Understanding Aluminum Alloys: Properties & Uses
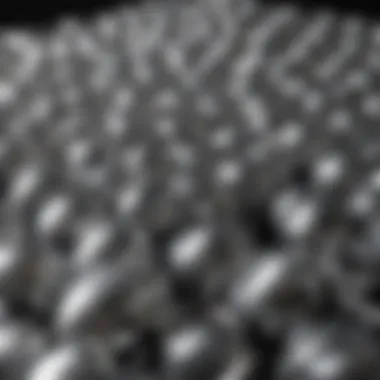
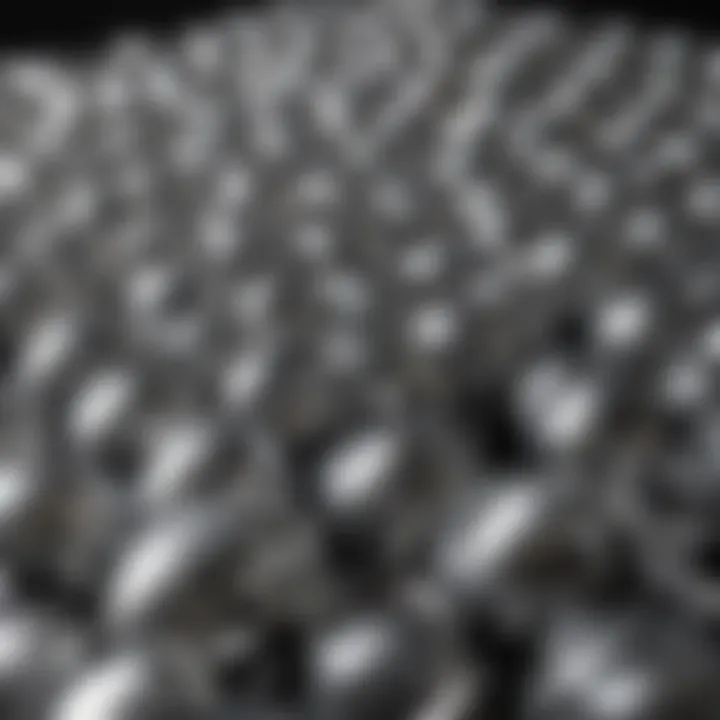
Intro
Aluminum alloys have become integral in various industries due to their unique properties and versatility. These alloys are not just light and strong, but also offer excellent corrosion resistance, making them suitable for a wide range of applications. Understanding the different types of aluminum alloys and their characteristics is essential for students, researchers, and industry professionals who seek to maximize the benefits of this material.
Aluminum alloys are generally divided into two categories: wrought and cast alloys. Each of these categories has its own subtypes based on specific compositions and properties. Wrought alloys are typically formed through mechanical working processes, such as rolling or extrusion, while cast alloys are made by pouring molten aluminum into molds.
The significance of studying aluminum alloys extends beyond theoretical knowledge. In practice, the properties of these alloys directly impact their applications in fields like aerospace, automotive, construction, and consumer goods. This article aims to elaborate on the common aluminum alloys, their properties, and the distinct applications that arise from these characteristics.
Preamble to Aluminum Alloys
Aluminum alloys play a crucial role in modern manufacturing and various engineering fields. The versatility of these materials makes them suitable for a wide range of applications, from aerospace to automobile industries. Understanding aluminum alloys is important for anyone involved in material science or engineering, as it bridges the gap between raw material properties and their practical uses.
The distinct advantages of aluminum alloys include their lightweight nature, excellent corrosion resistance, and good mechanical properties. Their adaptability allows engineers to select the most appropriate alloy for specific requirements, optimizing performance and reducing costs. Through examination of these alloys, professionals can improve the efficiency of their designs, thus contributing to better products.
In this section, we will define what aluminum alloys are and outline their historical development, offering insight into how these materials have evolved in various applications over time.
Definition of Aluminum Alloys
Aluminum alloys are materials formed by mixing aluminum with other elements, enhancing specific properties for diverse applications. These elements may include copper, magnesium, manganese, silicon, and zinc. The combination results in various types of aluminum alloys, categorized mainly into wrought and cast alloys.
Wrought alloys are shaped through mechanical processes such as rolling or extruding, while cast alloys are produced by pouring molten aluminum into molds. This distinction helps engineers choose the right alloy based on how it will be used and processed.
