Understanding Passivation: Mechanisms and Applications
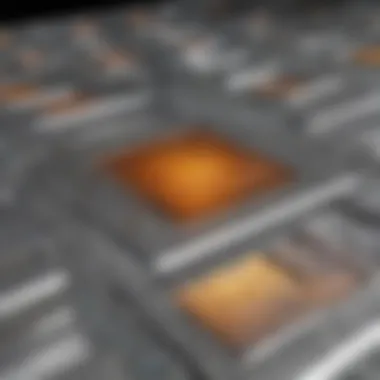
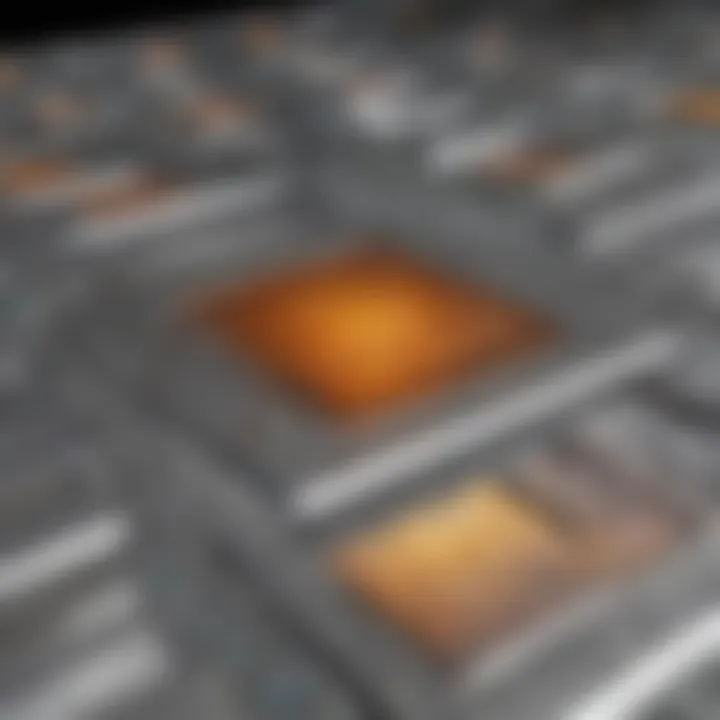
Intro
Passivation serves as a cornerstone in materials science, influencing the longevity and effectiveness of various substances, particularly metals and semiconductors. It essentially forms a protective layer over these materials, preventing reactions that could degrade their performance. This article intends to peel back the layers of passivation, exploring its mechanisms and applications. From real-world uses in electronics to implications for biocompatible materials, passivation is a pivotal subject warranting deeper discussion.
In constructing this exploration, we'll cover essential aspects: the mechanics behind the process, the types of materials typically involved, and how environmental factors can alter outcomes. We'll also analyze the relevance of passivation in future technological innovations, providing a well-rounded understanding aimed at students, researchers, educators, and industry professionals.
Research Highlights
Overview of Key Findings
Through rigorous investigation, this article elucidates several key points about passivation:
- Mechanisms of Passivation: Detailing how chemical processes create a protective layer on metals and semiconductors.
- Types of Materials: Identifying which materials commonly require passivation and the potential benefits they reap.
- Impact of Environmental Conditions: Discussing how humidity, temperature, and other factors can significantly affect passivation efficacy.
- Real-World Applications: From electronics to biocompatible materials, understanding how passivation is applied transforms our comprehension of its utility.
The findings show that passivation is not merely an academic concern but has tangible effects on product quality and longevity in various sectors, including electronics, healthcare, and manufacturing.
Significance of the Research
As industries lean toward innovation and sustainability, the significance of passivation cannot be overstated. Recognizing how passivation enhances durability can lead to the design of products with longer lifespans, ultimately fostering economic savings and reduced waste. Moreover, understanding these mechanisms opens the door for advanced research in materials science, paving the way for new technologies.
"Passivation is likened to putting a strong umbrella over materials, shielding them from the harsh elements of their environment."
The discussion surrounding passivation also extends into academic research realms, providing a fertile ground for future inquiries that can influence technological progress. The succinct understanding of this process fortifies our grasp of how materials can be optimized for both traditional and cutting-edge applications.
Prelims to Passivation
Passivation plays a formidable role in materials science, particularly in the realm of corrosion resistance and enhancing the viability of various materials. Understanding this phenomenon is not simply an academic exercise; it carries substantial implications in industries ranging from electronics to engineering. Passivation processes fundamentally alter a material's surface properties, rendering them more suitable for a range of applications.
