Tungsten Rhenium: Exploring Dual-Metal Systems
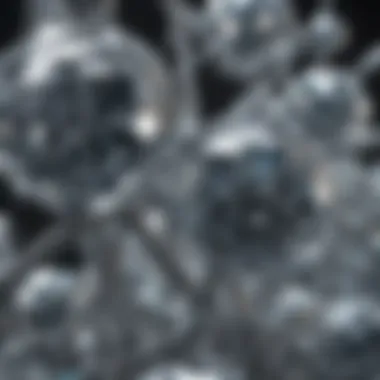
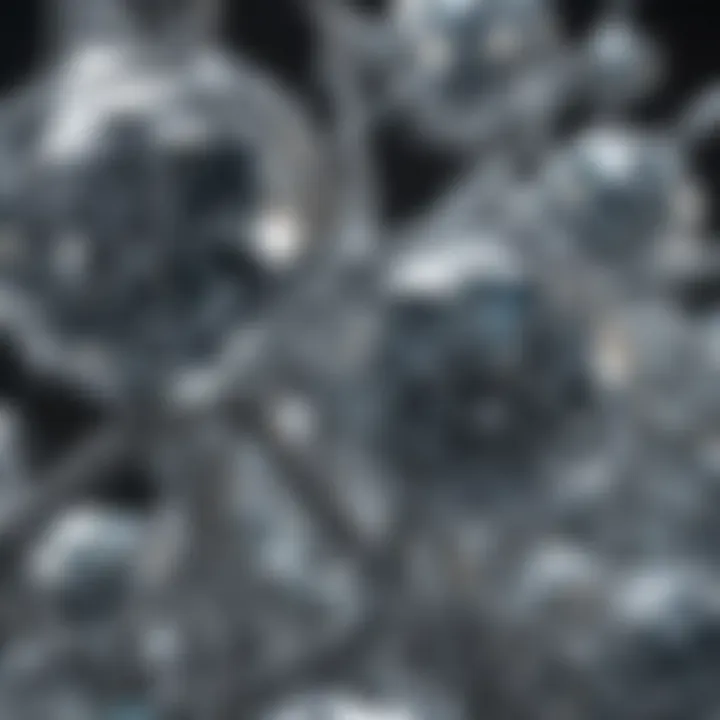
Intro
Tungsten and rhenium are two elements that possess remarkable properties and find diverse applications across various scientific and industrial domains. Tungsten, with its high melting point and unmatched density, is widely recognized for its effectiveness in situations requiring strength and durability. On the other hand, rhenium, known for its excellent resistance to wear and high temperatures, complements tungsten in numerous applications, particularly in aerospace and electronics.
The interaction between these two metals leads to the formation of tungsten-rhenium alloys, which exhibit enhanced characteristics compared to their individual components. This article delves into the unique properties, interactions, and applications of tungsten and rhenium. Through a comprehensive analysis of existing research and ongoing advancements, we aim to inform and engage a diverse audience, inviting students, researchers, and professionals into the intricate world of tungsten-rhenium systems.
By presenting current findings and insightful evaluations, we elucidate the importance of these materials in modern science and industry and outline potential future directions for research and development.
Intro to Tungsten Rhenium
Tungsten-rhenium alloys have gained significant attention due to their unique combination of properties. Understanding these elements within the framework of alloy formation is crucial. Tungsten, with its high melting point and density, serves as a robust foundation. Rhenium complements this with its remarkable resistance to heat and corrosion. Together, they create materials that are versatile and reliable under extreme conditions.
This section sets the stage for a deeper exploration of the historical context and modern significance of these alloys. Their importance resonates across various fields, from aerospace to electronics, making them subjects worthy of close examination.
Historical Context
The development of tungsten-rhenium alloys dates back to the mid-20th century. After World War II, the demand for advanced materials in various industries surged. During this time, researchers began to investigate the potential of combining tungsten with rhenium. Initially considered for military applications, these alloys found their way into civilian sectors. Their exceptional properties also came to the fore during the Space Race, where performance under extreme conditions was paramount.
As industries evolved, so did the understanding of tungsten and rhenium interactions. Research teams identified that even small amounts of rhenium added to tungsten significantly enhanced its properties. This discovery paved the way for innovations that utilized their combined strengths, especially in high-temperature applications.
