Separation Machines: Principles and Applications
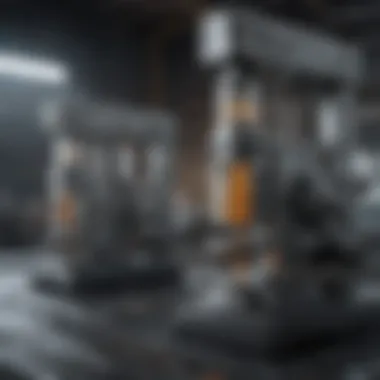
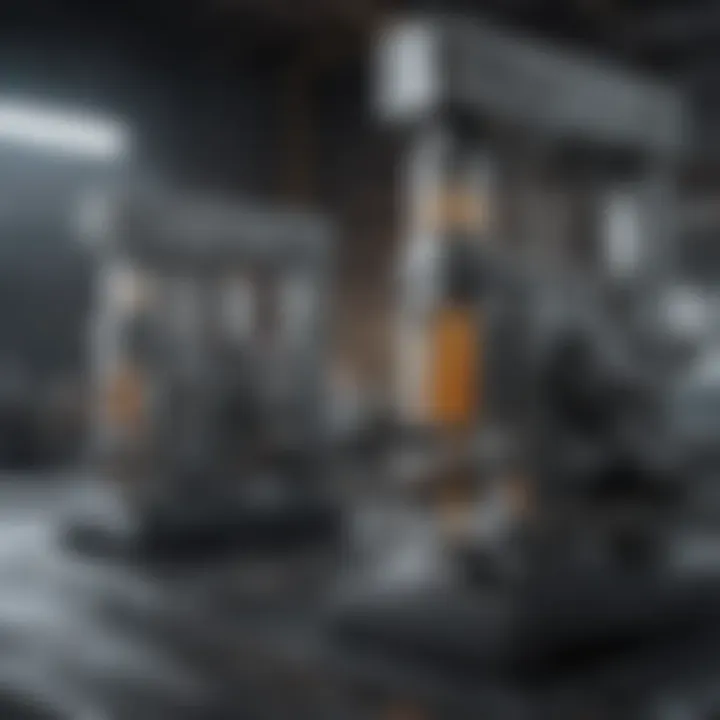
Intro
Separation machines play a pivotal role in various scientific fields, ranging from chemical engineering to environmental science. They are designed to isolate specific substances from mixtures, making them essential in processes such as purification, concentration, and analysis. Understanding the principles that govern these machines is crucial for optimizing their use in industry and research.
In this article, we will delve into the fundamental concepts of separation technology, including the different types of machines and their specific functions. We will also explore the advancements and applications that demonstrate the significance of these devices in solving real-world problems.
Whether it is in pharmaceuticals, food processing, or environmental remediation, the applications are diverse and impactful. As we explore these themes, readers will gain insights into the operational mechanisms, benefits, and emerging trends in separation technologies.
Prologue to Separation Machines
Separation machines play a vital role in both scientific and industrial applications. They are essential tools that help in isolating components from mixtures, enhancing the purity and functionality of materials in various processes. Understanding the principles and workings of these machines will empower researchers and professionals across multiple disciplines to optimize their operations and innovate effectively.
Definition and Overview
Separation machines refer to a category of equipment designed to separate mixtures into their constituent parts. The term encompasses a wide range of technologies, including mechanical, thermal, and chemical methods. Each type of machine operates on specific principles, utilizing physical or chemical forces to achieve separation. These machines can be found in laboratories, factories, and processing plants, addressing diverse needs in sectors such as chemical engineering, biotechnology, and food processing.
Importance in Various Industries
The significance of separation machines transcends mere functionality; they are pivotal in driving efficiency and sustainability in many industries. Here are some key areas where their impact is notable:
- Chemical Engineering: In this field, separation machines such as distillation columns and centrifuges are used to purify chemicals or recover valuable products from by-products, boosting economic viability.
- Biotechnology: Techniques like filtration and centrifugation are essential in purifying biological compounds, which is essential for drug development and production.
- Food Processing: Separation machines ensure food safety by removing contaminants, improving the quality and shelf life of food products.