When you think about durability in metal and semiconductor applications, passivation often comes to mind. For instance, when metal components are exposed to moisture or other corrosive elements, they readily give in to deterioration. Through passivation, however, these components develop a thin protective layer, akin to putting on a raincoat during a storm. This makes the entire system more reliable and longer-lasting.
Definition and Importance
To put it plainly, passivation involves the process of forming a protective layer on a surface that inhibits further reaction with the environment. This could mean a layer of oxide, hydroxide, or even a polymer. The essence of passivation lies in its ability to mitigate the degradation of materials, which in turn leads to enhanced performance and longevity.
Why is passivation crucial? Here are several reasons:
- Corrosion Resistance: The protective layer prevents penetrating agents from causing rust or other forms of damage.
- Enhanced Product Lifespan: By maintaining structural integrity, passivation contributes to a longer life for various products, ultimately saving costs associated with replacements.
- Performance Consistency: In high-stakes applications, especially in electronics, passivation ensures that materials maintain their functional capabilities over time.
Historical Perspective
Looking back in history reveals a curious evolution of thought regarding passivation. Ancient civilizations often unknowingly relied on the natural passivation of metals, as they discovered that certain treatments could protect their tools from rapid deterioration. It was not until the late 19th to early 20th century that researchers began to formally explore the chemical mechanisms behind the phenomenon.
In the 1920s, scientists like L. E. Ebert made significant strides in understanding how oxides formed on metal surfaces could protect against corrosion. They started to unravel the complexities of these reactions, paving the way for modern applications in which controlled passivation is used across various industries. Today, materials science continues to build upon this foundation, striving for innovative solutions to optimize the passivation processes.
Fundamental Mechanisms of Passivation
The mechanisms of passivation are pivotal to understanding how various materials maintain their integrity over time. They provide a framework for how protective layers form, thus influencing the longevity and performance of metals, semiconductors, and other substances. Comprehending these mechanisms goes beyond academic interest; it has practical implications across industries, from electronics to biomedical applications. The benefits of effective passivation include resistance to corrosion and enhanced functionality in challenging environments. These mechanisms essentially serve as the frontline defenders against detrimental processes that can compromise material properties.
Chemical Passivation
Chemical passivation involves the formation of a protective film on the surface of a material through chemical reactions. This process typically occurs when metals are exposed to acidic or basic solutions, leading to the gradual development of oxide layers that serve as barriers against further corrosion. For instance, stainless steel is often treated with nitric acid, promoting the formation of chromium oxide. This oxide layer not only protects the underlying metal but also tends to self-heal when the surface is scratched, a property that is impressive for its resilience.
Chemical passivation is particularly effective for metals because it alters the surface chemistry without altering the bulk properties of the material. It promotes stability in extreme environments, including fluctuating temperatures and varying chemical reagents. Understanding the necessary conditions for chemical passivation—such as concentration, time, and temperature—is essential for achieving predictable results. Besides, knowledge about the suitable passivating agents can cut costs in long-term material maintenance, improving the lifecycle of the product.
Electrochemical Passivation
Electrochemical passivation takes a step beyond traditional chemical methods by utilizing electrical potential to enhance the process of passivation. Here, an electrochemical cell is created, where an applied electric current influences the formation of a protective layer. This method is especially useful in applications where uniform coverage is essential, such as with intricate geometries in aerospace components.
The key advantage of electrochemical passivation is that it can yield a more controlled and uniform protective layer than chemical methods alone. This is important in industries like microelectronics, where the precision of coatings can dictate the success of device performance. Furthermore, electrochemical passivation employs a range of materials, allowing for tailored solutions based on specific operational environments. By adjusting voltage, current density, and electrolyte composition, it is possible to fine-tune the properties of the passivating layer to meet specific needs.
Physical Passivation
Physical passivation involves barrier methods that provide protection through physical means, rather than chemical changes. This includes processes like coating with non-reactive materials, applying layers of polymers, or even using ion implantation to modify the surface structure of materials physically. For example, applying a thin polymer film over a metal surface can prevent moisture and corrosive substances from reaching the metal.
Physical passivation methods are increasingly gaining traction in fields that require compatibility with varying conditions. They are often preferred due to their simplicity and effectiveness. However, it is worth mentioning that the durability of physical passivation layers can be dependent on mechanical stresses and environmental conditions. Factors such as temperature extremes, UV exposure, and mechanical wear can lead to deterioration of these layers over time, necessitating the need for regular maintenance.
