Parylene: A Comprehensive Overview of Its Properties and Uses
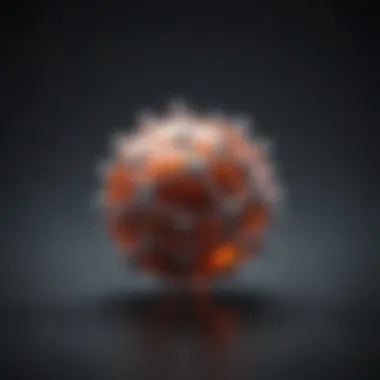
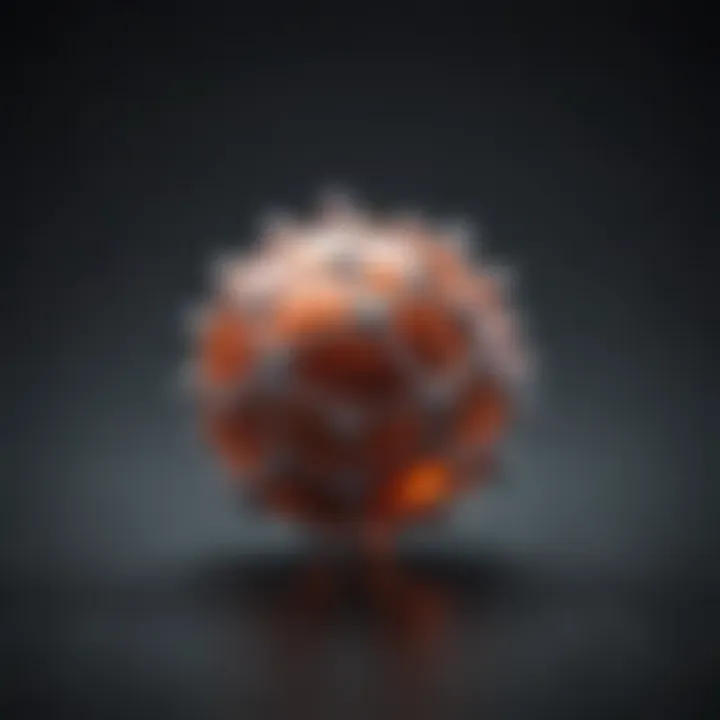
Intro
Parylene is a polymer that has gained attention for its unique properties and versatile applications across various sectors. Known mainly for its thin-film qualities, Parylene serves crucial roles in electronics, biomedical applications, and the aerospace industry.
This comprehensive overview aims to illuminate the facets of Parylene, starting with its chemical structure, then moving on to deposition methods, characteristics, and specific use cases. We will also delve into environmental considerations and future research avenues to provide an in-depth guide suitable for students, researchers, educators, and professionals alike.
Intro to Parylene
The significance of understanding parylene is rooted in its wide-ranging applications and remarkable properties. Parylene, a type of polymer, has emerged as a crucial material in various industries, influencing how products are designed and function. This section serves as a gateway to unraveling the complexities surrounding parylene, delving into its definition, historical context, and modern-day relevance.
Definition of Parylene
Parylene is a generic name for a range of poly(xylylene) polymers. It is known for its thin-film deposition capabilities that provide exceptional barrier properties. These polymers are typically deposited as a vapor and then polymerize onto surfaces, forming a highly conformal coating. This process ensures that even irregular or complex shapes are uniformly coated. Parylene exhibits characteristics such as flexibility, chemical resistance, and electrical insulation.
Historical Background
The development of parylene dates back to the 1960s, when it was first introduced by chemists at Union Carbide Corporation. Its unique deposition process was designed to address the limitations of existing protective coatings which often failed in demanding environments. Over the years, parylene has evolved significantly. Today, various types of parylene exist, each tailored for specific applications.
Importance in Modern Science
Parylene holds significant importance in contemporary applications due to its versatility and effectiveness. In the electronics sector, parylene is used for insulating and encapsulating delicate components, protecting them from moisture and contaminants. In the biomedical field, it serves as a vital material in medical device coatings and drug delivery systems, enhancing biocompatibility.