Importance in Modern Science
Today, tungsten-rhenium alloys play a vital role in several scientific domains. Their key characteristics, such as high thermal stability and excellent mechanical strength, make them indispensable in aerospace, medical devices, and even nuclear applications.
Advancements in technology have driven further research into these materials. Scientists are now exploring nanostructured forms and other emerging technologies that leverage their unique properties. This ongoing investigation not only highlights their current utility but also opens the door to future innovations.
"Understanding tungsten and rhenium interactions has become essential for material science, contributing to breakthroughs in various high-tech industries."
The synergy between tungsten and rhenium offers a rich landscape for innovation. As this exploration continues, it informs both theoretical and practical applications that can have a significant impact on multiple fields.
Chemical Properties of Tungsten
Understanding the chemical properties of tungsten is essential in the exploration of our dual-metal system with rhenium. Tungsten, with the chemical symbol W, is known for its remarkable characteristics, making it vital in various applications. It possesses high melting and boiling points, exceptional density, and outstanding durability. These properties allow tungsten to perform well in extreme conditions, thus contributing to its importance in industrial applications.
Elemental Characteristics
Tungsten is a transition metal located in group 6 of the periodic table. Its atomic number is 74. One of the most defining characteristics is its density, approximately 19.25 grams per cubic centimeter, making it one of the heaviest metals. Tungsten also has a high melting point of about 3,422 °C, which is the highest of all elements. This trait allows tungsten to endure high temperatures without losing structural integrity.
In terms of reactivity, tungsten is relatively stable. It does not react with air at room temperature and only forms oxides at elevated temperatures. It can combine with gases including oxygen and nitrogen. Furthermore, the metal exhibits good corrosion resistance, particularly against acidic environments, which makes it favorable for many scientific applications.
Alloy Formation
The alloy formation of tungsten is significant for enhancing its properties. Tungsten is often alloyed with various metals, including nickel and iron, to optimize its characteristics for specific applications. When combined with rhenium, the tungsten-rhenium alloy exhibits superior mechanical strength and enhanced ductility.
These alloys are widely used in high-temperature settings, such as in aerospace and defense applications. The alloying process involves melting the metals together, followed by casting or forming into desired shapes. As the alloy cools, the properties of the materials interact, leading to new mechanical and thermal characteristics that can be advantageous in complex environments.
Chemical Properties of Rhenium
Rhenium, with atomic number 75, is a rare transition metal known for its unique chemical properties. This section focuses on the elemental characteristics of rhenium and its role in the creation of superalloys. Understanding these properties is crucial for recognizing the significance of rhenium, especially in advanced materials technology and industrial applications.
Elemental Characteristics
Rhenium is distinguished by its high melting point, which is approximately 3,180 degrees Celsius. This quality makes it one of the most heat-resistant metals, suitable for varying extreme applications. Rhenium is silver-gray in colour and possesses a very dense structure, with a density of about 21 grams per cubic centimeter. These characteristics lend rhenium notable robustness in harsh environmental conditions.
