Mould Fabrication Techniques and Applications
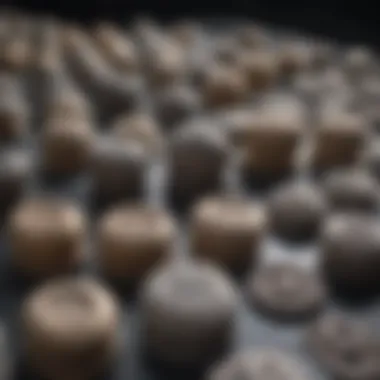
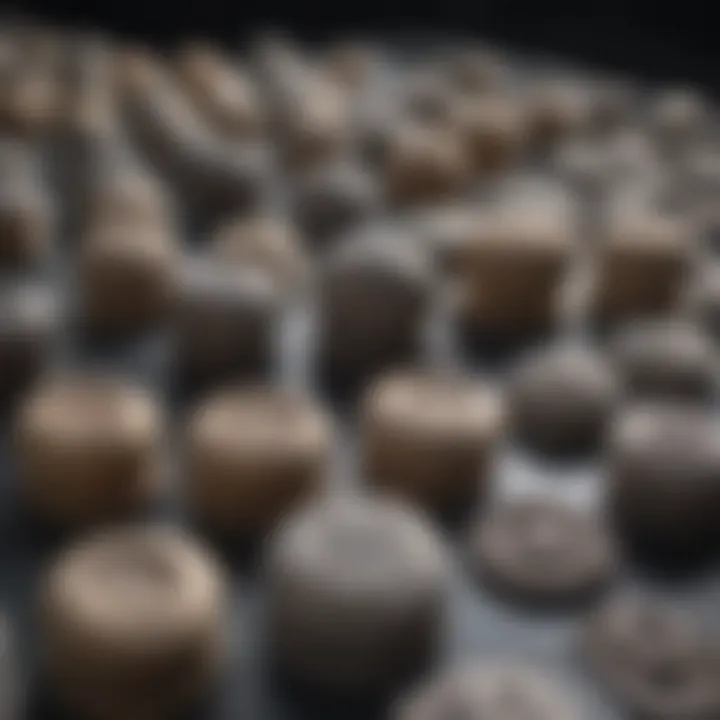
Intro
The manufacturing landscape is as diverse as it is intricate, with mould fabrication standing as a cornerstone in various industries. Mould fabrication embodies both art and science, merging engineering precision with creative design. In this exploration, we will traverse the pathways of techniques, materials, and applications that define this crucial aspect of production.
While the focus might primarily be on plastics and metals, it’s vital to recognize that moulds influence a broad range of sectors, from aerospace to consumer goods. The insights gleaned here will resonate with an array of professionals: engineers, designers, and decision-makers.
As we peel back the layers of this topic, expect to discover how technological advancements are reshaping the mould fabrication industry, enhancing both quality and efficiency. Prepare for a nuanced discussion that’s not merely theoretical but deeply rooted in applicable knowledge and real-world implications.
"The mould is the invisible hand of production, shaping not just the product, but the industry's future itself."
Let’s embark on this journey to uncover the techniques and methodologies that make mould fabrication an indispensable ally in manufacturing processes.
Prelude to Mould Fabrication
Mould fabrication stands as a cornerstone of modern manufacturing, with its critical role in the creation of products that span various industries—from consumer goods to aerospace components. Understanding its importance opens the door to appreciating the complexities of production processes. Moulds serve not merely as vessels for shaping materials but as pivotal tools in enhancing efficiency, ensuring quality, and unlocking innovative design possibilities. As we embark on this exploration, it’s essential to grasp how mould fabrication both influences and complements the broader spectrum of manufacturing.
Definition and Importance
At its core, mould fabrication is the process through which molds are created for manufacturing purposes. These molds can shape materials, typically metals or plastics, into precise forms that fulfil specific functional or aesthetic requirements. In simpler terms, moulds are to manufacturing what cookie cutters are to baking; without them, achieving uniformity and design intentions would be a daunting task.
The importance of mould fabrication can’t be overstated. In industries such as automotive and consumer electronics, the precision and consistency that well-fabricated moulds provide lead directly to improved product quality. Consider how a tiny imperfection in a mould can lead to significant flaws in the final product—rendering it unsuitable for market release and financially draining for a company. Thus, investing in quality mould fabrication translates into substantial long-term savings and enhances a company’s reputation.