The value of parylene continues to grow, especially as researchers explore its potential in new areas such as nanotechnology and advanced manufacturing. As the demand for materials that can withstand extreme environments increases, understanding parylene's properties becomes crucial for innovation and development in various scientific fields.
Chemical Structure of Parylene
The chemical structure of parylene plays a crucial role in understanding its distinctive properties and applications. Parylene is a type of polymer that is known for its versatility across various industries. The unique arrangement of its monomers leads to specific behaviors and characteristics that make it suitable for different applications, particularly in electronics and biomedical fields.
Monomer and Polymerization
Parylene is derived from a dimeric precursor commonly known as p-xylylene. The polymerization process involves the conversion of the p-xylylene dimer into a polymer through a chemical vapor deposition, or CVD, method. In this process, the dimer is vaporized and then polymerized onto substrates at room temperature. This deposition allows for a consistent and uniform coating on complex geometries and intricate shapes.
The significance of the monomer lies in its structure, which affects how well the final polymer performs in various conditions. The polymerization leads to a highly stable and versatile polymer with excellent resistance to moisture, chemicals, and other detrimental environmental factors.
Types of Parylene
There are different types of parylene, each characterized by slight variations in their chemical structures, leading to unique properties. Here are the primary classifications:
Poly(p-xylylene)
Poly(p-xylylene) is perhaps the most widely used form of parylene. Its main characteristic is a high degree of stability coupled with exceptional barrier properties. This particular polymer is essential for protecting sensitive electronic components from moisture and corrosion. The uniform coating achieved with this type of parylene provides a dependable insulating layer that can withstand challenging environmental conditions. It is often chosen for electronic applications due to its low dielectric constant and high resistivity.
Poly(m-xylylene)

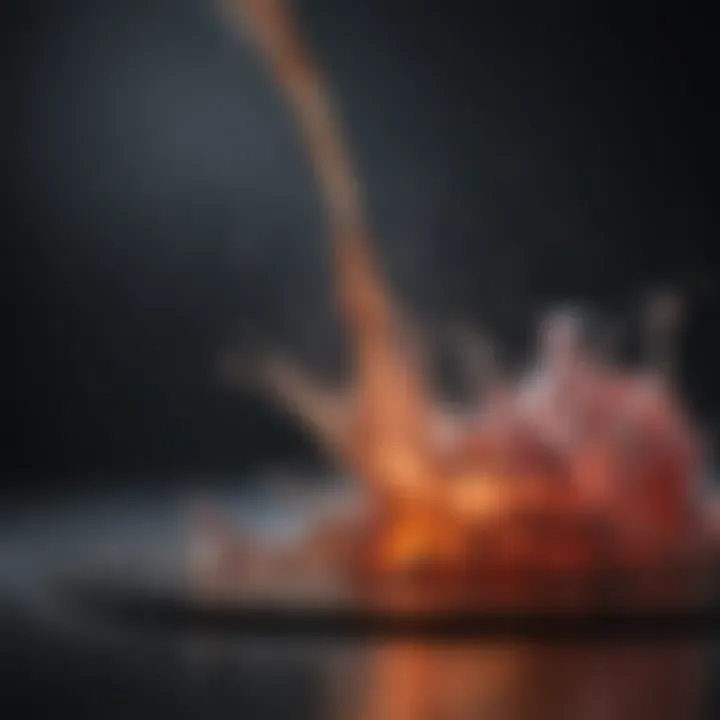
Poly(m-xylylene) presents a different set of characteristics compared to its p-counterpart. This type features a more flexible structure and offers superior adhesion properties. It is beneficial for applications requiring enhanced coatings on surfaces without compromising flexibility. Its unique feature is that it can be easier to apply on components needing more than just protection—such as improving wear resistance or creating a smoother surface finish. However, its performance in extreme environmental conditions may not match that of poly(p-xylylene).
