Sintering Steel: Process and Applications Explained
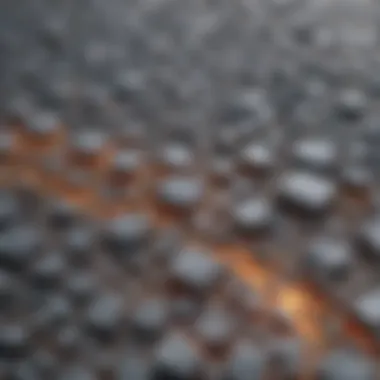
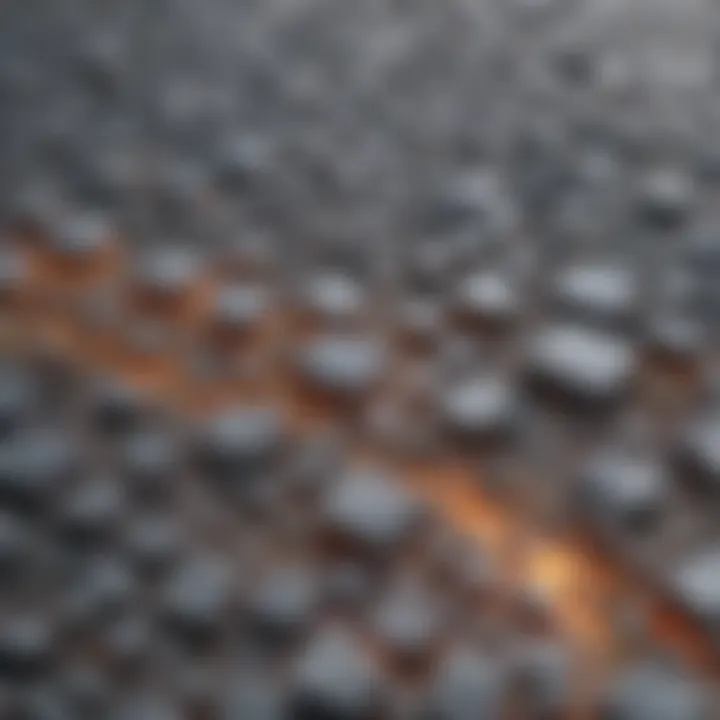
Intro
Sintering steel is an essential process in metalworking and powder metallurgy. It serves as a cornerstone in producing components that demand high strength and precision. Understanding the intricacies of sintering allows professionals and researchers in various fields to optimize production processes and enhance material performance. This article clarifies the key aspects of sintering, from its fundamental principles to its applications in industry, helping readers navigate through its complexities.
Research Highlights
Overview of Key Findings
Sintering involves heating powdered steel below its melting point, enabling atomic diffusion and solidification. The process can be influenced by several factors, including temperature, pressure, and the presence of additives. This article identifies several significant findings:
- Techniques: Different sintering techniques, such as liquid phase sintering and microwave sintering, each have distinct advantages depending on the application.
- Additives and Binders: The inclusion of specific additives can enhance mechanical properties and facilitate the sintering process. For example, boron and silicon are often employed to improve strength.
- Mechanical Properties: Sintered steel exhibits unique mechanical properties, such as improved hardness and wear resistance, which are pivotal in applications ranging from automotive parts to aerospace components.
Significance of the Research
The research contributes substantial insights into the evolution of sintering technology. By exploring advancements and sustainability efforts, it highlights the importance of sintering in contemporary material sciences. This knowledge not only aids engineers in choosing the right methods for production but also encourages innovations that could lead to more efficient manufacturing processes.
Applications of Sintering in Industry
Sintering has a vast range of applications across multiple industries. Here are some contexts where it plays a critical role:
- Automotive: Sintered components are widely utilized in engine parts, transmission gears, and bearings due to their strength and durability.
- Aerospace: High-performance components in aircraft and spacecraft rely on the capability of sintered steel to withstand extreme temperatures and pressures.
- Medical Devices: The biocompatibility of certain sintered materials makes them suitable for producing implants and surgical tools.
Epilogue and Future Trends
As industries push towards more innovative and sustainable practices, sintering technology continues to adapt. Future research will focus on improving energy efficiency in sintering processes, developing greener materials, and integrating digital technologies for better precision and control. As such, this article serves as a reference point for students, researchers, and professionals aiming to understand the current landscape and future directions of sintering steel.
Preface to Sintering Steel
In the realm of material science, sintering steel stands out as a pivotal process in transforming metal powders into solid structures. This section aims to elucidate the significance of sintering within the frameworks of manufacturing and engineering. Understanding sintering is crucial for those engaged in industries that rely on advanced material properties and production efficiencies.