Historical Development
The history of aluminum alloys dates back to the early 19th century. Initially, pure aluminum was considered a precious metal before methods for extraction evolved. The introduction of alloying elements revolutionized its use, leading to the creation of various alloys suitable for different industrial needs.
Significant developments include the advent of heat-treatable alloys during World War II, particularly in aerospace. Engineers began to understand that alloying and heat treatment could significantly enhance the performance of aluminum. Post-war advancements in technology led to further innovation, resulting in the modern alloys we use today.
In summary, knowledge of aluminum alloys is essential for optimizing designs in engineering processes. This understanding aids in selecting the right material for specific tasks, yielding superior results and driving innovation across industries.
Classification of Aluminum Alloys
The classification of aluminum alloys is essential in understanding their diverse applications and properties. This segment aims to delineate two primary categories: wrought and cast alloys. Each classification serves specific industry needs and has unique advantages. Knowing how these alloys are categorized helps in selecting the right type for particular tasks. The classification is based on the manufacturing process and composition, which directly influences factors such as strength, weight, and corrosion resistance.
Wrought Alloys
Wrought alloys are formed by mechanical processes such as rolling, forging, or extrusion. The primary feature of wrought alloys is their ability to be shaped without melting. This method enhances the mechanical properties through work hardening. Wrought alloys are categorized into series based on their main alloying elements. The common series include Series 1000, Series 2000, Series 3000, and others.
- Series 1000: Known for excellent corrosion resistance and high thermal conductivity. Used in electrical applications.
- Series 2000: Contains copper as the main alloying element, recognized for high strength. Common in aerospace applications.
- Series 3000: Manganese is the principal element, offering good corrosion resistance and workability. Often used in chemical and food processing.
- Series 4000: Primarily contains silicon, used for welding and brazing due to its fluidity when molten.
- Series 5000: Magnesium is the key element, providing high resistance to corrosion. Used widely in marine environments.
- Series 6000: A versatile category combining magnesium and silicon, commonly used in structural applications and buildings.
- Series 7000: Zinc is the primary alloying element, known for its strength-to-weight ratio, used in high-performance applications like sports equipment.
- Series 8000: Contains lithium and other elements, primarily used in packaging.
The transformation of wrought aluminum alloys confers significant advantages, including better mechanical properties and the ability to create complex shapes. Additionally, the wrought process allows for finer controls on properties, which leads to an overall improvement in performance.
Cast Alloys
Cast alloys are produced by pouring molten aluminum into a mold. This method allows for intricate shapes and reduces processing costs. Cast alloys are typically categorized into two general groups: those containing silicon and those without.
- Aluminum-Silicon Alloys: These alloys are known for their excellent fluidity and so are widely used in casting applications. They have good corrosion resistance and low thermal expansion. Common applications include automotive components and engine blocks.
- Aluminum-Copper Alloys: Recognized for their high strength, they are mainly used in aerospace and transportation industries. They exhibit excellent machinability and wear resistance.
- Aluminum-Magnesium Alloys: These alloys provide good corrosion resistance and are often used in marine applications due to their lightweight properties.
- Aluminum-Zinc Alloys: Characterized by high strength, these alloys are suitable for structural applications, particularly in aerospace.
Cast aluminum alloys allow for complex designs and rapid manufacturing. However, they typically have lower mechanical properties compared to wrought alloys. Thus, the choice between wrought and cast alloys often depends on the specific requirements of the application and the desired properties of the final product.
Understanding the differences between wrought and cast aluminum alloys rises to forefront when selecting materials for specific functional needs in various industries. The right choice can significantly affect performance and durability.
Common Wrought Aluminum Alloys
Wrought aluminum alloys make up a significant portion of the aluminum market. Their unique properties and versatility render them ideal for a variety of applications, ranging from aerospace to consumer products. Understanding these alloys is crucial for anyone involved in selection, design, or manufacturing. Each series of wrought alloys has distinct characteristics and benefits that cater to different needs and applications. This section explains these series in detail, enabling readers to grasp their importance and utility in diverse sectors.
Series
Series 1000 alloys consist of 99% or higher aluminum content. These alloys exhibit excellent corrosion resistance and high thermal and electrical conductivity. They are commonly used in applications requiring high thermal conductivity, such as heat exchangers and electrical conductors. One limitation, however, is their lower strength compared to other alloy series.
