductive plastics can provide a more stable and cost-effective alternative for many applications.
Ceramics
Ceramics are often regarded for their stability and resistance to heat. They can be designed as conductive materials, offering unique properties in specialized situations such as insulators and capacitors.
Key Points about Ceramics:
- Thermal stability
- High strength-to-weight ratio
- Excellent wear resistance
However, ceramics often lack the necessary flexibility and can be brittle, which makes them less suitable for dynamic applications that require movement. Conductive plastic films present a solution in these areas, providing a balance of conductivity and flexibility which ceramics cannot achieve.
The comparative assessment of conductive plastics against metals, carbon-based materials, and ceramics shows how each material has strengths and weaknesses affecting their applications.
In summary, while metal conductors, carbon-based materials, and ceramics have established roles in various applications, conductive plastic film stands out for its combination of conductivity, flexibility, and lower cost, thus proposing new opportunities in design and use across different industries.
Regulatory Compliance and Standards
Regulatory compliance and standards play a vital role in the manufacturing and application of conductive plastic film. This aspect ensures that the materials used and the final products meet specific requirements essential for quality, safety, and performance. Adhering to these guidelines helps foster trust and reliability in the industries that rely on conductive plastic films.
Industry Standards
Industry standards encompass guidelines and specifications developed by organizations such as the International Electrotechnical Commission (IEC) and ASTM International. These standards are critical for ensuring that conductive plastic films maintain consistent quality and performance across different applications.
Some key elements include:
- Material Composition: Standards specify acceptable ratios of conductive materials and base polymers. This ensures uniform conductivity across shifts in production.
- Performance Criteria: Conductive plastic films must demonstrate certain levels of electrical conductivity, mechanical strength, and thermal stability. Compliance with these metrics can boost consumer confidence.
- Testing Methods: Industry standards dictate the methodologies employed for testing the performance and durability of these films. This consistency aids industries in comparing products effectively.
Compliance with industry standards not only enhances product quality but also mitigates risks associated with product failures.
Safety Regulations
Safety regulations are paramount in the development and use of conductive plastic films, especially given their applications in sensitive sectors such as electronics and biomedicine. Proper adherence to safety guidelines ensures that these materials pose minimal risk to users and the environment.
Important considerations include:
- Hazard Communication: Manufacturers are required to convey information regarding potential risks associated with the materials used in conductive plastic film. This might involve labeling according to the Globally Harmonized System (GHS).
- Environmental Standards: Regulations concerning waste disposal and recycling are crucial. Conductive plastic films must comply with local and international environmental standards to ensure sustainability and reduce negative impacts on ecosystems.
- Occupational Safety: Compliance with OSHA (Occupational Safety and Health Administration) regulations ensures the safety of workers involved in the production and handling of conductive plastic films. Proper training and protective equipment are necessitated.
Adopting rigorous regulatory compliance not only protects public health but also elevates the credibility of manufacturers in the market.
Regulatory compliance and standards are foundational to the development and application of conductive plastic films. They safeguard quality and safety while enabling industries to harness the material's full potential effectively.
Culmination
The conclusion of this article serves to encapsulate the multitude of insights and discussions regarding conductive plastic film. In many ways, it highlights the unique position this material holds in modern industries and research fields. As intricate as its composition, the multifaceted properties of conductive plastic film make it a pivotal player in fields such as electronics, energy storage, and biomedicine.
Summary of Key Points
- Definition and Importance: Conductive plastic film is not merely a functional material but a transformative one that bridges the gap between traditional plastics and advanced electronic applications.
- Diverse Applications: Its use spans from consumer electronics to innovative energy storage systems, showcasing its versatility and adaptability to meet growing industry demands.
- Production Techniques: Various methods, such as extrusion and coating, ensure that the film is produced efficiently while maintaining necessary properties.
- Market Trends: The market for conductive plastic film exhibits a growth trajectory influenced by technological advancements and sustainability efforts.
- Challenges: Despite its advantages, there are issues related to durability and cost that need to be addressed for wider adoption.
Final Thoughts
In summary, conductive plastic film represents a significant step forward in material science, marrying functionality with adaptability. Awareness of its characteristics and applications is crucial for researchers, students, and professionals aiming to leverage this technology. Understanding regulatory standards and environmental considerations will ensure its responsible development and use. As industries continue to evolve towards more efficient and sustainable practices, conductive plastic film is well-positioned to play a key role in shaping the future of technology and innovation.
"The path forward for conductive plastic film is filled with challenges and opportunities, underscoring its dual role as both a solution provider and a catalyst for further research and development."
By exploring the insights provided in this article, readers can grasp not only the significance of conductive plastic film but also its potential impact on future advancements and global trends.