The process involves heating steel powders up to a specific temperature, allowing particles to bond, thereby creating a dense material with desirable characteristics. This method is not just a means to produce components but also a pathway that opens avenues for innovation in design and sustainability. The nuances of the sintering process enable the production of parts with complex geometries, which may be challenging to achieve through traditional means like casting or machining.
Definition and Overview
Sintering is a thermal process used to convert powdered materials into a solid mass. The primary principle involves the application of heat without melting the base material, which in this context is steel. During sintering, atoms on the powder's surface migrate and bond, leading to enhanced mechanical properties.
Different stages define the sintering process, each with its own significance. These stages involve heating the material to a point where the particles adhere but do not melt, followed by cooling. The resulting material exhibits a uniform microstructure, which is essential for ensuring consistent mechanical performance across various applications.
Historical Context
The origins of sintering can be traced back to ancient times, with evidence suggesting that the process was utilized in the form of ceramics and metalworking long before modern techniques were developed. Historically, sintering was primarily done manually in small batches, limiting its application and scope. However, with advancements in technology, such as the introduction of controlled atmosphere sintering and improved heating methods, the process has evolved significantly.
In the early 20th century, sintering steel began gaining traction as the demand for higher precision and strength in components increased. Companies recognized that sintering could enhance efficiencies in production, leading to its incorporation in various industrial practices. Today, sintering has become integral to various sectors, including automotive, aerospace, and medical industries, reflecting its adaptability and importance in modern manufacturing.
The Sintering Process Explained
The sintering process is essential in the production of sintered steel and is a focal point of this article. Understanding sintering allows for greater insights into how complex steel components are manufactured. It involves heating metal powders to a point where they bond together without melting completely. This process not only makes it possible to create components with intricate designs but also improves material properties like strength and performance. The benefits of sintering include efficiency in production and the ability to utilize materials that might be difficult to process through traditional means.
Fundamental Mechanisms
The fundamental mechanisms of sintering involve several physical and chemical phenomena that occur as powders are heated. The key mechanism at play is atomic diffusion, where atoms move from regions of high concentration to regions of low concentration. This leads to the densification of the powder mass, and thus, improved mechanical integrity of the final product. The process is influenced by factors such as temperature, time, and the presence of additives, which enhance bonding.
Sintering Stages
The sintering process can be divided into distinct stages, each contributing to the final characteristics of the steel product. Understanding these stages is crucial for optimizing the processes and ensuring desired end results.
Heating Phase
The heating phase is where consolidation begins as the steel powders start to reach elevated temperatures. During this phase, the critical characteristic is the temperature rise, which should be controlled meticulously. This phase is especially beneficial as it prepares the powders for contact formation. However, if the temperature is not precisely managed, it can lead to undesired grain growth, which may weaken the structural integrity of the final product.
Contact Formation
During contact formation, powder particles begin to touch each other. The key feature in this phase is the establishment of bonds across particle edges. This leads to initial strengths in the structure, which are crucial for further densification. A beneficial aspect is that strong contact points enhance material cohesion, allowing for better performance in the final application. However, over-pressuring can lead to an uneven distribution of stresses.
Sintering Phase
The sintering phase is where most of the densification occurs. Here, the key characteristic is the ongoing atomic diffusion that leads to neck growth between adjacent particles. This is essential because it increases the density of the material. The unique feature of this phase is that it solidifies the relationships built in previous stages, contributing greatly to the material's toughness. Yet, there exists a potential risk if the phase lasts too long, leading to excessive coarsening of the microstructure, which could compromise hardness.
Cooling Phase
Finally, the cooling phase is critical as it stabilizes the final structure. The key characteristic of this phase is controlling the cooling rate, which affects the microstructural properties of the sintered steel. A slow cooling rate is often preferred to minimize thermal stresses, which can lead to cracking or other defects. Its unique feature is that proper cooling enhances properties like strength and hardness while avoiding the risk of warping. A drawback can be the time involved in this phase, which may affect overall production efficiency.
Sintering steel is a dynamic process where each stage serves a purpose in achieving the desired material attributes. Effective control over these stages leads to superior end products.
Materials Used in Sintering Steel
The choice of materials in the sintering process plays a critical role in determining the quality and performance of the final product. Understanding the components that contribute to sintering is essential for optimizing outcomes in various applications. As sintering steel involves the transformation of metal powders into a solid mass, both the powders and any additional constituents like additives and binders must be carefully considered. This section explains two key components in the sintering process: steel powders, and additives and binders.