- Water Treatment: Machines like membrane filters clean water supply, playing a crucial role in public health and environmental protection.
It is evident that separation machines contribute not only to productivity but also to environmental sustainability by enabling more efficient resource use and waste reduction.
Understanding the operational principles of separation machines is crucial for maximizing their potential in various applications.
Principles of Separation
The principles of separation are vital in understanding how separation machines function. They lay the groundwork for designing processes that can effectively isolate components in various mixtures. This section explores the foundational concepts that underlie these technologies, emphasizing their significance across different applications in industries like chemical engineering, biotechnology, and food processing.
Basic Concepts
Separation processes fundamentally aim to alter the composition of a mixture. Different methods are employed based on the properties of the components involved. Four basic principles guide these operations:
- Differences in Phase: Many separation techniques leverage the distinct physical states of materials, such as solid, liquid, or gas. For instance, filtration utilizes solid-liquid phase differences to collect solids from liquids.
- Chemical Affinity: The interactions between molecules can be utilized to separate substances. A specific example can be seen in adsorption, where materials bond with molecules in a mixture based on their chemical properties.
- Size and Shape: Separators often exploit differences in size and shape to achieve separation. This is readily apparent in screening processes, where sieve size allows smaller particles to pass through while retaining larger ones.
- Density: Different materials have varying densities, which can be pivotal in separation processes like centrifugation. Here, centrifugal force is used to accelerate the settling of heavier particles in a mixture, ensuring effective separation from lighter components.
These basic concepts form the building blocks for more complex separation technologies that enhance efficiency and effectiveness.
Thermodynamic Considerations
Thermodynamic principles underscore many separation processes. Understanding these considerations is crucial for optimizing operations and ensuring energy efficiency. Key aspects include:
- Equilibrium: Many separation processes rely on reaching a state of equilibrium. For example, distillation separates components based on their boiling points. The process continues until the vapor and liquid phases are balanced, thus achieving effective component separation.
- Energy Requirement: Different methods have varying energy demands. For instance, thermal operations, such as evaporation, usually require significant energy inputs, which must be factored into cost analyses.
- Phase Changes: Separation often involves phase transitions. Recognizing how temperature and pressure influence these changes can improve process design. Crystallization, for example, can be manipulated by adjusting temperature to control how and when solids form from a solution.
- Entropy: Understanding entropy helps in evaluating how systems evolve and the feasibility of different separation methods. High entropic changes may indicate a less favorable process outcome, necessitating reevaluation of the separation strategy.
In summary, mastering the principles of separation provides essential insights into the effectiveness and economic viability of various technologies. This understanding is crucial for researchers and professionals tasked with streamlining processes across numerous sectors.
Types of Separation Machines
Separation machines play a critical role in many sectors by providing methods to isolate and purify substances. Understanding the types of separation machines is essential to grasp their functionality and applicability across various industries. This section delves into the three main types: Mechanical, Thermal, and Chemical Separators. Each type introduces unique technologies, highlights specific characteristics, and addresses benefits and challenges within the context of separation processes.
Mechanical Separators
Mechanical separators utilize physical methods for the separation of materials. These processes rely on the properties of materials, such as size, shape, and mass. Below, we explore significant mechanical separation techniques including screening, filtration, and centrifugation.
Screening
Screening is a fundamental mechanical separation technique that involves the use of screens to separate particles based on size. Its main contribution is to effectively classify materials into different size ranges, enabling further processing of finer or coarser materials. The key characteristic of screening lies in its adaptability to various industries, including construction and food processing.
A unique feature of screening is its ability to handle large volumes of material with relatively low energy consumption. The advantages of this method include its efficiency and simplicity in operation. However, disadvantages may arise when dealing with particles of similar sizes, resulting in less effective separations.