Series
Series 2000 alloys are primarily alloyed with copper. They are known for their exceptional strength and are often used in aerospace applications. However, these alloys are less resistant to corrosion. Therefore, surface treatments are often employed to enhance their durability. The notable alloys in this series include 2024 and 2011, which are commonly used in aircraft structures.
Series
Series 3000 alloys include manganese as a principal alloying element. They are known for moderate strength and good corrosion resistance. Their ductility makes them suitable for forming processes. These alloys find applications in manufacturing beverage cans and architectural applications. The relatively low strength of this series might not suit every application but is highly acceptable for common uses.
Series
Series 4000 alloys are mainly alloyed with silicon. They are known for their good wear resistance and low expansion characteristics. They are often utilized in welding applications and automotive components. The aluminum-silicon alloy offers a balance between strength and ductility, allowing for ease in processing. Alloy 4047 is a common choice in this series for applications requiring good corrosion resistance and fluidity in casting.
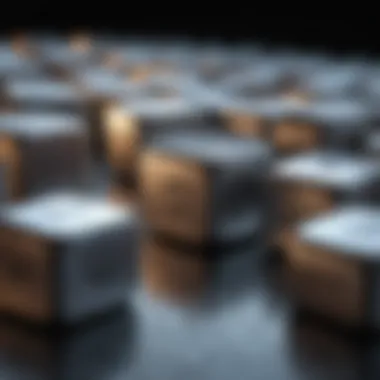
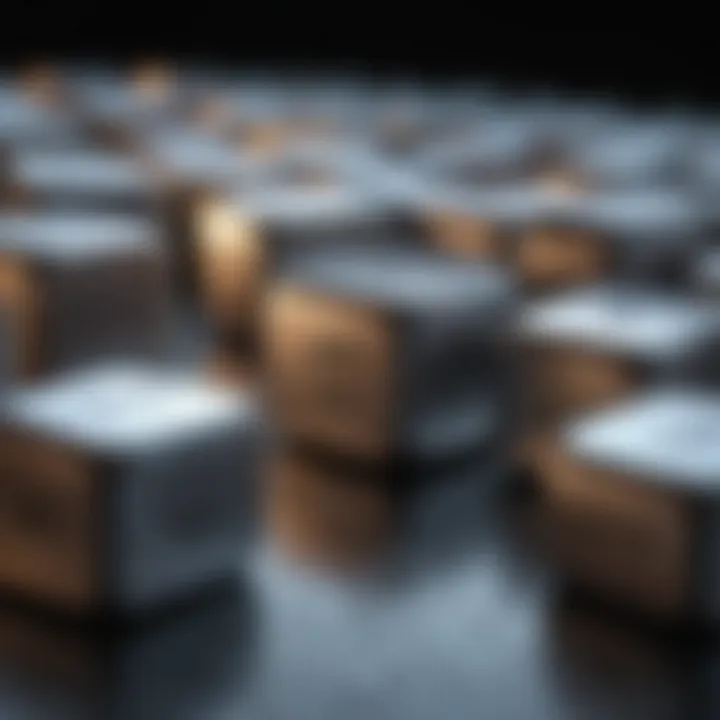
Series
Alloys in the 5000 series typically contain magnesium as their chief alloying agent. They exhibit excellent corrosion resistance, good weldability, and moderate to high strength. These factors make them suitable for marine environments as well as architectural applications. Alloy 5052 is relatively common in this series, widely used in shipbuilding and automotive sectors. The excellent anodizing capabilities further enhance their utility in aesthetic applications.
Series
The 6000 series represents a broad range of alloys and includes magnesium and silicon. They are versatile, comprising good mechanical properties and high corrosion resistance. This series is frequently used in structural applications, such as buildings and bridges. Alloys such as 6061 and 6063 are popular due to their excellent weldability and formability, making them favorites in the construction and transportation sector.
Series
Consisting primarily of zinc, series 7000 alloys are known for their high strength, making them suitable for aerospace applications. However, they are less corrosion resistant compared to other series. It is common to apply protective coatings to mitigate this issue. Alloy 7075 is one of the most recognized in this series, often used in aircraft components and high-stress applications.
Series
Series 8000 accommodates various elements, primarily used for applications outside of the structural material domain. Common uses include aluminum foil and wire. Alloys such as 8006 find application in packaging materials. The composition varies widely, allowing for customization of properties to suit specific needs.