Poly(chloro-xylylene)
Poly(chloro-xylylene) is another variant, recognized for its superior chemical resistance. This polymer is particularly advantageous in applications where harsh chemicals are present. Its composition allows it to resist solvents and corrosive agents more effectively than other types of parylene. A key characteristic of poly(chloro-xylylene) is its capability to maintain integrity under various chemical exposures. However, its processing requirements might be more stringent, making it less accessible for on-site applications.
"Understanding the chemical structure of parylene is fundamental to leveraging its properties in advanced applications across numerous sectors."
Deposition Methods
The deposition methods for parylene play a crucial role in determining the quality and efficacy of the final applications. These techniques dictate how well the material adheres to surfaces and the uniformity of its coating. Understanding these methods is essential for professionals and researchers looking to employ parylene across various industries. Each method has its own specific advantages and considerations, making it necessary to choose wisely based on the requirements at hand.
Chemical Vapor Deposition ()
Chemical Vapor Deposition, or CVD, is a widely used technique for applying parylene coatings. In this process, a gaseous mixture of the parylene monomer is introduced into a reaction chamber. The temperature and pressure are carefully controlled to cause the monomer to decompose and polymerize on the substrates being coated. This process results in a thin, uniform layer of parylene that conforms to the contours of the underlying materials.
The advantages of using CVD include:
- Uniform Coating: CVD achieves a highly uniform layer, which is especially important for complex geometries.
- Adhesion: The resulting coatings often have excellent adhesion properties, essential for longevity in various applications.
- Versatility: This method allows for the coating of a variety of materials, including metals, plastics, and ceramics.
However, careful handling is required to manage the by-products of the reaction and ensure proper ventilation to mitigate any potential safety risks.
Physical Vapor Deposition (PVD)
Physical Vapor Deposition, or PVD, is another technique utilized for applying parylene coatings. In PVD, the parylene material is vaporized in a vacuum environment and then condensed onto the substrate surface. This method may be less common than CVD for parylene but still serves important roles.
PVD has distinct benefits:
- Speed: The process can be faster than CVD for certain applications, allowing for quicker turnarounds.
- Control: PVD provides finer control over the thickness of the coating compared to CVD.
- Clean Process: PVD does not involve gaseous chemicals that may pose risks of exposure, potentially making it safer in certain contexts.
However, the ability to coat complex surfaces uniformly may be limited, especially when working with intricate designs.
Comparison of Techniques
Both CVD and PVD have their own strengths and weaknesses when it comes to parylene deposition.
- CVD is preferred when a uniform coating is essential on complex shapes. It excels in achieving thin films with excellent adhesion.
- PVD might be chosen for processes requiring speed and high throughput or when specific thickness control is more important.
When selecting between the two, it is crucial to consider:
- The geometry of the items being coated
- The desired properties of the parylene layer
- Safety and handling considerations related to each method.
Properties of Parylene
The properties of parylene are crucial for understanding its role in various applications. These unique characteristics dictate its performance and suitability for different environments. Parylene's mechanical properties, thermal stability, and chemical resistance are especially important, making it a preferred choice in fields such as electronics and biomedical engineering.