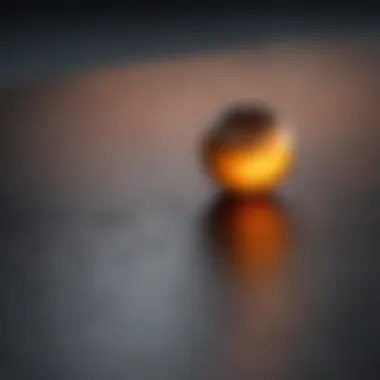
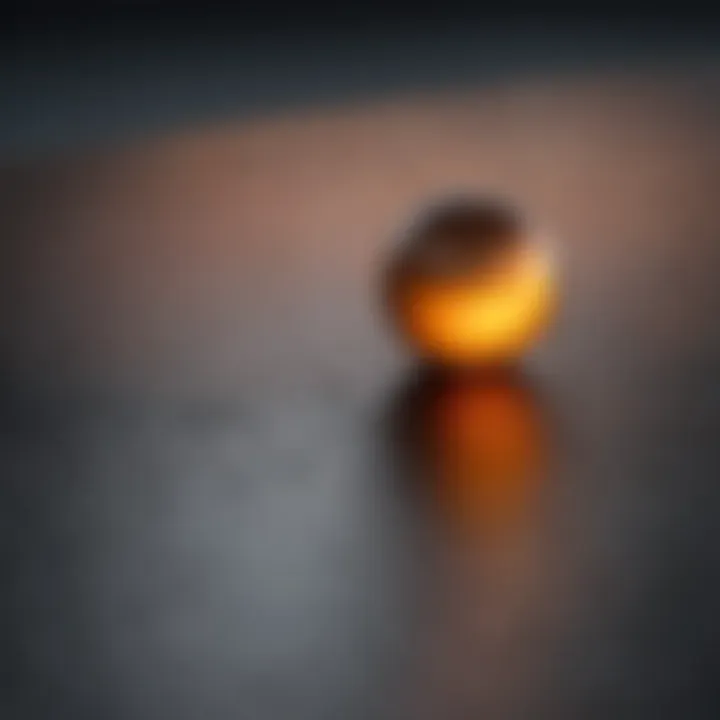
In terms of its chemical behavior, rhenium is known to exhibit oxidation states ranging from -1 to +7. This flexibility allows it to form a variety of compounds and complexes, facilitating its use in different chemical reactions. For instance, rhenium complexes have shown promising catalytic activity in reactions such as hydrogenation and oxidation.
Rhenium is also remarkably resistant to corrosion. This property is vital in industrial settings where the exposure to reactive chemicals is frequent. Importantly, it can withstand both oxidizing and reducing conditions, which makes it an asset in applications requiring durability.
Role in Superalloys
Rhenium plays a critical role in the development of superalloys, particularly nickel-based superalloys. These materials are extensively used in the aerospace and nuclear industries due to their excellent mechanical properties under extreme temperatures.
The addition of rhenium to nickel-based alloys enhances their thermal stability and tensile strength. This improvement directly impacts the longevity and performance of alloy components in high-stress environments. Superalloys with rhenium can maintain structural integrity even where temperatures soar beyond 1,000 degrees Celsius.
Furthermore, the rhenium content in these alloys aids in strengthening the crystalline structure of the metals. It can also improve the corrosion resistance of the superalloy, allowing for prolonged service life and reduced maintenance needs.
The synergy between rhenium and other metal constituents in superalloys makes it a key player in advanced material science. The continued research around rhenium's properties is essential for expanding its applications and exploring new alloys that can provide even better performance in demanding industrial contexts.
Rhenium not only provides unique properties but also enhances the overall functionality of the alloys where it is used.
Tungsten-Rhenium Alloys: Composition and Properties
Tungsten-rhenium alloys represent a unique segment in metallurgy, capturing attention for their remarkable properties. The combination of tungsten and rhenium leads to enhancements in strength, thermal stability, and corrosion resistance. These characteristics make them crucial for various applications where high-performance materials are essential. Understanding their composition and properties allows for advancements in fields such as aerospace, electronics, and nuclear technology.
Synthesis Methods
The synthesis of tungsten-rhenium alloys involves various methodologies, each tailored to achieve specific material properties. The most common methods include powder metallurgy, arc melting, and sintering.
- Powder metallurgy: This process begins with mixing tungsten and rhenium powders in desired proportions. The mixture is then compacted and sintered at high temperatures, which enables the powders to bond together at a molecular level.
- Arc melting: In this method, tungsten and rhenium are melted together using a plasma arc. This technique allows for homogeneous mixing and is essential for producing alloys with minimal impurities.
- Sintering: Sintering complements powder metallurgy, as it involves heating the packed powders to below their melting points. This process promotes solid-state diffusion and forms stronger bonds between the tungsten and rhenium atoms, enhancing the overall material integrity.
These methods are critical for developing alloys that meet the required engineering specifications for high-temperature or high-stress environments.
Mechanical Properties
Tungsten-rhenium alloys exhibit exceptional mechanical properties, attributed to the solid solution strengthening effect. When rhenium is added to tungsten, it raises the material's tensile strength and hardness, making it suitable for applications that demand resilience under mechanical stress.
- High tensile strength: The incorporation of rhenium can lead to tensile strengths exceeding those of pure tungsten, especially in elevated temperature conditions.