Understanding these series enriches knowledge crucial in industries that rely on aluminum, enhancing decision-making in material selection.
Common Cast Aluminum Alloys
Cast aluminum alloys represent a vital segment in the realm of aluminum materials, crucial for a wide range of applications. Their significance stems from the unique properties and versatility they offer across various industries. When discussing aluminum alloys overall, recognizing the specific traits of cast aluminum alloys helps in understanding their role in manufacturing and engineering applications. With the right advantages, such as good fluidity, excellent corrosion resistance, and the ability to create complex shapes, these alloys often become preferred materials in many sectors.
Aluminum-Silicon Alloys
Aluminum-silicon alloys are among the most widely used cast aluminum alloys. They are notable for their excellent casting characteristics that allow for high volume production with minimal defects. The physical properties are enhanced with the addition of silicon, resulting in increased resistance to corrosion and a lower coefficient of thermal expansion. This makes them particularly suitable for applications like engine blocks and other components in the automotive sector.
In combination, these factors yield significant benefits. The ease of machining and resistance to wear further solidify aluminum-silicon alloys as a popular choice in both industrial and consumer products.
Aluminum-Copper Alloys
Aluminum-copper alloys, while less common than aluminum-silicon alloys, play an important role in specific applications. They are recognized for their high strength and excellent machinability. However, their use is somewhat limited due to a tendency to corrode, which can be mitigated through careful selection and processing. Typically, these alloys find their place in aerospace applications, where high strength-to-weight ratios are essential for structural integrity and performance.
This strength comes at a cost of ductility, meaning that any forming operations must be approached with caution. Nonetheless, the overall performance characteristics often justify their use in demanding conditions.
Aluminum-Magnesium Alloys
Aluminum-magnesium alloys are valued for their corrosion resistance and good weldability. They provide a balance of strength and lightweight properties, making them an excellent choice for marine applications and automotive structures. Their casting capabilities allow for intricate designs, which expands the range of possible uses.
The magnesium content enhances the mechanical strength while ensuring that the materials remain lightweight. This quality makes them particularly favorable in industries focused on efficiency and performance, such as in aerospace and high-end automotive engineering.
Aluminum-Zinc Alloys
Aluminum-zinc alloys are another subset of cast aluminum that exhibit good strength and resistance to stress corrosion cracking. This makes them ideal for applications that experience high loads and stress conditions. While their direct corrosion resistance is not as robust as other alloys, the mechanical properties compensate for this drawback.
These alloys are often used in the production of heavy-duty structural components and in the aerospace industry for high-strength applications. The added zinc modifies the basic properties of aluminum, allowing for increased performance in certain specialized fields, enabling engineers to exploit their capabilities to the fullest.
"The choice of alloy is critical in engineering applications as it determines the performance characteristics of the final product."
In summary, understanding the characteristics of common cast aluminum alloys provides crucial insights for applications across various sectors. Each alloy type holds unique properties that tailor to specific needs, making their understanding integral to selecting the right materials for projects.
Key Properties of Aluminum Alloys
Understanding the key properties of aluminum alloys is crucial for applications across various industries. These properties help in assessing the suitability of specific alloys for different tasks. This section examines mechanical properties, corrosion resistance, thermal conductivity, and electrical conductivity. Each aspect plays an important role in determining how aluminum alloys perform in real-world scenarios.
Mechanical Properties
Mechanical properties are fundamental to understanding how aluminum alloys behave under different loads. This includes tensile strength, yield strength, and fatigue resistance, which are all significant for structural and engineering applications.
Tensile Strength
Tensile strength refers to the maximum stress a material can withstand while being stretched or pulled before breaking. It is a key characteristic that directly influences an alloy's performance in load-bearing applications. The tensile strength of aluminum alloys can vary significantly based on their composition and processing methods. For instance, alloys from the 6000 series often demonstrate higher tensile strength, making them suitable for structural applications.
One of the main advantages of high tensile strength is that it allows for lighter components without sacrificing performance. This can lead to decreased fuel consumption in automotive and aerospace sectors. A potential disadvantage, however, is that increasing tensile strength can sometimes lead to reduced ductility, impacting how an alloy can be formed or welded.
Yield Strength
Yield strength is the stress level at which a material begins to deform plastically. This property determines the maximum load that can be applied to an alloy without causing permanent deformation. In engineering designs, understanding yield strength is essential for ensuring components can handle operational loads.