Filtration
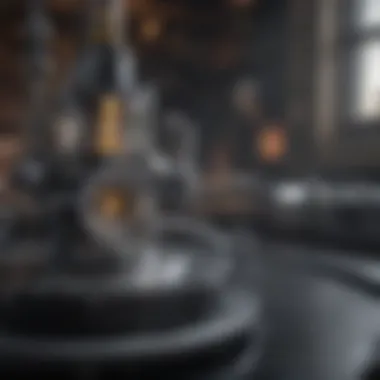
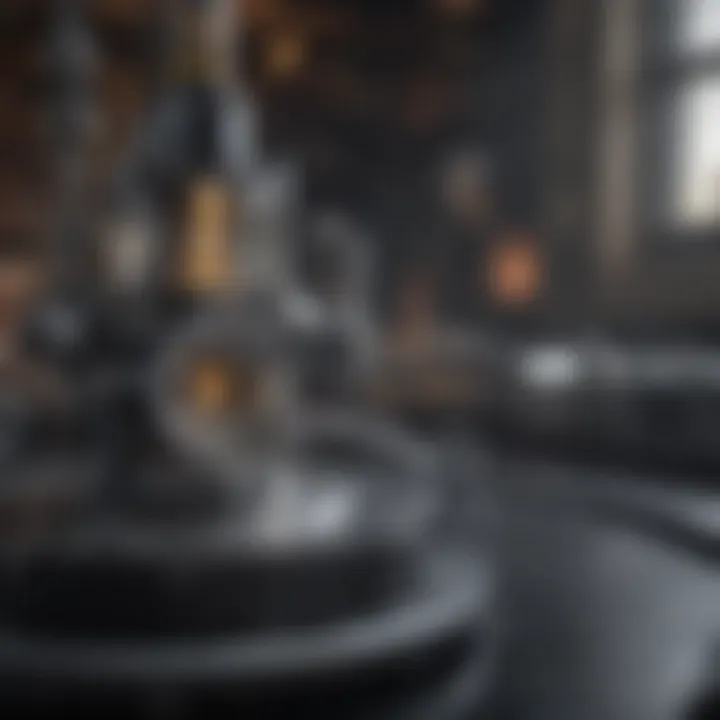
Filtration is another prevalent mechanical separation method focused on separating solids from liquids or gases. The process uses a porous material, allowing liquids or gases to pass while trapping solid particulates. Its contribution is vital in sectors like pharmaceuticals, water treatment, and food production.
The main characteristic of filtration is its capability to achieve different purity levels, which is essential for many processes. A major advantage is its effectiveness in retaining solids, while a key disadvantage is the potential for filter clogging, which may reduce efficiency over time.
Centrifugation
Centrifugation utilizes the force of rotation to separate components based on density differences. This method is widely used in laboratories and industries for applications such as blood separation, wastewater treatment, and the production of dairy products.
Centrifugation's key characteristic is its capacity to achieve rapid and efficient separations. This technology allows for the processing of small sample sizes with high precision. Nevertheless, the disadvantages include the need for skilled operation and maintenance of equipment, which may add to operational costs.
Thermal Separators
Thermal separators function by using temperature changes to facilitate the separation of substances. This process is fundamental in areas such as chemical engineering and environmental management. Notable thermal separation methods include distillation, evaporation, and crystallization.
Distillation
Distillation is a process primarily used to separate mixtures based on differences in boiling points. This technique is highly relevant in the petrochemical industry for separating crude oil into various refined products. The key characteristic is the ability to achieve high purity levels through controlled heating and cooling cycles.
A unique feature of distillation is its scalability, making it suitable for both small and large operations. However, the process is energy-intensive, which can result in higher operational costs.
Evaporation
Evaporation is a simpler thermal separation process that involves heating a liquid to leave behind solids or to change the liquid into vapor. This technique is especially useful in food processing, for example, in the concentration of juices. The key characteristic is its effectiveness in removing solvent at low temperatures.
A significant advantage of evaporation is its low energy requirement compared to other thermal methods. However, it may not provide a complete separation, leaving some soluble components behind.
Crystallization
Crystallization aims to separate a solid from a solution, forming pure crystals. This method is crucial in producing high-quality chemical compounds and pharmaceuticals. The main characteristic of crystallization is its ability to yield highly pure compounds.
The unique feature of this method is its capability to remove impurities efficiently. Nonetheless, crystallization can be slow and may require extensive equipment to ensure optimal conditions for crystal formation.
Chemical Separators
Chemical separators utilize chemical processes to achieve separations based on chemical properties rather than physical ones. This section covers three primary techniques: absorption, adsorption, and membrane technology.