- Ductility: Although generally less ductile than pure tungsten, tungsten-rhenium alloys provide improved ductility compared to their pure counterparts, which helps in processing and manufacturing.
- Fatigue resistance: The alloy is known for its outstanding fatigue resistance, making it suitable for components subjected to cyclic loading.
These mechanical characteristics underscore the relevance of tungsten-rhenium alloys in industries requiring materials that can withstand extreme conditions.
Thermal Stability
One of the most significant advantages of tungsten-rhenium alloys lies in their thermal stability. Different industrial applications, such as in aerospace and electronics, often encounter extreme thermal environments.
- High melting points: Both tungsten and rhenium have high melting points, making the alloys capable of performing well at elevated temperatures. This stability reduces the risk of material degradation.
- Thermal expansion: The thermal expansion coefficients of tungsten-rhenium alloys are relatively low. This property minimizes dimensional changes under thermal load, which is crucial in precision engineering applications.
- Oxidation resistance: The alloy's composition provides good resistance to oxidation at high temperatures, further enhancing longevity and performance in challenging environments.
"The combination of tungsten and rhenium offers a compelling proof of how metallurgy can push the boundaries of material properties, enabling innovations across different fields."
Maintaining a focus on the synthesis methods, mechanical properties, and thermal stability provides a comprehensive understanding of tungsten-rhenium alloys. This knowledge is pivotal for both scientific research and practical applications across industries.
Applications of Tungsten-Rhenium Alloys
Tungsten-rhenium alloys find significant use in various high-performance fields. Their exceptional properties make them suitable for demanding applications. These alloys combine the strengths of both tungsten and rhenium, providing superior thermal stability and mechanical performance.
The applications of tungsten-rhenium alloys can be categorized into major industries, reflecting their importance in modern science and technology. The unique characteristics of these alloys, such as high melting points, strong tensile strength, and resistance to wear, set them apart from other materials. These benefits contribute greatly to enhancing the performance and reliability of industrial systems.
Aerospace Industry
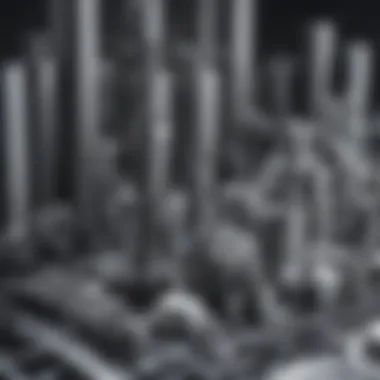
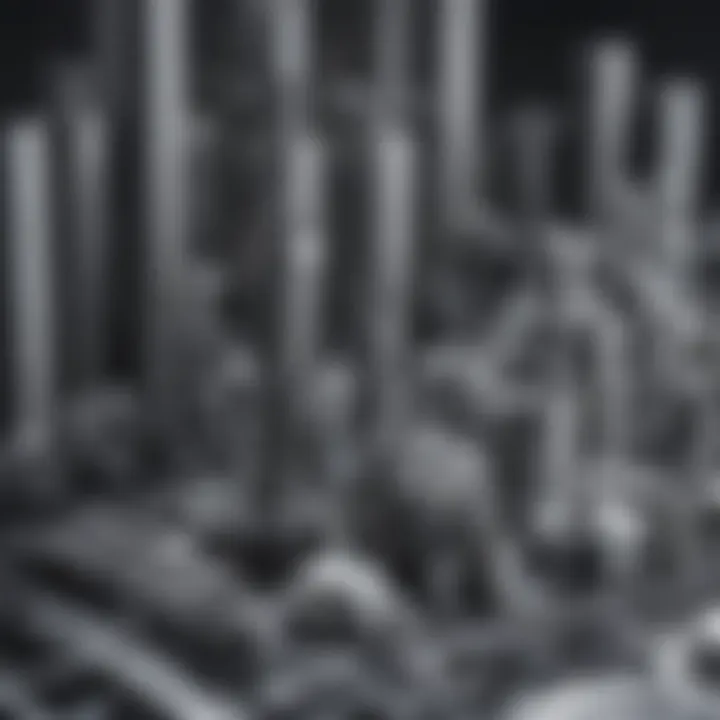
In the aerospace sector, the need for materials that can withstand extreme conditions is critical. Tungsten-rhenium alloys play a vital role in components that face high temperatures and pressures, such as rocket engines and heat shields. The specific properties of these alloys allow them to maintain structural integrity under extreme stress, providing reliability in critical missions.