The notable characteristic of yield strength is its relationship with safety margins. High yield strength in aluminum alloys allows for more efficient designs, as engineers can minimize the material used while ensuring safety. However, similar to tensile strength, optimizing for yield strength could limit other properties, such as ductility, which may be needed for specific applications.
Fatigue Resistance
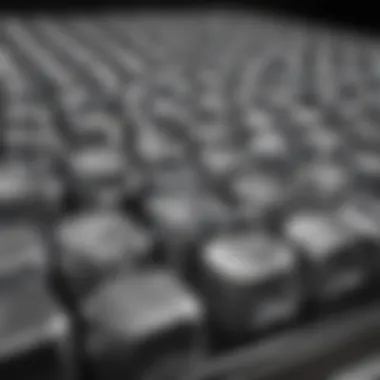
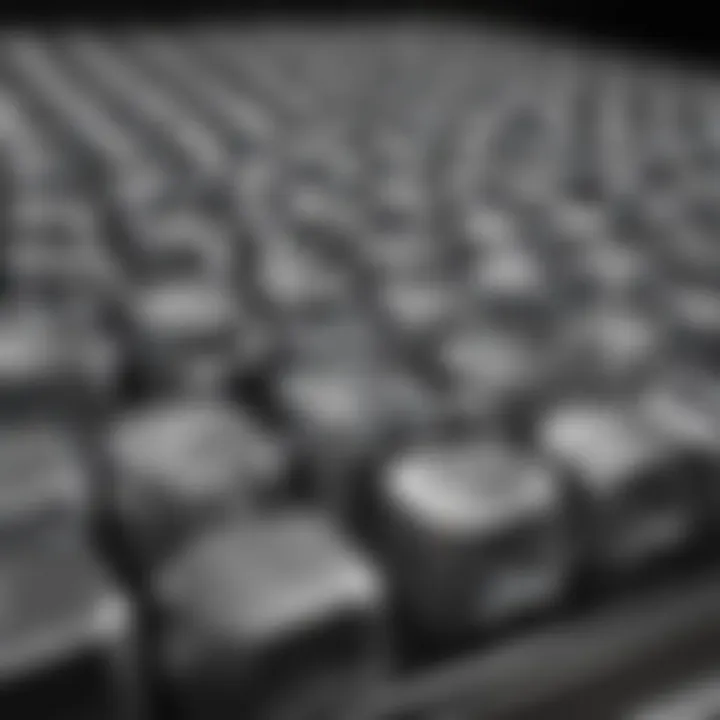
Fatigue resistance indicates how well a material can withstand repeated loading and unloading cycles. This property is especially critical in components subjected to fluctuating or cyclic stresses, such as in aircraft or automotive parts.
A key feature of aluminum alloys with good fatigue resistance is their ability to maintain performance over extended periods without failure. This is beneficial in ensuring reliability and safety in long-term applications. On the downside, poor fatigue resistance in some alloys can lead to unexpected failures after prolonged use.
Corrosion Resistance
Corrosion resistance is another vital property of aluminum alloys, essential for longevity and durability in various environments. Aluminum naturally forms a protective oxide layer when exposed to air. This layer helps inhibit further oxidation, making aluminum alloys generally resistant to corrosion.
However, the effectiveness of this layer can be affected by environmental factors such as humidity, salt, and pollution. In specific applications, especially those in marine environments, additional protective coatings are advisable to enhance corrosion resistance. Understanding and improving corrosion resistance is particularly relevant for industries like aerospace and construction, where material integrity over time is paramount.
Thermal Conductivity
Thermal conductivity is a measure of a material's ability to conduct heat. Aluminum alloys are known for their excellent thermal conductivity, which is beneficial for applications that require effective heat dissipation, such as in heat exchangers and electronic housings.
The ability to conduct heat can also influence how aluminum alloys are processed. For instance, good thermal conductivity allows for faster production in casting and machining processes. Nevertheless, in applications where heat retention is needed, high thermal conductivity may not be desirable, and certain alloys might be selected to address that requirement.
Electrical Conductivity
Electrical conductivity is a crucial property in applications like wiring and communication systems. Aluminum alloys exhibit good electrical conductivity, although it is generally lower than that of copper. However, the lower density of aluminum makes it advantageous for certain applications, where weight savings are crucial, such as in overhead power lines.