"Quality is not an act, it is a habit." - Aristotle
This application of mould fabrication becomes even more significant as technology integrates into manufacturing. For example, advancements like 3D printing not only enhance the speed of producing moulds but also allow for complex geometries that traditional methods may struggle with. As we delve deeper into this exploration, we’ll uncover how such innovations are reshaping our expectations and capabilities in mould fabrication.
Historical Context
Understanding the historical context of mould fabrication sheds light on its evolution and the technological advancements that have driven its transformation. The journey starts way back in ancient times, when artisans originally carved simple shapes into materials like clay and stone. Over the centuries, these rudimentary techniques laid the groundwork for more sophisticated methods.
The Industrial Revolution marked a significant turning point. During this period, the advent of mechanized production brought about more standardized practices in mould design and manufacture. Factories began employing specialized machines, resulting in faster production times and higher volumes—crucial factors in meeting the rising demand for various goods.
In the latter half of the 20th century, digital technologies started making waves. Computer Numerical Control (CNC) machining emerged, allowing for unparalleled precision and complexity in mould creation. Today, we stand on the brink of even more advancements, such as smart manufacturing and lightweighting—concepts that underscore the dynamic nature of mould fabrication and its ongoing importance across industries.
In summary, the history of mould fabrication is a testament to human ingenuity and the relentless pursuit of improvement in manufacturing processes. Recognizing this historical narrative not only contextualizes current practices but also hints at future innovations that could further revolutionize the way we produce.
Fundamental Concepts
Understanding fundamental concepts in mould fabrication is crucial for anyone engaged in the manufacturing sector. These principles not only underpin the entire process but also directly influence the efficiency, quality, and cost-effectiveness of produced parts. Familiarity with these concepts equips professionals with the tools they need to make informed decisions regarding mould design, materials selection, and fabrication techniques.
Basic Principles of Mould Design
In mould design, a correct approach can save time and resources. The main goal is to create a mould that can produce consistent and high-quality parts while minimizing waste. Here are some basic principles:
- Functionality: The mould must fulfill its intended purpose effectively, ensuring that it can produce the designed component accurately.
- Material Compatibility: Choosing materials that work harmoniously with the final product is key. Different plastics or metals have specific requirements.
- Cooling System Design: An effective cooling system can drastically reduce cycle times. Water or oil channels should be designed to ensure even cooling of the mould.
- Draft Angles: Implementing proper draft angles allows for easier ejection of the part from the mould, reducing the chance of damaging either the part or the mould.
- Surface Finish: The finish quality impacts both the appearance and functionality of the final product. High-quality surface finishes reduce the need for additional treatments.
By adhering to these principles, designers can create highly efficient moulds that cater to the specific needs of their manufacturing operations.
Key Terminologies
In the mould fabrication realm, there are numerous terms that are essential to understand:
- Thermoplastic: Plastics that can be melted and remolded, making them ideal for processes like injection moulding.
- Cavity: The space within the mould where the component is formed. Moulds can have multiple cavities to increase production efficiency.
- Core: The part of the mould that shapes the interior features of the component, often working in conjunction with the cavity.
- Shrinkage Rate: The percentage by which a material contracts as it cools. Knowing this helps in accounting for dimensional accuracy.
- Cycle Time: The total time needed to complete one production cycle, critical for efficiency evaluation.
"Understanding the terminology is like knowing the language—without it, the conversation about mould design and fabrication becomes quite baffling."
Grasping these terminologies can significantly streamline communication among professionals and enhance the overall effectiveness of the mould fabrication process. \n The significance of these fundamental concepts cannot be overstated. They lay the groundwork for success in mould fabrication and serve as an indispensable reference for both novices and seasoned industry veterans.
Materials Used in Mould Fabrication
Understanding the materials employed in mould fabrication is essential to grasping the broader implications of this manufacturing process. The choice of materials not only influences the durability and efficacy of moulds but also plays a pivotal role in enhancing production efficiency and reducing waste. Each material comes with its own set of advantages and limitations, which must be thoroughly considered to meet specific project requirements and application needs. Below are the primary types of moulding materials and an analysis of their distinct characteristics.
Types of Moulding Materials
Metals
Metals are a cornerstone in the realm of mould fabrication. Their strength and ability to withstand high temperatures make them incredibly valuable in various applications. Steel, for instance, is often the go-to option due to its robustness and wear resistance. Moulds made from stainless steel exhibit superb corrosion resistance, making them ideal in industries where hygiene is paramount, such as food and pharmaceuticals.
One unique feature of metal moulds is their heat conductivity, enabling rapid cooling and increased production rates. However, it's worth noting that metal moulds can be costly to produce, particularly for complex designs. Despite this, their long lifespan and ability to yield high-quality parts can justify the initial investment.