Steel Powders
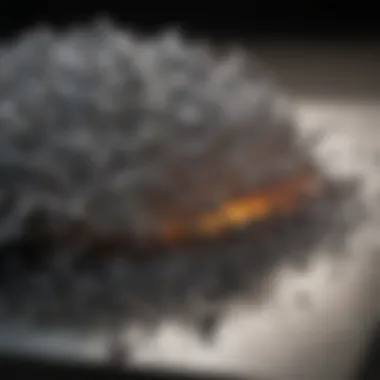
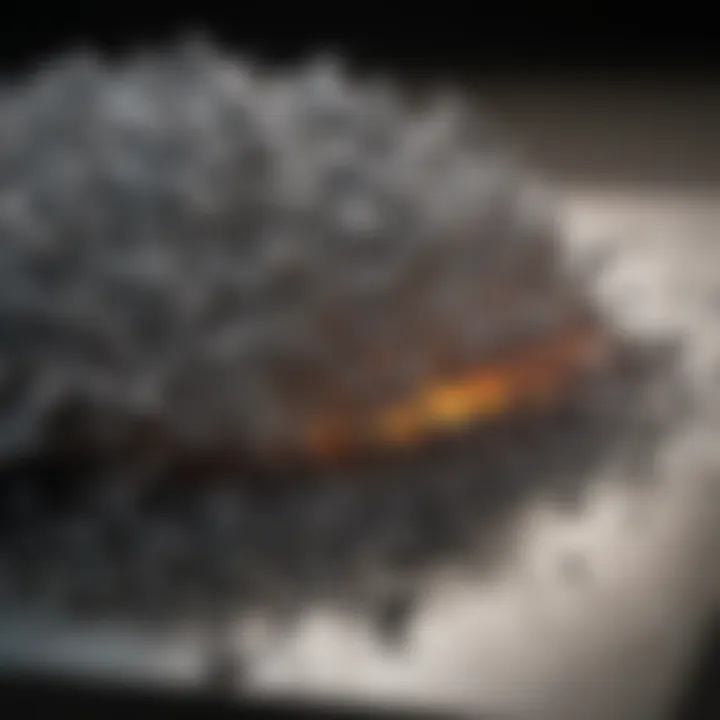
Steel powders are the foundational material used in the sintering process. The specific properties of these powders determine how well they will perform during sintering. Factors such as particle size, shape, and purity significantly impact the densification of the final product.
- Particle Size: The size of the powder particles affects the sintering behavior. Smaller particles tend to have a larger surface area, which can enhance the sintering rate. However, excessive fineness may lead to increased agglomeration.
- Particle Shape: Irregularly shaped powders can provide better packing density compared to spherical powders. Yet, this can also lead to inconsistencies in flow and handling during processing.
- Purity: The presence of impurities in steel powders can compromise the mechanical properties of the sintered part. High purity is often necessary for demanding applications, such as aerospace and medical devices.
Overall, choosing the right steel powders is vital. The interaction between these properties dictates not only the quality but also the efficiency of the sintering process itself.
Additives and Binders
Additives and binders are introduced to improve the performance of the sintered material. These components serve various functions, including enhancing flowability during powder handling and altering the mechanical properties of the sintered product.
- Additives: These may include materials like graphite, which is used to improve lubricity during die compaction. Other additives can modify magnetic or corrosion-resistant properties, tailoring the final product to specific needs.
- Binders: Different types of binders are used to facilitate the binding of powder particles prior to sintering. Some binders are removable after processing, while others are designed to burn out, leaving no residue. The selection of appropriate binders affects not only the density but also the porosity of the final sintered object.
Adding these materials presents both advantages and challenges, as improper use may lead to defects or undesired properties in the final product. Therefore, careful assessment of additives and binders is necessary for successful sintering.
"Understanding the composition of materials used in sintering is essential for achieving desired performance in the final product."
Types of Sintering Techniques
Sintering techniques are fundamental in shaping the way steel is processed and ultimately, the characteristics of the final product. This section presents the various sintering methods, highlighting their significance, benefits, and different considerations involved in their implementation.
Conventional Sintering
Conventional sintering is the most widely used method in the sintering of steel. This technique involves heating mixed powder materials to a temperature below their melting point. The heating allows the particles to bond through atomic diffusion, creating a compact solid structure. This method is cost-effective and offers reliable reproducibility in producing various steel products.
The key aspects of conventional sintering include:
- Temperature control: Optimal temperature ensures proper diffusion and bonding of the particles without causing deformation.
- Atmospheric conditions: Sintering is typically carried out in controlled atmospheres to prevent oxidation and contamination of the steel powders.
- Time management: The duration of the sintering process significantly influences the material properties and must be carefully monitored.
Despite its advantages, conventional sintering is limited in producing intricate geometries and high-density components, which can be a drawback for advanced applications.
Hot Isostatic Pressing
Hot Isostatic Pressing (HIP) is an advanced sintering technique that enhances the density and mechanical properties of the material. This method combines high temperature and isostatic pressure, which allows for greater consolidation of the powder materials. The process results in fewer defects and higher strength in the final sintered products.