Common applications include:
- Rocket engine components: where high thermal stability is crucial.
- Thermocouples: providing accurate temperature measurements in harsh environments.
These uses highlight the relevance of tungsten-rhenium alloys in ensuring safety and success in aerial operations. The ability to perform effectively in extreme conditions assists aerospace engineers in designing more efficient and advanced systems.
Electronics and Electrical Applications
The electronics industry benefits significantly from tungsten-rhenium alloys, particularly in applications where conductivity and durability matter. These materials are often employed in high-temperature electronics, ensuring the devices function well even in challenging conditions.
Applications in this field include:
- Electrical contacts: where wear resistance is essential for longevity.
- Filaments: used in vacuum tubes and specialized lighting solutions.
The unique conductivity properties of tungsten-rhenium alloys enhance performance in electrical components, making them a preferred choice in applications that require high reliability and efficiency.
Nuclear Applications
Nuclear technology also utilizes tungsten-rhenium alloys due to their ability to withstand radiation and thermal stresses. Components in nuclear reactors need to maintain performance over long periods under high radiation. Tungsten-rhenium alloys prove effective in these demanding environments.
Key utilization areas are:
- Control rods: where high resistance to corrosion and thermal conductivity is needed.
- Encapsulation: of radioactive materials to ensure safety and containment.
These applications underscore the strategic significance of tungsten-rhenium alloys in not only enhancing functionality but also ensuring safety in nuclear technology.
Conclusion: The applications of tungsten-rhenium alloys span diverse industries, showcasing their critical role in modern technology. Their remarkable properties enable innovation and efficiency in complex systems, reinforcing their value in both established and emerging technologies. \n By addressing their distinctive benefits, this section illustrates the essential place of tungsten-rhenium alloys in cutting-edge applications.
Advantages of Tungsten-Rhenium Alloys
The exploration of tungsten-rhenium alloys reveals a plethora of advantages that make them indispensable in numerous industrial and scientific applications. In a world increasingly reliant on advanced materials, understanding the unique characteristics of tungsten-rhenium alloys can lead to enhanced performance in high-stress environments. This section delves into two primary advantages of these alloys: strength and durability and resistance to corrosion.
Strength and Durability
The strength and durability of tungsten-rhenium alloys are among their most notable benefits. Tungsten, known for its impressive tensile strength, contributes significantly to the overall performance of these alloys. When combined with rhenium, the hardness and resilience of the material increase, making it capable of withstanding extreme temperatures and pressures. This property is particularly critical in aerospace applications, where materials must endure the rigors of flight without compromising structural integrity.
- High melting point: The melting point of tungsten is around 3,422 °C (6,192 °F), and rhenium adds to this thermal stability. This allows the alloys to perform effectively in environments where most materials fail.
- Superior mechanical properties: The alloy’s ability to maintain mechanical strength even at elevated temperatures makes it suitable for applications in turbine engines and other high-performance machinery.
These combined properties mean tungsten-rhenium alloys are not only stronger than many alternatives but also possess a longer operational lifespan. Thus, engineering applications benefit greatly from their use, as the durability translates into reduced downtime and maintenance costs.
Resistance to Corrosion
Another significant advantage of tungsten-rhenium alloys is their remarkable resistance to corrosion. Rhenium’s chemical structure enhances the protective qualities of tungsten, allowing these alloys to endure corrosive environments that would typically degrade other materials. This characteristic is particularly beneficial in specific industrial contexts, such as in chemicals and oil refining.
- Chemical inertness: Tungsten-rhenium alloys show high resistance to oxidation and other chemical reactions which could lead to degradation. This enables their application in harsh environments without the risk of rapid deterioration.
- Long-term stability: The alloys maintain their properties over extended periods even when exposed to aggressive substances. This stability ensures consistent performance in challenging conditions.
The unique combination of strength, durability, and resistance to corrosion makes tungsten-rhenium alloys a preferred choice for a wide range of industries.