Plastics
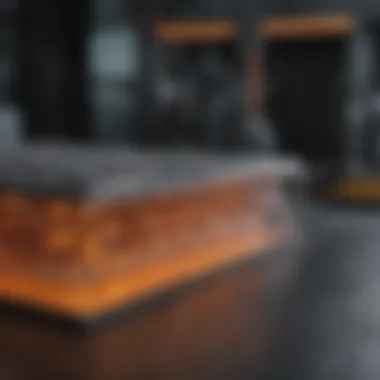
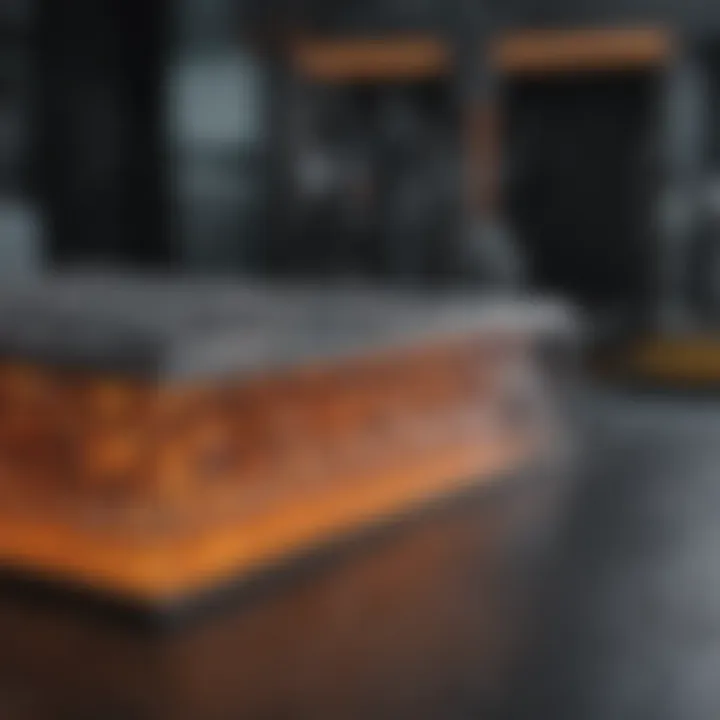
Plastics have carved out a significant niche in the mould fabrication arena, primarily due to their versatility and lower production costs. Thermoplastics like polyethylene and polypropylene are widely used because they can easily be reheated and reshaped. This property allows manufacturers to produce intricate designs without breaking the bank.
Plastic moulds can also be lighter than their metal counterparts, thus simplifying handling and installation. However, they may not be suitable for high-volume production due to their durability concerns. Over time, some plastics can warp or degrade under high temperatures, making them less viable for extensive use.
Composites
Composites represent an emerging category in mould fabrication, blending various materials to achieve superior performance. By combining fibers with resin, manufacturers can create moulds that are both lightweight and incredibly strong. Carbon fiber composites are popular for their high strength-to-weight ratio and impressive rigidity.
The unique aspect of composites lies in their customizable nature. Depending on the application needs, manufacturers can adjust the properties of the composite materials to enhance specific features such as impact resistance or thermal stability. Nevertheless, the higher cost and complexity of production might limit their use to specialized applications, like aerospace or high-performance automotive sectors.
Material Properties and Selection Criteria
Choosing the right material for mould fabrication involves understanding a set of material properties:
- Durability: How long will the mould last under operational conditions?
- Temperature Resistance: Can the material withstand the operational temperatures without degrading?
- Cost: What is the budget for materials versus the long-term investment?
- Lead Time: How long will it take to fabricate the mould using the chosen material?
- Application Specifics: Does the application demand specific properties like biocompatibility or conductivity?
Selecting the right material can make the difference between a successful project and an expensive, failed venture. It's critical for engineers and designers to weigh these factors carefully to optimize their mould fabrication processes.
Mould Fabrication Techniques
Mould fabrication techniques form the backbone of modern manufacturing practices. These methods not only determine the efficiency of production but also significantly impact the quality of the finished products. By understanding the nuances involved in each technique, professionals can make informed decisions that optimize performance and reduce waste. The landscape of mould fabrication is evolving, influenced by advances in technology and materials. Hence, it is crucial for students, researchers, and practitioners to familiarize themselves with these techniques, grasping their relevance in both contemporary practice and future trends.