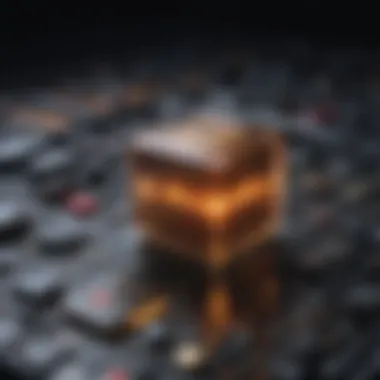
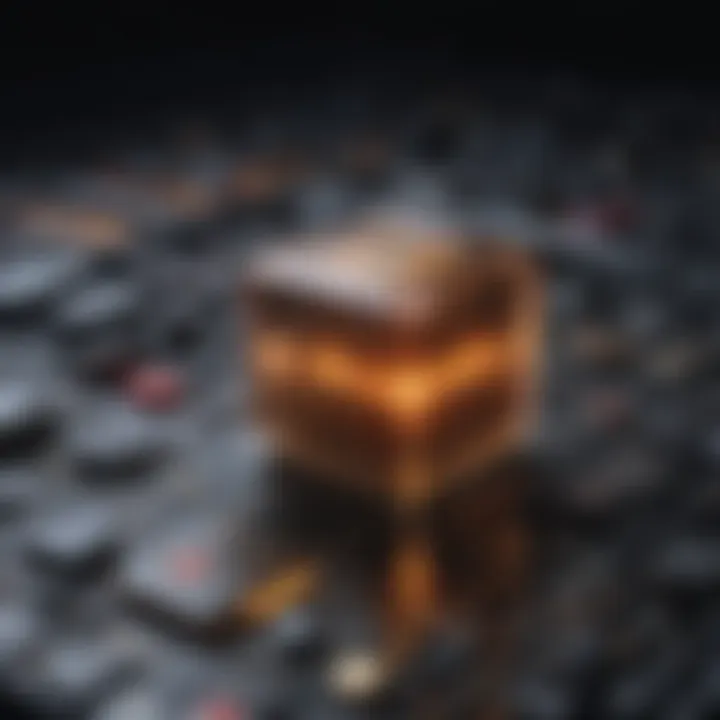
Mechanical Properties
Parylene exhibits notable mechanical strength. It demonstrates a balance of flexibility and rigidity, which is essential for many applications. The tensile strength of parylene is significant, allowing it to withstand considerable stress without deforming. Additionally, it has a low coefficient of friction, enhancing its utility as a protective coating. Such mechanical properties ensure that parylene can keep functionality under various load conditions, making it ideal for use in electronics where structural integrity is paramount.
It's worth noting that the mechanical characteristics of parylene can be affected by its thickness. Thicker coatings tend to display enhanced strength but might compromise adhesion to substrates. Understanding these nuances helps engineers make informed decisions when utilizing parylene in diverse projects.
Thermal Stability
One of the defining features of parylene is its thermal stability. It can maintain performance across a broad temperature range, from cryogenic levels up to 400 degrees Celsius. This exceptional thermal reliability is crucial in applications that involve significant temperature fluctuations, particularly in aerospace and electronic devices.
Importantly, parylene does not suffer from thermal degradation in the same way many polymers do. This quality allows devices coated with parylene to operate effectively in extreme conditions. Tests have shown that parylene coatings retain their functionality without evident signs of breakdown or alteration even after prolonged exposure to high temperatures.
Chemical Resistance
Parylene's resistance to various chemicals sets it apart as a preferred coating material. It is inert to many solvents, acids, and bases, making it suitable for applications in hostile chemical environments. For instance, in the biomedical field, parylene is used extensively for coatings on medical devices due to its ability to resist bodily fluids and sterilization processes.
This chemical resilience also extends to electrical insulation. Parylene does not allow moisture or corrosive agents to permeate, which is critical for electronics that require protection from environmental factors. Moreover, it adds an extra layer of security in maintaining the performance of sensitive equipment.
In summary, the properties of parylene make it an exceptional material for a variety of applications. Its mechanical strength, thermal stability, and chemical resistance are essential considerations in ensuring that it meets the demanding needs of modern science and industry. Understanding these properties is key for professionals seeking to leverage parylene effectively in their projects.
Applications of Parylene
Parylene plays a significant role across various industries due to its unique properties. This polymer is known for its effective insulation capabilities, moisture resistance, and biocompatibility. These aspects make it highly valuable in electronics, biomedical fields, and aerospace applications. Understanding the applications of parylene helps illustrate not only its versatility but also its necessity in modern technology and industry.
Electronics
Insulation
Insulation is a critical aspect in electronic devices. Parylene offers superior insulation properties, which are essential in protecting sensitive components from moisture and contaminants. This unique property is important as it enhances the reliability and lifespan of electronic devices. The ability of parylene to conform to complex geometries means it can coat intricate designs, making it popular in this field. However, its application may involve higher costs compared to other materials.