Benefits of Hot Isostatic Pressing include:
- Uniform density: The application of pressure during the sintering process leads to a more uniform distribution of density throughout the material.
- Improved material properties: Compared to conventional sintering, HIP can produce materials with higher tensile strength and ductility.
HIP is particularly beneficial for industries that require high-performance components, such as aerospace and biomedical sectors.
Spark Plasma Sintering
Spark Plasma Sintering (SPS) is an innovative method that utilizes pulsed electric current to achieve rapid heating and densification of the powder materials. This technique reduces processing times and is suitable for various material compositions, including steel. The main advantage of SPS is its ability to enhance the microstructure of sintered materials, leading to improved mechanical properties.
Key features of Spark Plasma Sintering include:
- Quick processing: The rapid heating provided by electric pulses minimizes the time required for sintering, leading to significant energy savings.
- Controlled microstructure: The technique facilitates the formation of fine-grained microstructures that enhance strength and toughness in the final product.
- Versatility: SPS can be applied to a broad range of materials beyond steel, allowing for innovation in various fields.
In summary, understanding the differences between these techniques is crucial for selecting the appropriate method for specific steel applications. Each technique offers distinct advantages that cater to different requirements within the steel industry, helping optimize material performance and production efficiency.
Key Parameters Affecting Sintering
The process of sintering steel is influenced by several critical parameters that play a key role in determining the quality and properties of the final product. These factors include temperature profiles, pressure conditions, and atmospheric control. Understanding these parameters helps in optimizing the sintering process, leading to enhanced mechanical properties and performance of sintered steel components.
Temperature Profiles
Temperature is one of the most significant factors in the sintering process. It impacts the kinetic energy of the particles, which influences their movement and binding. The heating phase must be precisely controlled to avoid defects. Too high a temperature may lead to liquefaction, causing unwanted melting or deformation of the powders. Conversely, too low a temperature may result in insufficient diffusion, preventing the formation of a solid mass.
Effective temperature profiles can vary depending on the composition of the steel powders and the desired properties of the final product. Typically, the heating phase begins slowly to eliminate moisture and volatiles. Then, the temperature is raised gradually to the sintering temperature, followed by a sustained period at this temperature to allow for proper bonding. Following this, a controlled cooling phase is necessary to relieve stresses which can occur during solidification.
Pressure Conditions
Pressure applied during the sintering process can significantly influence the density and microstructure of sintered steel parts. Higher pressure can enhance atomic interaction, leading to improved particle bonding. This is particularly relevant in techniques such as Hot Isostatic Pressing (HIP), where the materials are subjected to both heat and pressure simultaneously.
Maintaining optimal pressure conditions is crucial. Too low pressure may result in porous structures, reducing the mechanical properties of the steel. On the other hand, excessive pressure can lead to unwanted deformation or cracking. Understanding the relationship between pressure and the resulting porosity and mechanical properties helps manufacturers tailor the sintering process for specific applications.
Atmospheric Control
The sintering atmosphere must be carefully controlled to prevent oxidation and contamination of the steel powders. An inert atmosphere, such as argon or nitrogen, is often recommended to protect the material during the heating phases. Additionally, the introduction of certain gases can aid in achieving desired properties, such as improved ductility or enhanced oxidation resistance.
Monitoring and adjusting the atmospheric conditions during the sintering cycle ensures consistent product quality. Deviations in the atmosphere can lead to variations in microstructure and properties, resulting in defective components. Thus, understanding and controlling the atmospheric exposure is essential for successful sintering processes.
Mechanical Properties of Sintered Steel
The study of mechanical properties in sintered steel is essential due to its significant implications for material performance in various applications. Understanding these properties allows one to better optimize the sintering process, improve manufacturing techniques, and select appropriate materials for specific uses. Sintered steel is known for its unique combination of strength, ductility, toughness, and impact resistance, making it suitable for demanding environments such as automotive and aerospace sectors.
Strength and Hardness
Strength is a primary consideration in the context of sintered steel. During the sintering process, powder particles bond together, creating a dense and strong material. The level of strength achieved can depend on factors such as sintering temperature, dwell time, and the presence of additives. Higher sintering temperatures typically enhance strength due to improved particle fusion. Additional treatments, such as heat treatment, can further enhance the hardness of the material.