CNC Machining
CNC (Computer Numerical Control) machining is a cornerstone of modern mould fabrication. This technique utilizes computer software to control tools and machinery, enhancing precision and repeatability in producing moulds. The integration of CNC technology into manufacturing has sparked a revolution that allows for intricate designs that were once considered impractical.
CNC machining’s key benefits include:
- Accuracy: Achieves tolerances of up to ±0.01 mm, ensuring precision in the final product.
- Flexibility: Allows for the quick modification of designs, making it adaptable to changing requirements.
- Efficiency: Reduces production time significantly when compared to manual machining approaches.
Despite its advantages, CNC machining does come with considerations, such as the need for skilled operators and the initial investment in machinery. Companies often weigh these factors against the long-term savings and enhancements in quality.
3D Printing and Additive Manufacturing
The rise of 3D printing marks a significant shift in mould fabrication. Unlike traditional subtractive methods, additive manufacturing builds up moulds layer by layer, allowing for complex geometries and customized designs to become a reality. This technique is particularly attractive in prototyping, where speed and intricacy are paramount.
Advantages of 3D printing in mould fabrication:
- Reduced Waste: Only the material needed is used, leading to a greener manufacturing process.
- Customization: Highly versatile, it facilitates the production of unique designs tailored to specific needs.
- Rapid Prototyping: Quick turnaround times enable faster testing and iteration, shortening product development cycles.
However, some challenges persist. Material limitations and slower production speeds compared to traditional methods can hinder widespread adoption in certain sectors.
Injection Moulding Processes
Injection moulding is arguably one of the most prevalent methods used in mould fabrication, particularly in the plastic industry. This process involves injecting molten material into a mould, allowing it to cool and solidify into the desired shape.
Key characteristics of injection moulding include:
- High Efficiency: Ideal for mass production, it can produce thousands of identical parts in a short time.
- Detail and Complexity: Capable of creating highly intricate designs with varying thicknesses and textures.
- Material Variety: Compatible with a wide range of materials, including thermoplastics and thermosets.
While injection moulding offers remarkable capabilities, it isn't without downsides. The initial mould creation can be costly, and any changes made to the design may lead to significant delays and expenses.
"Understanding the techniques of mould fabrication is crucial for harnessing their potential in innovative manufacturing solutions."
Quality Assurance in Mould Fabrication
Quality assurance in mould fabrication is the backbone of ensuring that products meet or exceed expected standards. Without proper quality checks, even the most advanced moulding techniques can lead to defects, resulting in significant financial loss and product recalls. In essence, it ensures that every mould not only functions as intended but does so consistently over time. The practices involved in quality assurance vary from thorough inspections to rigorous testing standards. Both elements are crucial for the longevity of a business's reputation and the efficiency of their production processes.
As mould fabrication is often applied in sensitive industries such as automotive, medical, and consumer products, adhering to quality assurance protocols is non-negotiable. It goes beyond just identifying and fixing issues; it fosters a culture of continuous improvement. Businesses that invest in quality assurance processes can expect reduced scrap rates, less downtime, and an overall boost in productivity—an outcome that translates directly into profitability.
Inspection Techniques
Inspection techniques play a pivotal role in the quality assurance of mould fabrication. These methods ensure that every aspect of a mould is scrutinized for potential defects. Common inspection techniques are:
- Visual Inspection: The most straightforward method, relying on the eyes of a trained technician to spot defects such as surface irregularities or misalignment.
- Dimensional Measurement: Involves using tools like calipers or coordinate measuring machines (CMM) to ensure that all dimensions meet specified tolerances.
- Non-Destructive Testing (NDT): Techniques like ultrasonic testing or X-ray imaging check the integrity of the mould without causing any damage. This is crucial for identifying internal flaws that could affect performance.
Each inspection technique brings in its strength, and often, a combination of methods is employed to ensure thoroughness.