Encapsulation
Encapsulation is another crucial use of parylene in electronics. It serves to protect electronic circuits from environmental factors. This process provides a barrier against dust, chemicals, and humidity. The thinness of parylene films allows for minimal impact on the weight of devices, making it a preferred option. Nevertheless, the application must be carefully managed, as improper layers can lead to less effective protection.
Biomedical Uses
Coatings for Medical Devices
Parylene is widely utilized as a coating for medical devices due to its biocompatibility and inertness. These characteristics make it an ideal choice for implants and surgical instruments. This application ensures that devices do not react adversely with body tissues. Furthermore, parylene provides a protective layer that hinders bacteria growth, enhancing patient safety. However, the cost of coating can be a disadvantage for some manufacturers.
Drug Delivery Systems
In the field of drug delivery, parylene offers innovative solutions. Its thin films can control the release of medication, providing consistent dosages over time. This controlled release is vital for the effectiveness of many treatments. Furthermore, the biocompatibility of parylene ensures that medical applications do not induce negative responses in the body. Yet, designing effective drug delivery systems may require extensive research and development efforts.
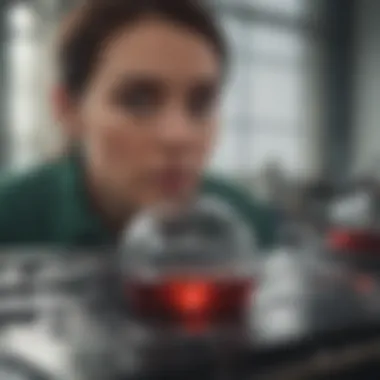
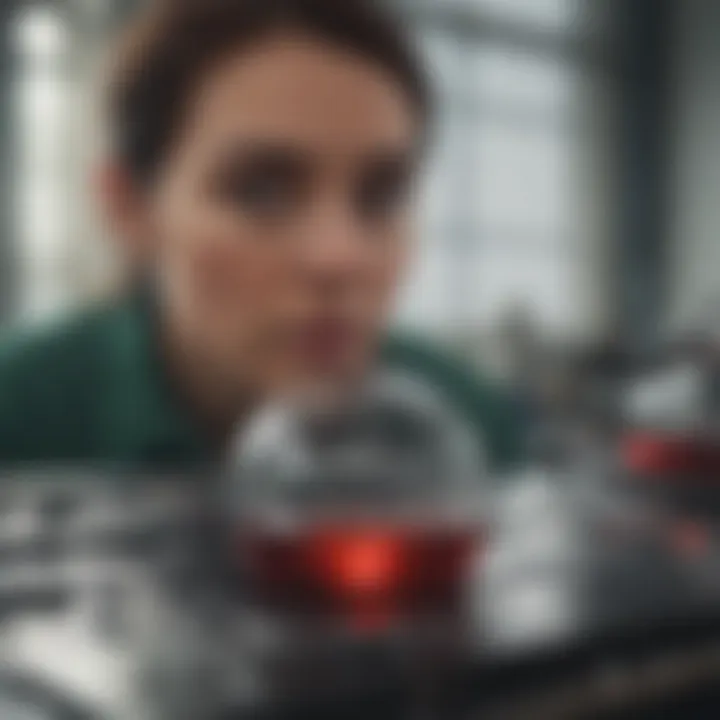
Aerospace Industry
The aerospace industry benefits significantly from the use of parylene. Its lightweight nature and excellent thermal stability make it suitable for various aerospace applications. Parylene can protect components from extreme conditions, providing a vital layer of safety and performance. Furthermore, its chemical resistance is crucial for parts exposed to fuels and other harsh substances. The challenge remains to balance its performance benefits with material costs for large-scale use.