For many electronics applications, electrical conductivity is often balanced against mechanical properties like strength. Some alloys can be tailored to optimize combinations of these properties, making them suitable for a range of uses.
In summary, the key properties of aluminum alloys comprise mechanical characteristics, corrosion resistance, thermal and electrical conductivity. Recognizing these elements aids in selecting the right alloy for specific applications, ensuring performance and durability.
Applications of Aluminum Alloys
The applications of aluminum alloys are extensive and critical for many industries. Their unique properties such as lightweight, corrosion resistance, and strength make them invaluable in various fields. Understanding these applications is important for engineers, manufacturers, and researchers alike. By examining how these alloys are used in practical scenarios, we can appreciate their versatility and significance in modern technology and construction.
Aerospace Industry
Aluminum alloys play a vital role in the aerospace industry due to their lightweight properties. The demand for fuel efficiency and reduced payload weight drives the use of these materials in aircraft construction. For instance, series 7000 and certain 6000 series alloys are favored for structural components. These alloys provide high strength-to-weight ratios, helping to improve the overall performance of aircraft. Moreover, resistance to corrosion is essential in aviation, as components are constantly exposed to harsh environments.
Using aluminum means not only can manufacturers save on weight but also reduce fuel consumption in daily operations, directly impacting operational costs.
Automotive Industry
In the automotive sector, aluminum alloys contribute significantly to achieving fuel efficiency and decreasing greenhouse emissions. Major car manufacturers increasingly embrace aluminum in the production of vehicle bodies and chassis. Alloys from series 5000 and 6000 are common for their excellent corrosion resistance and weldability.
The shift towards lighter vehicles is not just a trend; it is often a regulatory requirement. Cars made with aluminum alloys require less energy to move, which contributes to their eco-friendliness. This shift addresses both consumer preferences for better fuel efficiency and regulatory pressures towards sustainable practices.
Construction and Architecture
In construction, aluminum alloys are prized for their adaptability and strength. Commonly used materials include series 5000 and 6000, which provide excellent resistance to weather and UV deterioration.
Members of the construction industry favor aluminum for structural applications, window frames, and roofing sheets, owing to their durability and lightweight nature. This makes installation easier and allows for innovative designs without compromising structural integrity.
Aluminum's recyclability enhances its appeal, enabling construction firms to embrace sustainability in their projects.
Consumer Electronics
Aluminum alloys have transformed the consumer electronics arena, especially in the production of personal devices. Many gadgets like smartphones, laptops, and tablets utilize aluminum for their exteriors. The alloys in use often include series 6000 as they yield an appealing finish while ensuring durability and lightweight structure.
This trend aligns with consumer demands for sleek, robust devices. Moreover, aluminum is conducive to thermal management in electronics, helping dissipate heat effectively. Manufacturers benefit from both aesthetic appeal and functional excellence when choosing aluminum alloys for their products.
"Aluminum alloys are striking a balance between performance, aesthetics, and sustainability across diverse applications."
Overall, the applications of aluminum alloys not only showcase their technical properties but also highlight their importance across various industries. As needs evolve, aluminum alloys will continue to adapt and demonstrate their utility in an increasingly diverse set of applications.
Manufacturing Processes for Aluminum Alloys
Manufacturing processes play a significant role in defining the properties and applications of aluminum alloys. These processes determine the final characteristics of the alloys, which influences their performance in various industries. Understanding these processes allows better decisions regarding material selection and application. There are two main categories of processes: casting methods and forming techniques.
Casting Methods
Casting methods are essential in creating specific shapes and sizes of aluminum parts. These methods leverage the liquid state of aluminum, allowing it to take the form of molds. The three primary casting techniques include sand casting, die casting, and permanent mold casting.
Sand Casting
Sand casting is a traditional method characterized by its simplicity and low cost. The process involves creating a mold from a mixture of sand and a binding agent. Once the mold is formed, molten aluminum is poured into it. This method is particularly advantageous for producing complex shapes.
The key characteristic of sand casting is its adaptability. It can accommodate various sizes and shapes, making it a beneficial choice for prototypes or low-volume production runs. However, sand casting often results in a rough surface finish and lower dimensional accuracy compared to other casting methods.
While sand casting is versatile, it may not be suitable for high-volume production, where precision is crucial.