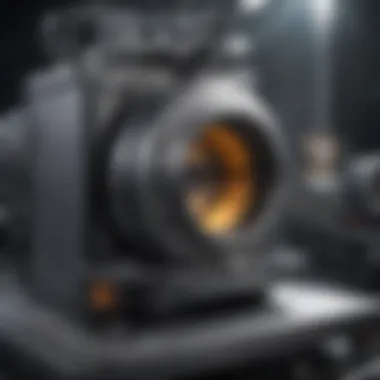
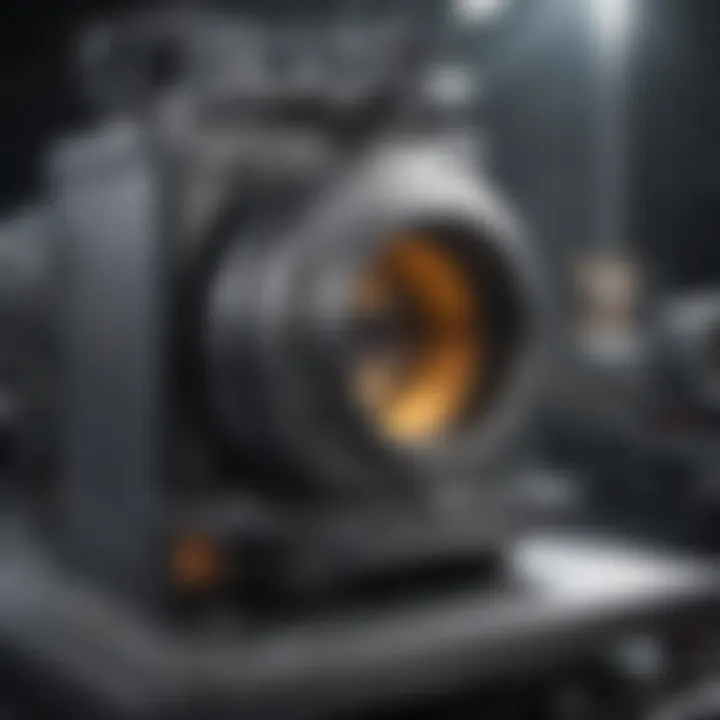
Hardness, on the other hand, relates directly to wear resistance β a crucial factor in applications where the material is subjected to mechanical stress. The hardness of sintered steel can be quantified using various scales, which provide important data for manufacturers. Ultimately, the combination of strength and hardness in sintered steel aligns with the requirements of many industrial applications, ensuring reliability and longevity of components.
Ductility and Toughness
Ductility refers to the ability of sintered steel to deform under tensile stress without fracturing. This property is vital for components that must endure dynamic loading or impact forces. While sintered steel is inherently strong, its ductility can be limited if the sintering conditions do not favor full particle bonding. Optimizing the heating profile and maintaining appropriate pressure during the process can enhance the ductility of the finished part.
Toughness is closely related to ductility and measures the material's ability to absorb energy before fractured. Sintered steel can demonstrate impressive toughness when processed correctly. The inclusion of certain alloying elements, such as nickel or chromium, can also improve both ductility and toughness, leading to more robust applications in harsh environments.
Impact Resistance
Impact resistance is another critical mechanical property for sintered steel. It quantifies a material's ability to withstand sudden forces without failing. Sintered steel components are often required to endure shocks or heavy loads in various applications, thus necessitating good impact resistance. This property can be influenced by the microstructure of the steel, as well as its density and the sintering conditions utilized.
Applications of Sintered Steel
The applications of sintered steel span a wide range of industries, showcasing the material's versatility and strength. Sintered steel components are essential in various sectors due to their unique mechanical properties and efficiencies in manufacturing. This section explores key industries that benefit from sintering technology, underlining the advantages and implications of using sintered steel.
Automotive Industry
In the automotive sector, sintered steel plays a crucial role. Parts like gears, bearings, and structural components benefit from the high strength and durability that sintered materials offer. The manufacturing process allows for complex geometries that are hard to achieve with traditional machining methods, enabling engineers to design lightweight components without sacrificing performance. One significant advantage in automotive applications is the material efficiency of sintering. When producing parts, less waste is generated compared to conventional machining practices.
Moreover, sintered steel provides excellent wear resistance, which is critical for components subject to high stress and friction. As vehicle performance standards rise, the demand for durable and efficient parts grows. By employing sintered steel, manufacturers can create components that meet stringent safety and performance regulations without unduly raising production costs.
Aerospace Sector
The aerospace industry demands materials with remarkable strength-to-weight ratios. Sintered steel fits this requirement thanks to its unique properties. Aerospace components often require high precision and can involve complex shapes. Sintered steel can be formed into intricate geometries that are not only lightweight but also strong enough to withstand extreme conditions in the atmosphere.
Components like turbine blades, brackets, and structural frames made from sintered steel contribute to improving fuel efficiency and reducing overall weight of aircraft. In this context, the ability to produce near-net-shape parts leads to reduced manufacturing time and costs. Using sintered steel also assists in meeting regulatory standards for airworthiness, as parts must sustain high stress and perform reliably in various environmental conditions.