"Quality isn’t expensive, it’s priceless." – anonymous
Testing Standards
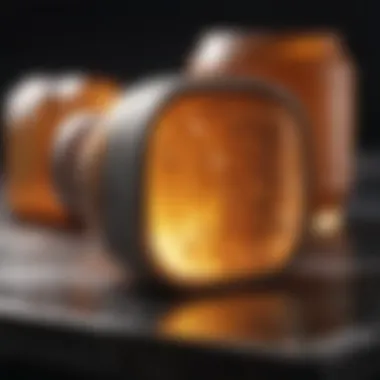
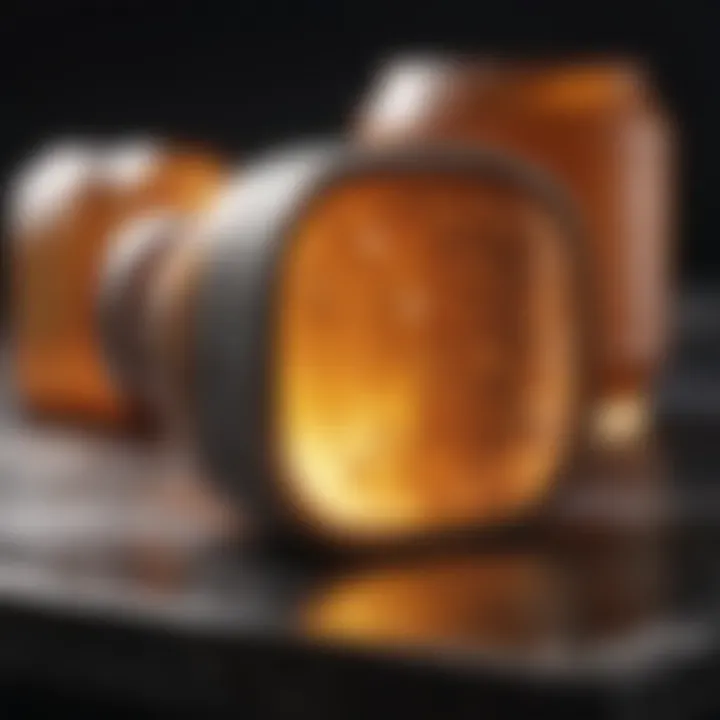
Testing standards are the guidelines that govern how moulds are evaluated for quality and safety. Adhering to these standards is crucial not only for compliance but also for maintaining competitiveness in the market. Some important testing standards include:
- ISO 9001: This internationally recognized standard ensures that organizations meet customer and other stakeholder needs while fulfilling statutory and regulatory requirements.
- ASTM Standards: Developed by ASTM International, these provide specifications on materials, products, systems, and services in various industries, including mould fabrication.
- SAE Standards: Particularly significant in the automotive field, these standards focus on the quality and performance of automotive components, inclusive of those manufactured using moulds.
Meeting these standards may require investments in both technology and training but can yield significant long-term benefits. Upholding high testing standards can not only alleviate risks of failure in the production line but also foster trust among customers, thereby enhancing brand reputation.
In summary, the value of robust quality assurance practices in mould fabrication cannot be overstated. They not only safeguard integrity and reliability but also lay the foundation for successful and sustainable manufacturing practices.
Applications of Mould Fabrication
Mould fabrication stands as a fundamental pillar in modern manufacturing, intertwining with a variety of industries to produce efficient and high-quality products. The significance of this topic within the sphere of mould fabrication cannot be overstated; it not only highlights the diverse range of applications but also illustrates the intricate details that elevate moulds from mere tools to critical enablers of innovation and design.
The applications stretch across sectors, from consumer products that populate our daily lives to advanced technologies in aerospace. This section shines a spotlight on each of these domains, revealing how mould fabrication integrates into their fabric, enhancing functionality and performance.
Through an in-depth discussion, we can delve into the benefits, considerations, and strategic elements that mould fabrication brings to the table in various industries.
Consumer Products
In the realm of consumer products, mould fabrication plays a pivotal role in shaping countless items that define our modern lifestyle. Think of the countless plastic containers, dishes, electronic housings, and toys that are manufactured, often without a second thought to the intricate processes behind their creation. These products rely heavily on the precision and repeatability that moulds provide, ensuring uniformity and quality.
Utilizing techniques such as injection moulding and blow moulding, manufacturers can produce items efficiently, reducing waste and lowering production costs. It's vital for designers to constantly consider the balance between aesthetics and functionality.
Moulds, crafted from a variety of materials including steel and aluminum, are tailored to yield high volumes of identical products, maintaining high manufacturing standards. This efficiency means that Consumer Product companies can quickly respond to market trends, as they can ramp up production or pivot designs with relative ease.
Some notable examples:
- Household items: From storage containers to kitchenware.
- Electronics: Outer casings of gadgets often produced through effective moulding processes.
- Personal care products: Various containers and applicators manufactured to enhance user convenience.
Automotive and Aerospace Industries
The significance of mould fabrication in the automotive and aerospace sectors cannot be neglected. These industries demand the highest levels of precision and safety due to the stakes involved in their operations. In automobiles, moulds are used to create complex parts that contribute to performance, such as panels, bumpers, and internal components.