Absorption
Absorption is a process in which a substance becomes integrated into another material, often through a liquid or solid medium. This method is prominent in various applications, including gas purification and waste treatment. The key characteristic of absorption is its non-reversible nature, allowing for complete integration of contaminants.
A unique trait of absorption is its ability to target specific substances for extraction. The disadvantage could be the slow kinetics involved in the process, which may limit its effectiveness under certain conditions.
Adsorption
Adsorption involves the accumulation of molecules on the surface of solid materials. This method is widely applied in areas such as environmental science and industrial applications for pollutant removal. Its key characteristic is selectivity, which helps in effectively targeting specific contaminants.
A significant advantage of adsorption is its versatility across various contexts. However, it may suffer from limitations related to capacity and potential saturation of the adsorbent material over time.
Membrane Technology
Membrane technology uses semi-permeable membranes to separate substances based on size or specific chemical properties. This method is prime in water treatment, food processing, and chemical manufacturing. The main characteristic is its high efficiency, often requiring lower energy than traditional methods.
A unique feature of membrane technology is its low environmental impact, making it a popular choice in processes requiring sustainability. The disadvantage might include membrane fouling, which can necessitate regular maintenance to ensure optimal performance.
Understanding these types of separation machines allows industry professionals to make informed choices about the appropriate technologies and methods for specific applications. Each technique presents unique characteristics and challenges, contributing to its effectiveness in different scenarios.
Applications of Separation Machines
Separation machines play a vital role across several industries. Their applications are diverse, each tailored to meet specific requirements of the field. Understanding these applications provides insights into their practical significance, benefits, and the considerations involved in their implementation. The use of separation technologies enhances efficiency, precision, and sustainability in processes that demand strict quality controls.
In Chemical Engineering
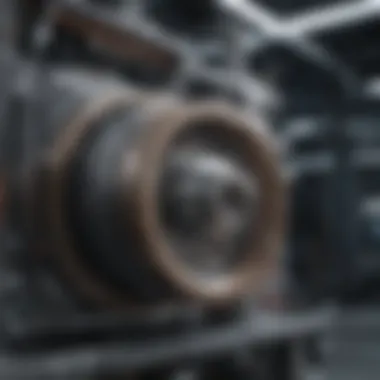
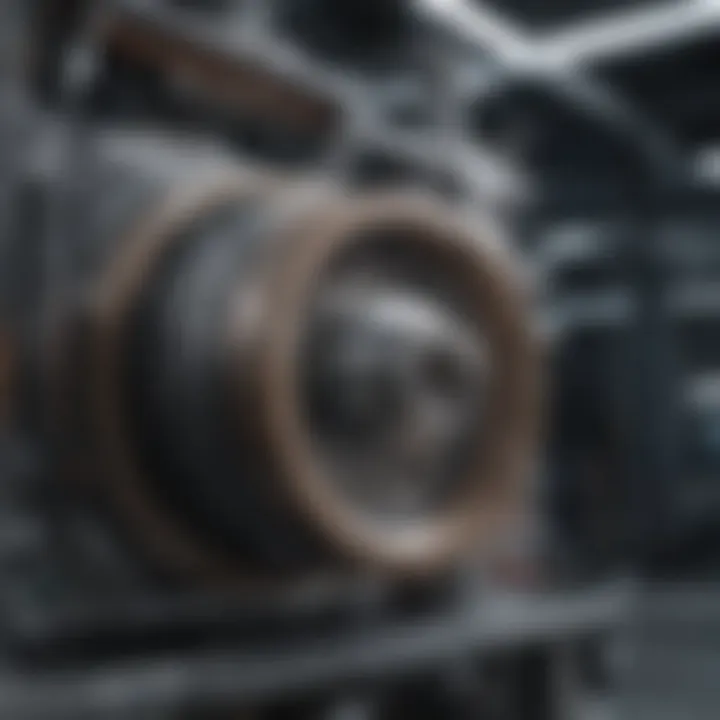
Chemical engineering relies heavily on separation processes for purifying compounds and materials. Techniques such as distillation, crystallization, and extraction are fundamental in this arena. Distillation, for instance, is critical for separating liquid mixtures based on differing boiling points. It enables the production of high-purity solvents which are essential for various chemical reactions.