Medical Devices
Another vital application of sintered steel is in the medical device industry. Medical devices demand high precision and reliability, with strict regulations governing their production. Sintered steel is used in surgical instruments, implants, and various components that require biocompatibility and strength.
The sintering process allows for a range of steel powders to be used, enabling manufacturers to fine-tune the mechanical properties of the final product for specific medical applications. For example, sintered components can be manufactured to have tailored porosity for bone implants, aiding in cellular integration. This adaptability is essential for ensuring optimal performance and patient outcomes.
Industrial Machinery
In industrial machinery, sintered steel parts are ubiquitous. They are utilized in various applications, including hydraulic components, gear systems, and power tools. The strength and toughness of sintered steel are paramount in machinery where reliability and efficiency are critical.
One of the benefits of using sintered steel in this sector is the ability to produce complex shapes that improve functionality and performance. For instance, sintered gears can be crafted to operate under high load conditions while maintaining precise tolerances. The cost-effectiveness of sintering also means that manufacturers can produce these components at scale, making it a strategic choice for industrial applications.
Advantages of Sintering Steel
Sintering steel is a significant method in the field of material production. This approach has several advantages, making it suitable for various applications across industries. Understanding these advantages helps evaluate why sintering is often preferred over other manufacturing processes.
Material Efficiency
One key advantage of sintering steel is its material efficiency. This process allows for the utilization of metal powders, which can be converted to final products with minimal waste. When traditional methods are used, a substantial amount of material can be lost during machining. In contrast, sintering enables the creation of complex shapes directly, reducing the need for extensive material removal. Typically, the yield from sintered parts can exceed 90%, unlike conventional machining methods where yield rates are often much lower.
In sintering, raw materials are often recycled within the system. Unused metal powders can be collected and reused for new batches. This not only minimizes total wastage but also lowers costs associated with material procurement. Additionally, using less material directly contributes to a smaller environmental footprint, aligning with sustainability goals in manufacturing.
Complex Geometries
Another notable benefit of sintering steel is the ability to produce complex geometries. When designing components, manufacturers frequently encounter challenges with intricate shapes. Sintering offers a flexible solution, accommodating complicated designs that may be difficult or impossible to create through conventional machining.
Sintered parts can incorporate features such as thin walls, fine details, and internal cavities, which are valuable in many applications. For instance, in the automotive sector, sintering can create lightweight components that enhance fuel efficiency without sacrificing strength. This capability allows industries to innovate continually, expanding product possibilities through more advanced engineering designs.
Furthermore, producing complex geometries through sintering frequently leads to a reduction in assembly steps. Many parts produced can function as integrated components, enabling more efficient assembly lines and improved structural integrity of the final products.
"Sintering technology empowers engineers to rethink design strategies, allowing for optimal performance and material conservation."
Sintering steel presents a solid choice for manufacturers. The material efficiency gained along with the capacity to create complex geometries not only enhances production but also supports broader goals of innovation and sustainability. As industries continue to evolve, embracing these advantages will be crucial for competitive edge in the market.
Challenges and Limitations
Understanding the challenges and limitations of sintering steel is crucial for professionals and researchers in material sciences. While sintering offers numerous advantages, it also presents hurdles that can affect production efficiency, material properties, and overall manufacturing costs. By recognizing these challenges, stakeholders can better navigate the complexities inherent in sintering processes.
Quality Control Issues
Quality control is a significant concern in sintering steel. Ensuring consistent quality of sintered products requires strict monitoring of various factors throughout the process. Variability in powder characteristics, such as particle size and distribution, can lead to inconsistencies in the final product's density and mechanical properties.
Moreover, temperature fluctuations during the sintering process can cause defects, which include porosity or uneven microstructure. These variations often arise from inadequate heating environments or improper control of the sintering stages. Therefore, robust quality control measures must be implemented. Techniques like laser scanning and advanced imaging systems can help in assessing the properties of sintered objects. These technological solutions aim to minimize defects while ensuring high quality and reliability of parts produced through sintering.
Cost Considerations
Cost is another critical aspect to consider when evaluating sintering technologies. Although this process can lead to material savings, the initial investment in specialized equipment is often high. Industries that rely on sintered components must carefully analyze the cost versus benefit of sintering against alternative manufacturing methods.
The costs stem not only from machinery but also from raw materials and energy consumption throughout the process. Additionally, if quality control measures are inadequate, it can lead to scrap material and increased production costs.
To minimize costs, companies can investigate ways to optimize their processes, such as reducing energy use or recycling unused powders.