Lightweight materials produced by moulding processes are essential, aiding in fuel efficiency and overall vehicle performance. Mould fabrication enables the industry to innovate with new designs, implement advanced materials like composites, and streamline production.
In aerospace, where reliability and precision are non-negotiable, moulding solutions permit the production of intricate parts that must endure extreme conditions. Materials that offer a balance between strength and weight are crucial—hence, technologies such as thermoset and thermoplastic composites are increasingly important.
Key considerations in these industries include:
- Safety Standards: Ensuring compliance with stringent regulations.
- Material Selection: Choosing appropriate materials based on performance needs.
- Custom Designs: Tailoring components to meet unique specifications of each aircraft or vehicle.
Medical Equipment Manufacturing
In the medical field, the role of mould fabrication transcends everyday manufacturing. From surgical instruments to housing for medical devices, the quality and reliability of these products can quite literally be a matter of life and death. Moulds must be designed not only for accuracy but also to comply with rigorous health and safety standards.
The applications range widely, including:
- Surgical Devices: Where precision and ergonomics are critical.
- Diagnostic Tools: Manufacturing components for equipment like MRI machines and ultrasound devices.
- Consumables: Producing disposables like syringes and surgical containers that are sterile and single-use.
Advancements in 3D printing and other innovative technologies have further revolutionized this sector. They allow for quick prototyping as well as customization of equipment, which can lead to better patient outcomes. Moreover, these practices can significantly shorten the lead time for new product development.
"Ensuring quality and adherence to standards in medical applications isn't just required; it's an ethical imperative that can directly affect patient safety."
Future Trends in Mould Fabrication
The landscape of mould fabrication is shifting, driven by the need for efficiency and precision in an increasingly competitive market. As industries evolve, so too must the methods and materials used in mould production. The emergence of new technologies and sustainable practices is not just a trend; it's becoming a fundamental component of modern manufacturing.
Emerging Technologies
Innovation is at the forefront of mould fabrication, with technologies such as 3D printing, robotics, and artificial intelligence revolutionizing the field. These advancements allow manufacturers to create highly intricate mould designs that were previously unattainable. For instance, additive manufacturing can produce complex shapes without the need for costly and time-consuming tooling changes. This has significant implications for prototyping, enabling rapid iterations and reducing lead times.
The integration of machine learning in design processes is enhancing how moulds are tested and refined. Through data analysis, manufacturers can better understand stress points and thermal responses within mould structures. This ensures that the final products are both durable and efficient, reducing waste and enhancing overall product quality.
Such technologies not only streamline the production process but also foster collaboration across different industrial sectors, paving the way for a more interconnected approach to manufacturing.
Sustainability Considerations
Sustainability is no longer an afterthought; it is integral to mould fabrication today. The manufacturing industry is feeling the heat of environmental scrutiny, and mould production is no exception. The shift towards recyclable materials and eco-friendly practices is moving full steam ahead. For instance, many companies are beginning to explore bio-based plastics that lessen environmental impact while maintaining performance efficiency.
Furthermore, energy-efficient processes are being adopted in manufacturing, minimizing the carbon footprint associated with mould fabrication. This can include employing solar energy or energy-recovery systems that capture waste heat for reuse. By embracing these sustainable practices, manufacturers are not only meeting regulatory requirements but also appealing to consumers who are increasingly prioritizing sustainability in their purchasing decisions.