Moreover, separation machines mitigate waste generation. By refining feed stock effectively, industries can reduce the quantity of byproducts which ultimately lowers treatment costs and environmental impacts. Innovations in separation technology, such as advanced membrane processes, also enhance operational efficiencies while ensuring compliance with increasingly stringent regulations.
In Biotechnology
In biotechnology, separation machines are crucial for isolating biological products. Processes like centrifugation and filtration are commonplace. These methods facilitate the extraction of proteins, enzymes, and other vital substances from biological materials, thus crucial for drug development and vaccine production.
Moreover, continuous advancements in separation technologies not only improve yield but also enhance safety and reduce costs. The integration of automation into separation processes also allows for precise control and reproducibility which boosts the reliability of biotechnological applications.
In Water Treatment
Water treatment processes heavily depend on separation technologies to ensure safe drinking water. Techniques such as sedimentation and filtration remove suspended solids and pathogens effectively. Additionally, advanced separation methods like reverse osmosis are integral to producing desalinated water, which is increasingly important in arid regions.
Understanding the varying separation needs for water treatment helps to implement more eco-friendly systems. These systems minimize energy use and chemical interactions. Consequently, they deliver sustainable solutions that address both environmental concerns and public health needs.
In Food Processing
The food processing industry utilizes separation machines to enhance product quality and safety. Technologies such as filtration and centrifugal separation are frequently used. For instance, these machines are employed to clarify juices and oils, removing unwanted solids while preserving flavor and nutrients.
Moreover, separation machines improve the overall efficiency of production lines. With higher purity levels in end products, consumer satisfaction increases. It is imperative for manufacturers to adopt advanced separation technologies that align with food safety standards and consumer preferences.
Separation machines are essential tools for increasing efficiency and quality across industries, influencing both production costs and environmental impact.
The applications of separation machines are integral to innovation and sustainability in various fields. Emphasizing their importance enhances our understanding of industrial processes, ultimately leading to improved practices and outcomes.
Technological Advancements in Separation Machines
Technological advancements in separation machines play a pivotal role in enhancing efficiency, productivity, and sustainability in various industries. These innovations not only improve the designs and functionalities of existing equipment but also open up new possibilities for the separation processes. As separation technologies evolve, they become more integrated with digitalization and automation, enabling smarter operations and reduced resource consumption.
Innovations in Equipment Design
Recent innovations in equipment design are focused on improving the overall performance of separation machines. The goal is to achieve higher efficiency while minimizing energy and material input. For instance, new materials are being used to create lightweight and stronger components. These materials can withstand harsh environments, thus extending the lifespan of the equipment.
Design optimization is also crucial. Computational fluid dynamics (CFD) software allows engineers to model the flow characteristics of materials being processed. This assists in refining the machine design to minimize turbulence and maximize separation efficiency.
Another notable advancement is the development of modular designs. These systems can be easily adapted to different processes, leading to increased flexibility in production.
Automation and Control Systems
Automation and control systems have significantly enhanced the operation of separation machines. These technologies make processes more precise and less prone to human error. Advanced sensors and monitoring devices collect real-time data, allowing operators to adjust parameters instantly for optimal performance.
The implementation of machine learning algorithms can analyze operational data, leading to better predictive maintenance. This means less downtime and lower maintenance costs, as issues can be addressed before they lead to failures.
Furthermore, automation contributes to safety. Reducing manual interventions decreases the risks associated with handling hazardous materials.
Nanotechnology in Separation Processes
Nanotechnology is emerging as a game changer in separation processes. The manipulation of materials at the nano scale opens the door to innovations that were previously impossible. For example, membranes with nanosized pores can separate particles at a much finer resolution than traditional methods. This has significant implications in industries like water treatment and biotechnology, where purity is paramount.
Nanotechnology also allows for the development of adsorbents that have a higher surface area, leading to more efficient adsorption processes. These materials can not only improve separation efficiency but also lower energy requirements.
"The intersection of nanotechnology and separation processes is reshaping the landscape of various industries, promoting sustainability and efficiency."