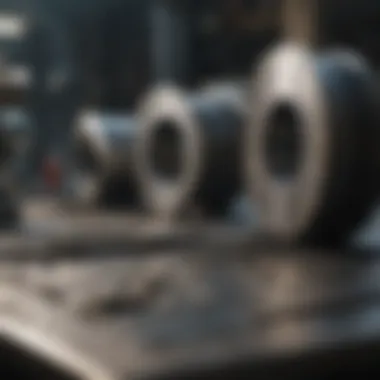
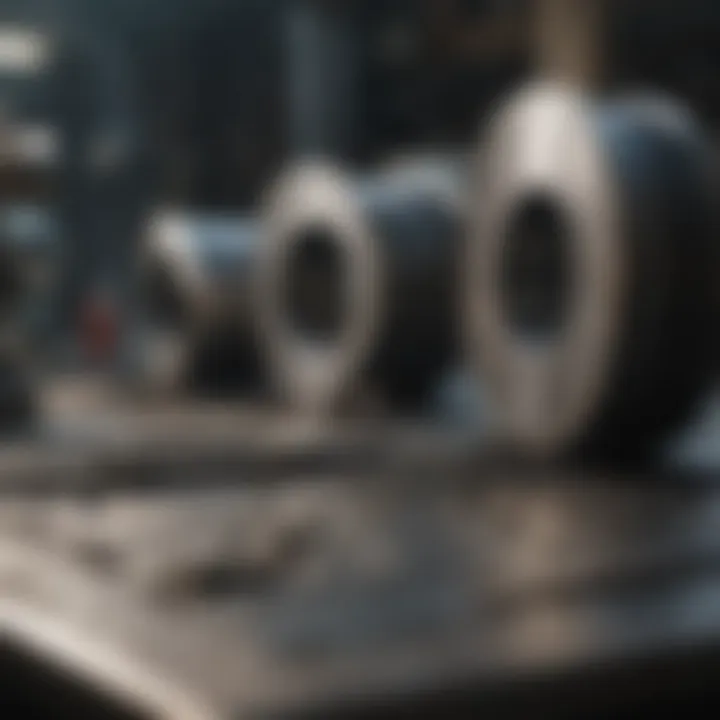
"Balancing quality and cost is paramount for the sustainability of sintering processes in competitive markets."
Understanding these challenges and limitations assists in strategizing ways to overcome them, ensuring that sintered steel continues to meet the demands of various industries.
Innovations in Sintering Technology
Innovations in sintering technology are vital for the progression and optimization of materials science. These advancements redefine how steel is processed, leading to improved efficiency, cost reduction, and enhanced product quality. Understanding the importance of innovation can provide insights into its role in staying competitive in various industries that rely on sintered materials.
Advancements in Equipment
Recent developments in equipment technology enhance the sintering process significantly. Traditional sintering furnaces are being upgraded to offer better control over temperature and atmosphere. For instance, advanced monitoring systems allow for real-time adjustments during the sintering phase. This dynamic control contributes to uniform sintering and reduced defects in the final product.
Moreover, the integration of automation and robotics minimizes human error and facilitates high-volume production. Machines that utilize computer numerical control (CNC) programming improve the reproducibility of complex geometries, which is essential in industries such as automotive and aerospace. In addition, multi-zone sintering furnaces have emerged, allowing for distinct temperature profiles across the sintering area. This feature is particularly beneficial when mixing various alloys, as it accommodates differing sintering needs.
"The evolution of equipment in sintering technology reflects the industry's commitment to innovation and quality improvement."
Alternative Energy Sources
The exploration of alternative energy sources in sintering processes is paving the way for more sustainable manufacturing practices. Conventional methods often rely on fossil fuels, which contribute to environmental degradation. However, the shift toward renewables, like solar and wind energy, is becoming increasingly feasible. The introduction of induction heating methods is another promising development. This technique provides localized energy and improves heating efficiency, minimizing heat loss.
In addition to powering equipment, energy efficiency can be optimized through the use of waste heat recovery systems. By capturing excess heat, companies can reduce overall energy consumption and costs. Furthermore, these advancements not only benefit the environment but also enhance the economic viability of sintering operations.
Sustainability in Sintering Processes
Sustainability in sintering processes has gained increasing attention in recent years due to growing environmental concerns and the need for efficient resource use. As industries push towards greener manufacturing practices, the sintering process presents both challenges and opportunities. This section explores how sustainability factors into sintering, focusing on energy consumption reduction and the recyclability of materials.
Energy Consumption Reduction
Energy consumption is often the largest operational cost in sintering processes. Recent developments aim to minimize energy usage while maintaining production efficiency. One approach involves optimizing thermal profiles during the sintering phases. By carefully controlling the heating and cooling rates, manufacturers can reduce the total energy consumed.
Utilizing advanced materials that allow for lower sintering temperatures can also contribute to this reduction. For example, powders with smaller particle sizes often sinter at lower temperatures compared to larger particles.