Environmental and Safety Considerations
The evaluation of environmental and safety aspects related to parylene is critical, particularly given its wide usage in various industries. Understanding how to manage parylene's impact on the environment and ensuring the safety of those involved in its production and application is essential. These considerations support not just regulatory compliance but also sustainability initiatives that many companies now embrace.
Disposal and Recycling
Disposal and recycling of parylene-coated products present unique challenges. As a polymer, parylene does not easily decompose in natural environments. Disposal methods must be carefully weighed to minimize environmental harm. Options include:
- Incineration: While burning can effectively eliminate parylene, it must be conducted in controlled conditions to prevent the release of harmful byproducts.
- Landfill: Disposing of parylene in a landfill is a common practice, but this requires stringent regulations to ensure the polymer does not leach harmful substances into the soil or groundwater.
- Recycling: Currently, recycling facilities for parylene are limited, which creates a push for developing methods to reclaim this material effectively. Research is ongoing to explore possible recycling pathways, as the demand for sustainable materials increases.
Parylene's resistance to chemical breakdown adds another layer of complexity. This durability means products with parylene coatings should prioritize responsible disposal methods to protect natural ecosystems.
Toxicity and Regulations
The toxicity of parylene and the regulations surrounding its use are pivotal in understanding its safety profile. While parylene itself is generally regarded as non-toxic, the monomers involved in its synthesis can pose health risks.
Various regulations govern the handling and usage of parylene across different sectors:
- Material Safety Data Sheets (MSDS): Regulations outline safety protocols that workers must follow when dealing with parylene products and their precursors. MSDS documents provide essential information on potential hazards.
- OSHA Guidelines: The Occupational Safety and Health Administration has rules to safeguard workers against exposure to hazardous chemicals in their environment, including parylene precursors.
- Environmental Protection Agency (EPA): The EPA oversees compliance with environmental standards, specifically regarding emissions from parylene production processes.
An understanding of these frameworks fosters safer use and management of parylene in various applications.
The proper handling and understanding of safety regulations ensure not just compliance but also the health of workers and the environment.
Future Directions in Parylene Research
The field of parylene research is a continuously evolving domain that showcases its adaptability and versatility across various applications. As industries push towards more efficient and sustainable solutions, the future of parylene offers exciting possibilities. This is particularly relevant for both professionals and researchers who aim to leverage the polymer's unique properties for innovative purposes. Understanding these directions can aid in fostering developments that enhance functionality, sustainability, and applicability in diverse sectors.
Innovative Applications
One of the most remarkable aspects of parylene is its potential for innovative applications. Emerging technologies are creating a demand for advanced materials that can meet specific requirements in electronics, medicine, and environmental solutions.
For instance, in the electronics sector, parylene can play a crucial role in further miniaturization of devices such as smartphones and wearable technologies. Its insulating properties offer enhanced performance, which can directly contribute to the longevity of these devices while minimizing power consumption. Additionally, its biocompatibility opens avenues for new biomedical devices that could be less invasive and more effective.
In renewable energy, research is looking into the usage of parylene coatings on photovoltaic systems. Its protective qualities could help in extending the lifespan of solar panels, leading to more sustainable energy solutions.
Advancements in Deposition Techniques
Deposition techniques are central to how parylene is utilized in various applications. Ongoing research is focused on refining these techniques to improve coating uniformity and thickness control. The most common method—Chemical Vapor Deposition (CVD)—is being optimized to enhance efficiency and reduce costs. While CVD has been effective, the introduction of new materials and technologies could lead to breakthroughs that allow for alternative methods like Atomic Layer Deposition (ALD) or sol-gel processes to be applied more extensively.
These advancements could result in
- Increased precision in coatings, essential for electronics miniaturization.
- Higher throughput in production, driving down costs across industries.
- Broader compatibility with various substrates, hence expanding its market reach.
This evolution in deposition techniques is vital for maximizing the transparency and efficacy of parylene in applications where conventional methods might fall short.
The continual growth in understanding deposition methodologies can potentially unlock a new wave of advanced applications for parylene across various fields.