Challenges in Separation Technologies
The domain of separation technologies presents numerous challenges that significantly impact the efficiency and effectiveness of processes across various industries. Understanding these challenges is crucial for professionals involved in the design, implementation, and optimization of separation machines. Each challenge invites a deeper examination of economic viability, environmental considerations, and technological advancements. Addressing these challenges leads to improved practices and a better alignment with industry objectives.
Cost Efficiency and Economic Feasibility
Cost efficiency remains a core concern when employing separation technologies. The initial investment for advanced separation machines can be substantial, often creating a barrier for smaller operations or startups. Understanding the cost-benefit analysis of these technologies helps in measuring their long-term economic feasibility.
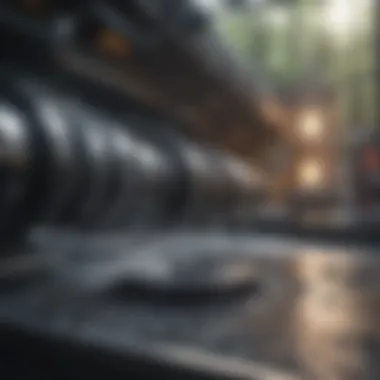
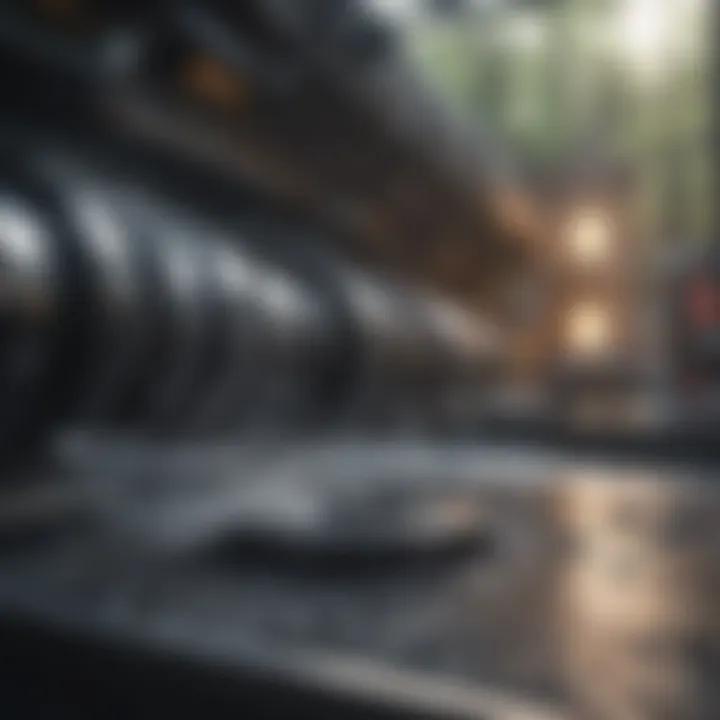
- Operational Costs:
- Return on Investment: A detailed analysis of productivity improvements against initial costs is vital. Companies must weigh the expected benefits against the expenses incurred, ensuring that the implementation of separation technologies is financially viable.
- Competitive Advantages: Investing in cost-efficient technologies can create a distinct market advantage, positioning businesses better in a competitive landscape. Effective separation processes can improve product quality and yield, leading to higher market acceptance.
- Maintenance and energy consumption significantly contribute to ongoing expenses. Efficient systems minimize these costs, providing greater economic returns.
- Human resources and training also play a role in operational budgets, needing careful consideration.
Environmental Impact and Regulations
The environmental implications of separation technologies increasingly guide industry practices. Stricter regulations and a growing awareness of sustainability compel companies to adopt eco-friendly practices.
- Waste Management:
- Energy Consumption:
- Regulatory Compliance:
- Many separation processes produce waste or by-products that require management. Utilizing separation technologies effectively can minimize waste generation and encourage recycling efforts.
- High energy requirements can lead to a larger carbon footprint. Methods that lower energy use not only mitigate environmental impact but can also ease compliance with regulations.
- Companies must remain cognizant of local and international regulations governing emissions and waste. Meeting these regulations is critical for avoiding fines and enhancing corporate responsibility.