Integration with Smart Manufacturing
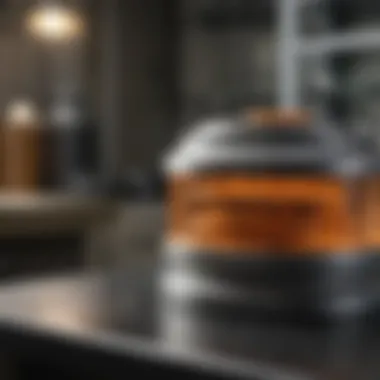
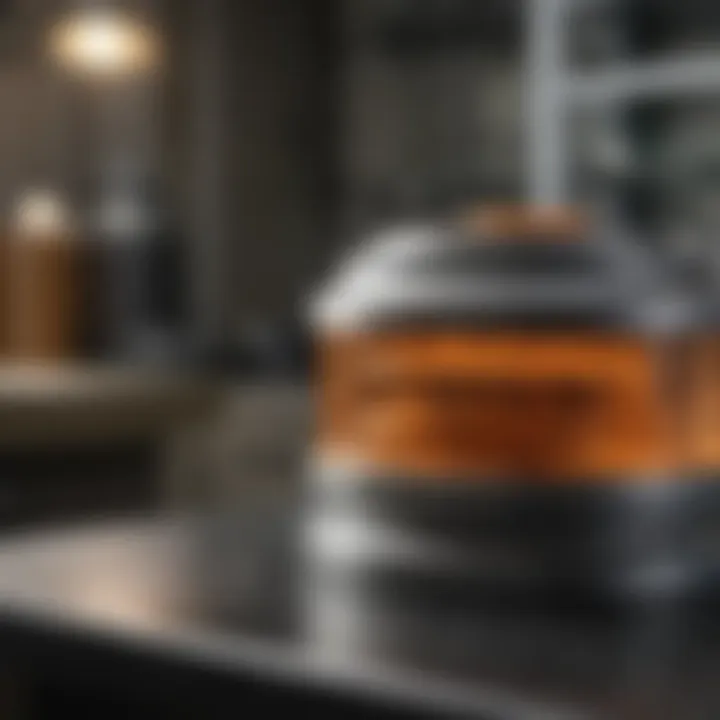
The concept of smart manufacturing is increasingly influencing mould fabrication. By incorporating Internet of Things (IoT) devices and real-time data analytics, manufacturers can monitor their production lines, ensuring optimal efficiency and minimal downtime. This connectivity provides valuable insights, allowing for predictive maintenance which delegates repairs before they become problematic.
- Key considerations in smart manufacturing include:
- Enhanced automation for precision machining.
- Real-time monitoring of mould quality through sensors.
- Streamlined supply chain management with enhanced data sharing across platforms.
As these technologies converge, mould fabrication is poised to become more agile, adaptive, and responsive to market demands. The potential for reduced costs and increased production speed will be paramount as businesses thrive on efficiency and customer satisfaction.
In summary, the future of mould fabrication is heavily intertwined with advanced technologies, sustainable practices, and smart solutions that are setting the stage for an efficient manufacturing era, where innovation meets responsibility.
By acknowledging these trends, businesses can better position themselves in an evolving market landscape, ensuring longevity and competitiveness in their operations.
Case Studies
Case studies serve as vital resources in understanding the real-world applications and implications of mould fabrication. They provide a narrative that connects theoretical concepts with practical expertise. By examining specific scenarios, we can gain insights into the effectiveness of various techniques and materials. Case studies may illuminate why a particular method was chosen or highlight unexpected challenges that arose during the production process. This detailed analysis not only enriches our comprehension of mould fabrication but also helps professionals anticipate potential obstacles and derive practical solutions.
Innovative Applications in Industry
Mould fabrication finds its relevance across several industries, showcasing innovative applications that drive efficiency and creativity. For instance, in the automotive sector, the use of complex mould designs has led to better lightweight components that improve fuel efficiency. A notable case can be seen in a project involving BMW, which integrated advanced injection moulding techniques to produce intricate dashboard elements, ultimately achieving a superior finish and functionality.
Similarly, the consumer electronics industry relies on precision moulding for products like smartphones and laptops. Apple’s meticulous approach toward mould design and fabrication has allowed the company to maintain a competitive edge, exemplified by the seamless aesthetics and high durability of its devices. These cases reveal how mould fabrication not only addresses functional requirements but also enhances product appeal and user experience.
Moreover, the medical field showcases applications that demand high precision and sterility. Companies specializing in medical devices often employ moulds made from biocompatible materials to ensure safety. For example, a study on the production of surgical instruments demonstrated that adopting innovative manufacturing techniques reduced production time and minimized waste, leading to significant cost savings.
These cases point towards a trend within mould fabrication where quality and innovation go hand in hand, indicating a shift towards a more integrated approach in manufacturing.
Lessons Learned from Past Projects
Reflecting on past projects in mould fabrication offers valuable lessons that can guide future endeavors. One significant takeaway is the importance of thorough material selection. A case involving the production of automotive components revealed that choosing the wrong plastic could lead to unexpected failures, undermining both safety and performance. The team learned to prioritize rigorous testing of materials prior to integration into the production cycle.
Additionally, the significance of robust design processes became evident during a cross-industry study. A project aimed at creating a new mould for a consumer product faced delays due to insufficient simulation testing. As a result, the final product did not meet quality standards. This led to an overhaul of their design protocol, shifting emphasis to comprehensive simulations and prototypes in the early stages of development.
Furthermore, case analyses often highlight the role of collaboration among various stakeholders. For instance, a successful appliance manufacturing project underscored how involving engineers, designers, and production teams in the decision-making process improved both product quality and team efficiency. This practice of collective input fostered an environment where innovative ideas could flourish and led to a faster turnaround in delivering products to the market.