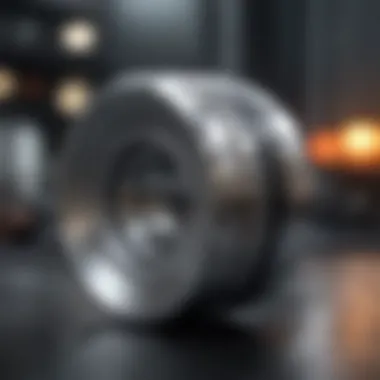
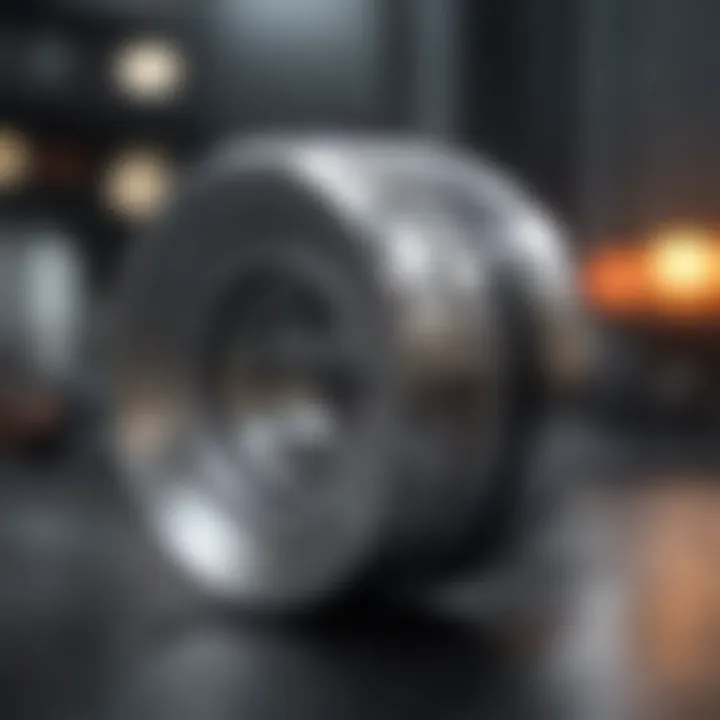
Die Casting
Die casting is a more advanced casting method that provides better precision and surface quality. In this process, molten aluminum is injected under pressure into a steel mold. The rapid cooling allows for quick cycle times and high production rates.
The key benefit of die casting is its ability to produce intricate shapes with excellent dimensional accuracy. The resulting components are often used in high-volume applications, notably in the automotive and consumer electronics sectors. However, initial costs can be high due to the expense of creating the molds. Die casting may also limit the variety of alloys that can be used compared to sand casting.
Permanent Mold Casting
Permanent mold casting combines features from both sand and die casting. In this technique, a permanent mold is used, usually made of steel or iron, which can be reused multiple times. This method allows for finer detail and better surface finish compared to sand casting.
The key advantageous factor of permanent mold casting is the reduction in porosity, which enhances the strength of the cast piece. This feature makes it a popular choice for components that require durability, such as automotive parts. However, the initial investment in the molds can be significant, and like die casting, it may limit alloy selection.
Forming Techniques
Forming techniques involve shaping aluminum alloys without changing their physical state. This category includes extrusion, rolling, and forging. Each technique offers distinct benefits and is suitable for different applications.
Extrusion
Extrusion involves forcing the aluminum alloy through a die to create long shapes with a continuous cross-section. This process is efficient for producing complex profiles.
The primary advantage of extrusion is its ability to create lightweight yet strong components which are consistent in quality. It is commonly used in construction and transportation applications. However, extrusion is limited to specific cross-sectional shapes dictated by the die, which may restrict some design options.
Rolling
Rolling shapes the aluminum by passing it through rollers. This technique is prevalent for producing sheets and plates widely used in various industries.
The primary characteristic of rolling is its ability to produce large, flat sections quickly and consistently. This method is also effective in improving the material's mechanical properties through work hardening. On the downside, the process can lead to thickness variations that may not meet specific structural needs.
Forging
Forging is a process where the aluminum alloy is shaped by applying compressive forces, often at elevated temperatures. This method enhances the strength and toughness of the material.
The key benefit of forging lies in the refined grain structure it imparts to the metal, enhancing mechanical properties significantly. It creates components like gears and aircraft wings, requiring high strength. However, forging can be costlier than other methods and may require substantial energy input for large-scale production.