The integration of sustainable practices in separation technologies is no longer optional; it is a necessity driven by regulatory compliance and market pressures.
Faced with these challenges, it is vital for companies to engage in continuous research and development. This ongoing effort ensures that they remain competitive while minimizing both economic and environmental costs.
Future Trends in Separation Technologies
The landscape of separation technologies is continuously evolving, driven by advancements in science and technology. Future trends in this area are essential for improving efficiency, reducing costs, and minimizing environmental impact. Exploring these trends allows professionals and researchers to stay ahead and implement solutions that meet the challenges of modern industry requirements.
Sustainability and Green Chemistry
Sustainability is not just a trend; it is a necessity. The integration of sustainable practices into separation technologies aims to minimize waste and reduce energy consumption. Green chemistry principles are guiding innovations in this field. These principles promote the development of separation processes that are environmentally friendly. For example, methods such as supercritical fluid extraction employ less hazardous solvents which align with sustainability goals.
Using efficient separation methods also aids in resource recovery from waste products. This can lead to increased energy efficiency and reduced costs. By adopting green practices, industries can enhance their public image and comply with stricter regulations regarding environmental protection.
The focus on sustainability fosters research into novel materials and processes that demonstrate higher effectiveness while using fewer resources.
Integration of AI and Machine Learning
The future of separation technologies will heavily rely on artificial intelligence and machine learning. These technologies offer transformative potential in optimizing separation processes. Algorithms can analyze extensive data sets to identify patterns, improving decision-making in real-time.
Machine learning can enhance various aspects, including:
- Process efficiency: Automating adjustments based on operational data can maximize productivity.
- Predictive maintenance: Analyzing equipment performance can prevent failures before they occur.
- Customization: Tailoring separation processes to specific materials or conditions can yield better results.
By integrating AI, industries can achieve greater precision and flexibility. This paves the way for smart factories where separation machines communicate and adapt to changes autonomously.
Culmination
The conclusion section of this article wraps up the key insights about separation machines, emphasizing their critical role in modern technology. The significance of separation machines cannot be overstated, as they serve as essential tools in various industries, including chemical engineering, biotechnology, water treatment, and food processing. These machines enable efficient and precise separation of materials, ultimately enhancing productivity and product quality.
In summary, the main points discussed throughout this article highlight:
- The fundamental principles of separation, such as thermodynamic considerations and basic concepts that underpin their functionality.
- The diverse types of separation machines—from mechanical to thermal and chemical—that cater to specific application needs.
- Technological advancements influencing separation processes, including innovations in equipment design and the integration of automation and control systems.
- The challenges faced within this sector, such as economic feasibility and environmental impact, which demand careful consideration.
- Future trends that suggest a leaning towards sustainability and the incorporation of artificial intelligence to optimize processes.
"Separation machines not only improve efficiency but also play a crucial role in addressing environmental concerns."
Summary of Key Points
In concluding this exploration, it is important to reiterate the primary takeaways:
- Adoption of Technologies: Various technologies, including centrifugation and distillation, facilitate effective separation processes.
- Importance of R&D: Ongoing research and development will drive improvements in separation efficiency and cost-effectiveness.
- Focus on Sustainability: Trends indicate a shift towards sustainable practices, emphasizing the need for environmentally friendly separation methods.
Each of these points contributes to a deeper understanding of how separation machines are integral to not just industrial processes, but also to addressing broader challenges such as environmental sustainability.
Implications for Further Research
The insights gained from this article open several avenues for future research in separation technologies. Potential areas of focus include:
- Enhancing Efficiency: With demands for higher efficiency, research can aim to optimize existing separation methods or create new technologies.
- Low-Impact Solutions: Investigating alternative separation processes that have minimal environmental impact remains a pressing need.
- Integration of AI: Future research could focus on leveraging artificial intelligence to enhance machine learning applications in separation processes, thereby improving decision-making and operational efficiency.
As these technologies continue to evolve, the interplay between engineering, chemistry, and data sciences will likely yield innovative and sustainable solutions that address both current and future challenges in separation processes. Each of these strands presents opportunities for academic inquiry and practical application, thereby pushing the boundaries of what is possible in the field.