Lessons gathered from past experiences not only enhance the understanding of challenges faced but also pave the way for future advances in mould fabrication, driving the industry forward.
Challenges in Mould Fabrication
In the realm of mould fabrication, the intricacies and hurdles involved play a pivotal role in shaping production efficiency and product quality. Addressing these challenges ensures that manufacturers can produce moulds that meet stringent standards while also navigating the complexities of modern production. By delving into the challenges, we gain insights into the constraints that shape the industry and how innovative solutions can lead to enhanced methodologies.
Technical Limitations
One significant obstacle in mould fabrication is the technical limitations inherent in the materials and processes used. For instance, the precision required in machining moulds can be stymied by the limits of some traditional machining methods. Tool wear, for instance, compromises the accuracy of mould features over time. If manufacturers are not constantly aware of this, they can end up with moulds that don’t meet specifications, necessitating costly reworks.
Moreover, the complexity of certain designs can exceed the capabilities of standard manufacturing equipment. Moulds for intricate parts or those with complex geometries often require bespoke solutions, which can escalate costs significantly. In many cases, a deeper understanding of the material properties of metals, plastics, and composites used can lead to better decisions in design and manufacturing techniques.
"Innovation lies not in avoiding limitations but in creatively working around them."
Additionally, as the demand for more sustainable manufacturing grows, many companies face technical barriers when trying to integrate eco-friendly materials into traditional mould fabrication techniques. The challenge, therefore, rests upon manufacturers to innovate continuously, possibly leading to the development and adoption of new technologies, like advanced additive manufacturing methods.
Economic Factors
Beyond technical issues, economic factors also heavily impact mould fabrication. Cost considerations run through nearly every decision made within this field. When manufacturers face tight profit margins, they need to balance quality with cost efficiency. For example, the initial cost of high-end CNC machinery may seem daunting, yet it often pays off by significantly reducing production time and waste in the long run.
Furthermore, fluctuating raw material prices can complicate budgeting and forecasting. For instance, when the price of steel or specialized alloys rises sharply, manufacturers might be compelled to either absorb the costs or pass them onto customers, potentially losing their competitive edge.
Additionally, market demands can shift unpredictably, necessitating fast adaptation in production to meet new demands without stretching resources too thin. In such scenarios, firms must evaluate whether to invest in new mould technologies or enhance existing capabilities, a decision that requires thorough market analysis and risk evaluation.
Epilogue
Mould fabrication stands at the intersection of creativity and engineering, encompassing a wide array of techniques and materials that drive modern manufacturing. This discussion encapsulates the critical roles these moulds play in various industries, illustrating their profound impact on product quality and production efficiency.
Summary of Key Points
In this article, we covered several essential areas, including:
- Definition and Importance: Mould fabrication is not just a procedure; it’s the backbone of product realization across industries like automotive, consumer goods, and healthcare.
- Techniques and Innovations: We examined numerous fabrication methods, from traditional CNC machining to cutting-edge 3D printing technologies, showcasing how each technique serves unique demands.
- Material Choices: The selection of materials—be it metals, plastics, or composites—highly influences the final product's attributes. Each comes with its merits and challenges, making material knowledge vital for practitioners.
- Quality Assurance: Emphasizing the significance of inspection techniques and testing standards ensures that produced moulds meet stringent quality benchmarks, thereby reducing waste and optimizing costs.
- Future Prospects: Emerging technologies and sustainability considerations pave the way for innovation in mould fabrication, hinting at a greener and more efficient manufacturing landscape.
Implications for Future Research
As the industry continues to evolve, several avenues warrant further inquiry:
- Integration of Smart Technologies: The incorporation of IoT and AI into mould fabrication can revolutionize the production process. Future research could explore how these technologies enhance decision-making and operational efficiency.
- Sustainable Practices: Given the increasing emphasis on sustainability, research focusing on eco-friendly material substitutes and manufacturing processes is crucial. Insights into reducing carbon footprints while maintaining quality could set new benchmarks in the field.
- Advanced Simulation Techniques: The role of simulation in mould design and optimization is an area ripe for exploration. Innovative software capable of predicting mould behavior under various conditions may bring enhanced precision and efficiency.
"With continuous advancements, the future of mould fabrication harbors immense potential, inviting professionals to innovate and redefine standards."
Through this article, readers should leave with a comprehensive understanding of mould fabrication’s intricate elements and its significance in modern manufacturing. This knowledge not only empowers industry professionals but also encourages aspiring researchers to delve deeper into emerging frontiers.