In summary, the advantages of tungsten-rhenium alloys, particularly their strength, durability, and resistance to corrosion, make them extremely valuable in today’s advanced technological landscape. Recognizing these benefits can foster the development of innovative applications and further research into their properties.
Challenges and Limitations
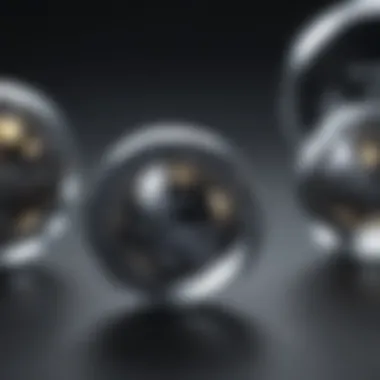
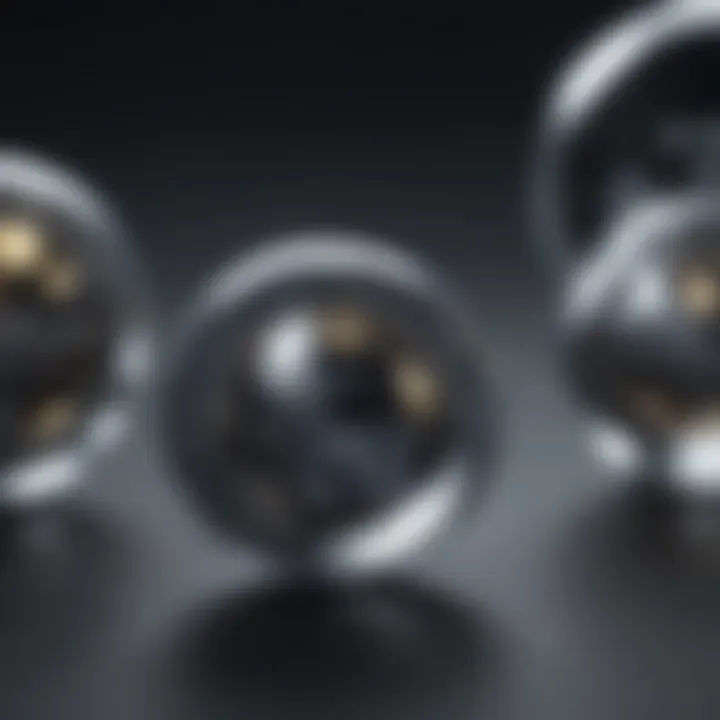
In the study and application of tungsten-rhenium alloys, it is crucial to evaluate both the challenges and limitations these materials face. Understanding these obstacles allows scientists and engineers to innovate better solutions and enhances the overall utility of tungsten-rhenium composites. Identifying cost factors and processing challenges is vital to ensure these substances fulfill their potential across many demanding fields like aerospace and electronics.
Cost Factors
Tungsten-rhenium alloys are often more expensive than other metallic materials. The high market prices of the constituent metals are a significant reason for this. Rhenium itself is one of the rarest elements in the Earth's crust. Thus, its procurement can be costly and sometimes limited to specific geographical regions. This scarcity generates fluctuations in pricing, which can impact large manufacturing projects reliant on consistent material availability.
Additionally, the costs tied to refining and processing these metals into usable alloys contribute to overall expenses. The economic analysis shows that while the performance of tungsten-rhenium alloys may justify their use in high-end applications, the investment required can be a barrier for less critical projects. This makes cost management strategies important for companies looking to utilize these materials.
Processing Challenges
The fabrication of tungsten-rhenium alloys incurs distinct processing challenges. Their high melting points make standard manufacturing methods difficult. Techniques such as sintering require careful temperature control and precise timing to achieve the desired material properties. Inadequate processing can lead to internal defects, affecting the mechanical strength and thermal stability of the final product.
Moreover, the tendency of tungsten and rhenium to form brittle compounds during alloying can complicate manufacturing efforts. This necessitates the development of advanced techniques and equipment to control processing environments. For example, inert atmospheres or vacuum environments are often required to maintain material integrity during heating.
It is also important to note that these processing challenges can lead to longer production times and increased waste, further driving up costs and time associated with tungsten-rhenium alloy production.