Each of these manufacturing processes affects the properties of aluminum alloys, influencing factors such as strength, weight, and cost. Understanding these details is crucial for selecting the right aluminum alloy for a specific application.
Future Trends in Aluminum Alloys
In the ever-evolving landscape of materials science, studying future trends in aluminum alloys is vital for professionals and industry leaders. The aluminum sector is witnessing rapid changes driven by technology, sustainability concerns, and market demands. These elements shape how aluminum alloys will be used in the future, impacting their design, production, and application across various sectors.
Recycling and Sustainability
Recycling aluminum is not just a trend; it is a necessity in today's world. Recycling has several benefits, including reducing energy consumption and minimizing landfill waste. The aluminum recycling process uses only about 5% of the energy required to produce new aluminum from ore. This aspect makes aluminum a very environmentally friendly material.
As industries aim for sustainability, the focus is on closed-loop recycling. This method ensures that aluminum materials are continually recycled into new products without degrading their properties. Companies are now investing in technologies that improve aluminum recycling efficiency and effectiveness. The importance of recycling and sustainability is evident in various applications, including automotive and construction, where recycled aluminum is now commonly used.
"The aluminum industry is committed to a sustainable future, where recycling plays a crucial role in reducing environmental impact."
Material Innovations
Innovations in aluminum alloys are shaping their usability and functionality. Research focuses on developing alloys that offer superior strength without increasing weight. Materials such as 7075 and 6061 are receiving enhancements through technology, and innovative methods are emerged to tailor properties according to specific needs.
Further, the introduction of advanced manufacturing processes, such as additive manufacturing (3D printing), is transforming how aluminum alloys are utilized. This method allows for producing parts that were not possible with traditional methods, leading to more complex designs and reduced material waste.
In line with current trends, the integration of nanotechnology into aluminum alloys shows potential for significant improvements. These advancements can result in alloys with enhanced corrosion resistance and improved mechanical properties. Keeping an eye on such material innovations will be essential for anyone involved in industries that utilize aluminum alloys.
In summary, the future trends in aluminum alloys underscore a shift towards sustainability and innovation, directly affecting production methods and applications. By focusing on recycling and embracing new material technologies, industries can enhance the lifecycle and performance of aluminum alloys.
Closure
The conclusion of this article emphasizes the critical role that understanding aluminum alloys plays in a multitude of sectors. As highlighted, aluminum alloys possess distinct properties that cater to specific applications, making them essential in industries such as aerospace, automotive, construction, and consumer electronics. By synthesizing the key characteristics and manufacturing processes discussed throughout the article, it becomes clear that a comprehensive grasp of these materials is not just beneficial but necessary for practitioners in the field.
Summary of Key Points
In summary, this article detailed several key aspects regarding aluminum alloys:
- Types of Alloys: Differentiation between wrought and cast aluminum alloys, along with their respective series, showcases the diversity of options available to engineers and designers.
- Properties: Mechanical properties, including tensile and yield strength, were discussed in relation to their importance in practical applications. Corrosion resistance, thermal, and electrical conductivity were mentioned too, underscoring the versatility of aluminum alloys.
- Applications: Real-world applications across industries were extensively outlined, emphasizing how specific alloys meet exacting demands.
- Manufacturing Techniques: An overview of casting methods and forming techniques provided insights into how these alloys are produced and processed.
- Future Trends: Finally, discussions about recycling, sustainability, and material innovations pointed to the evolving landscape in aluminum alloy use.
The Importance of Understanding Aluminum Alloys
Understanding aluminum alloys is vital for numerous reasons. First, it aids in the selection of appropriate materials for specific applications. Knowledge of mechanical and physical properties ensures that engineers can choose the best alloy for their projects, thus avoiding potential failures and inefficiencies.
Second, insights into the manufacturing processes expand the comprehension of how these materials are shaped and utilized. This not only informs product design but also influences production strategies, impacting costs and sustainability efforts.
Lastly, as industries pivot toward more eco-friendly practices, understanding the recycling potential and sustainability of aluminum alloys becomes indispensable.
To engage effectively with current practices and innovations in aluminum alloy technology, one must be well-versed in these essentials. A robust understanding will not only enhance the quality of work but also contribute to the advancement of the field as a whole.
A deep comprehension of aluminum alloys facilitates informed decision-making, significantly influencing product performance and sustainability.