"Reducing energy usage not only lowers costs but also lessens the environmental impact, helping to address the pressing issue of climate change."
Another strategy involves employing alternative energy sources. Renewable energy is becoming more viable in industrial applications. Solar, wind, or thermal energy can replace conventional fossil fuels, leading to significant decreases in greenhouse gas emissions.
Recyclability of Materials
The recyclability of materials used in sintering is a key aspect of sustainable practices. Many steel powders are derived from recycled metals, and this trend is growing. Using scrap steel in the production of new powders not only reduces the demand for virgin materials but also minimizes waste. The closed-loop recycling approach is ideal as it ensures that materials remain in use for as long as possible.
Adopting effective recycling protocols within the sintering process can lead to more sustainable production. For instance, any unused or failed parts can often be reprocessed into new powder. This not only conserves resources but also reduces costs associated with material procurement.
Additionally, incorporating binders that are eco-friendly enhances the overall sustainability profile of sintered products. Choosing biodegradable options or those with lower environmental impacts can further contribute to greener manufacturing processes.
Overall, improving the sustainability of sintering processes is essential for industries looking to enhance their environmental stewardship while maintaining productivity and profitability.
Future Trends in Sintering Steel
The realm of sintering steel is evolving rapidly, influenced by technological advancements and new applications that differ from traditional uses. Such trends are not insignificant; they highlight the necessity for continued innovation in the field. Understanding these developments provides insight into the future landscape of steel manufacturing and its applications in various industries.
Emerging Applications
As industries innovate, the applications of sintered steel are expanding. Traditionally, the automotive and aerospace sectors were the primary users, but the emerging technologies now enable new possibilities. For instance, sintered steel is finding uses in
- 3D printing: As additive manufacturing gains momentum, sintered steel parts can complement printed elements, providing increased strength and durability.
- Customized medical devices: Sintered steel allows for tailored and intricate designs needed for surgical instruments or implants, enhancing functionality and patient outcomes.
- Robotics and automation: As these sectors grow, sintered steel components ensure high-performance parts that can withstand dynamic stresses and environmental challenges.
In addition to these applications, the sustainability factor drives the interest in sintering. The ability to recycle powders and reduce waste presents a compelling case for its use in future manufacturing processes.
Market Growth Predictions
The sintering steel market is anticipated to expand significantly. Analysts suggest that the growth stems from multiple factors, including:
- Increased demand for efficient manufacturing processes across sectors.
- The rising trend of lightweight materials in aerospace and automotive applications.
- Enhanced performance characteristics of sintered materials, such as high strength-to-weight ratios and corrosion resistance.
Forecasts indicate that the market may witness a compound annual growth rate (CAGR) of significant percentage over the next five years. This outlook reflects a broader trend towards advanced manufacturing processes that embrace efficiency and sustainability. The need for innovation in powder metallurgy aligns well with industry demands, paving the way for advancements in sintering technologies.
"The sintering process is critical not only for traditional production but also for emerging technologies that redefine steel applications."
The future of sintering steel looks promising. As new applications arise and markets expand, it becomes imperative for professionals in the field to keep abreast of the developments. The interplay between innovation, sustainability, and market demand will shape the evolution of sintering steel far beyond its current capabilities.
Finale
The significance of the conclusion in this article cannot be overstated. It serves as a crucial wrap-up, synthesizing the main themes and insights related to the sintering of steel. The process of sintering, deeply explored throughout the article, showcases its relevance in various industries such as automotive, aerospace, medical, and industrial machinery. Understanding the comprehensive nature of sintering steel leads to a recognition of its potential and challenges, thus emphasizing the importance of ongoing innovation and research in this field.
Summary of Key Points
In summarizing the key points, we must consider several aspects:
- Definition and Process: Sintering is a critical metal powder processing technique that involves the gradual heat application to steel powders, leading to solid mass formation.
- Types of Techniques: Various sintering techniques including conventional sintering and spark plasma sintering were discussed, showcasing their unique attributes and utilizations.
- Mechanical Properties: The mechanical properties of sintered steel, such as strength, ductility, and impact resistance, are essential for its application across different sectors.
- Applications and Innovations: The applications of sintered steel resonate through multiple industries, while ongoing innovations and advancements in equipment represent vital trends that could reshape the future of this process.
- Sustainability Factors: The considerations surrounding sustainability, including energy consumption reduction and recyclability of materials, are not just modern demands but necessities for meaningful industrial progress.
Final Thoughts
Investing in research and development in sintering technology will lead to enhanced performance and sustainability, providing significant benefits not only to the industries but also to the environment in the long term.
The future of sintering steel is bright, driven by the demand for innovative solutions and the need for sustainable practices. Each stakeholder in this arena must remain informed and engaged in order to adapt to the shifts happening within the field.