"While tungsten and rhenium alloys provide superior performance, these materials come with their challenges that need addressing to maximize their potential."
In summary, the challenges surrounding cost factors and processing techniques are fundamental to understanding tungsten-rhenium alloys' overall landscape. These limitations encourage ongoing research and development efforts aimed at finding more efficient and cost-effective methods of production.
Research Frontiers in Tungsten-Rhenium Studies
Research surrounding tungsten-rhenium alloys has evolved considerably, marking a significant area of interest within materials science. Exploring this dual-metal system reveals opportunities and challenges that are crucial for advancement in various applications. This section delves into the forefront of ongoing studies, focusing on nanostructured alloys and emerging technologies related to tungsten and rhenium.
Nanostructured Alloys
Nanostructured alloys of tungsten and rhenium are gaining attention due to their enhanced mechanical properties and performance in extreme environments. These materials exhibit unique characteristics arising from their nanoscale features. Researchers are experimenting with various methods to produce these alloys, aiming to optimize their strength, ductility, and thermal stability.
The grain size reduction in nanostructured alloys significantly improves their hardness while also maintaining toughness. This dual benefit makes them highly desirable for industries requiring materials that can withstand considerable stress and high temperatures.
The benefits of nanostructured tungsten-rhenium alloys include:
- Exceptional strength-to-weight ratios.
- Increased resistance to thermal degradation.
- Improved overall performance in high-stress applications, such as aerospace components.
However, the production of these alloys is not without challenges. Techniques like mechanical milling or chemical vapor deposition are often required, and the scalability of these processes can be limiting factors. Achieving uniform particle size distribution is crucial for obtaining the desired performance characteristics, which demands further research and refinement in processing techniques.
Emerging Technologies
The landscape of tungsten-rhenium studies is being reshaped by emerging technologies aimed at maximizing the potential of these alloys. Innovations in additive manufacturing, for instance, allow for precise control over the microstructure of materials. This technique can improve the properties of tungsten-rhenium combinations significantly, revolutionizing applications in aerospace and defense sectors.
Another area of exploration is the application of advanced coating techniques, enabling the enhancement of surface properties without compromising the bulk material attributes. These coatings can provide additional benefits such as:
- Improved corrosion resistance.
- Enhanced thermal performance.
- Greater longevity in harsh operating conditions.
In addition, researchers are investigating the recycling and sustainability aspects of tungsten-rhenium alloys. The effort involves finding ways to reclaim rhenium from scrap or used components, which contributes to a circular economy approach in materials science. The integration of these technologies not only addresses production efficiency but also environmental considerations, making tungsten-rhenium alloys more viable for broader applications.
"As the demand for high-performance materials continues to rise, the importance of research into tungsten-rhenium alloys cannot be overstated. Innovations in nanostructured alloys and emerging technologies will shape the future of engineering and materials science."
With continued investment in these research frontiers, the future of tungsten-rhenium alloys shows significant promise, paving the way for their adoption in increasingly advanced applications.
The End
In the realm of material science, the transition from research to practical applications is vital. The conclusion of this article highlights several essential elements about tungsten-rhenium alloys. These alloys embody a unique combination of properties that ensure their relevance in high-performance sectors.
Summary of Findings
The investigation into tungsten and rhenium has revealed their intricate characteristics. Notably, tungsten showcases high density and boiling point, while rhenium contributes exceptional resistance to thermal and chemical degradation. The synergy between these elements results in robust alloys capable of withstanding extreme environmental conditions, especially in aerospace and nuclear applications. The discussion on alloy formation methods further emphasizes how precise control over composition can enhance mechanical attributes. Overall, the article consolidates the knowledge surrounding these materials and recognizes their pivotal role in advancing technology.
Future Outlook
Looking ahead, research into tungsten-rhenium alloys remains promising. Innovations in nanostructured alloys could unlock enhanced performance traits, encouraging further exploration in energy-efficient applications. The advent of emerging technologies, such as additive manufacturing, can pave pathways toward custom alloy formulations with tailored properties. As industries evolve, the demand for high-performance materials will likely bolster continued investigations into tungsten and rhenium systems. Thus, the future is ripe with potential, as scientists seek to leverage these elements in innovative ways.