"Understanding these fundamental mechanisms of passivation leads to enhanced material lifespan and performance across diverse applications."
In summary, the fundamental mechanisms of passivation—chemical, electrochemical, and physical—are crucial for improving the durability and performance of materials used in numerous fields.
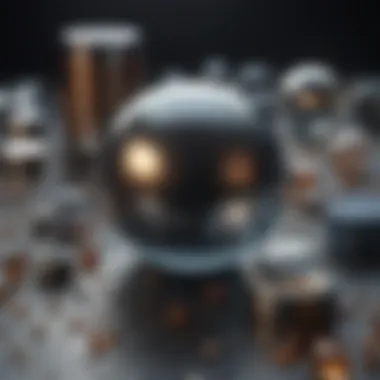
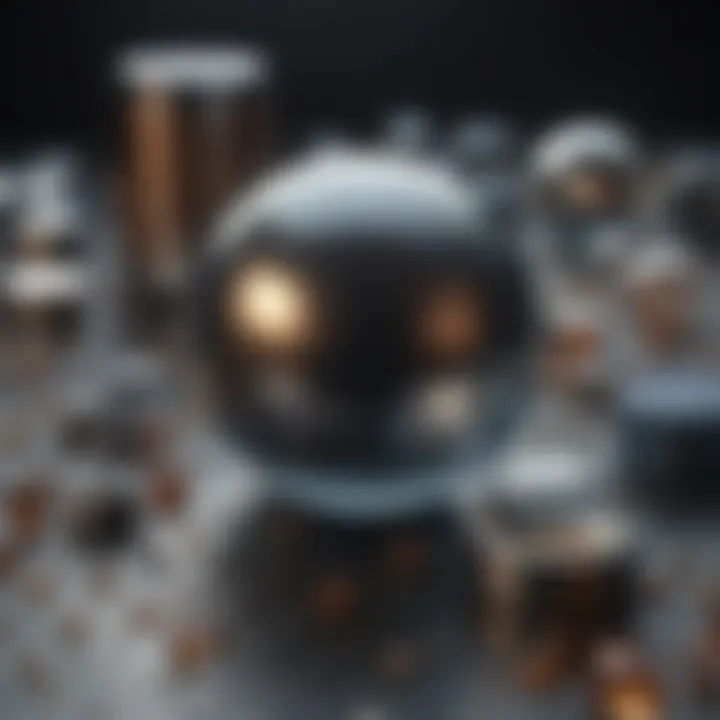
Types of Passivation Agents
Passivation agents play a vital role in enhancing the performance and longevity of materials subjected to various environmental factors. Understanding the types of passivation agents helps in selecting the appropriate method for different applications, suiting the specific requirements of the material in question. By choosing suitable passivation agents, industries can dramatically reduce the risks of corrosion, degradation, and failure. This section delves into the primary classes of passivation agents: oxides and oxyanions, polymeric coatings, and surface treatments.
Oxides and Oxyanions
Oxides and oxyanions are often the first line of defense against environmental attacks on metal surfaces. Basically, these materials form a protective layer that can effectively stave off corrosion. For example, when iron reacts with oxygen, it can form a layer of iron oxide, commonly known as rust, but controlled passivation can result in a protective oxide layer that prevents further degradation. This formation is not only crucial for metals but also plays a significant role in semiconductors where specific oxide layers can enhance electronic properties.
The effectiveness of oxides can be influenced by several factors:
- Thickness of the layer: Thicker layers generally offer better protection.
- Stability: Stable oxides remain intact under corrosive conditions, providing ongoing protection.
- Electrochemical properties: Certain oxides have better conductivity, aiding functionality in electronic applications.
Industry professionals constantly research methods to optimize oxide layer formation to achieve desired properties. Ultimately, oxides and oxyanions represent a fundamental group of passivation agents, making them crucial in the materials science toolkit.
"A well-established oxide layer can be the difference between a functional piece of equipment and a failure in critical systems."
Polymeric Coatings
Polymeric coatings introduce an entirely different strategy for passivation, utilizing synthetic materials to create a barrier between the substrate and the environment. These coatings are especially valuable in applications that demand resistance to adverse elements, including moisture, chemicals, and abrasion. Polymer-based passivation is notable for its versatility and adaptability.
A few benefits of polymeric coatings are as follows:
- Customizable Properties: Depending on the formulation, polymer coatings can exhibit varying degrees of flexibility, hardness, and resistance to various chemicals.
- Ease of Application: Many polymeric coatings are easier to apply than traditional methods, such as electroplating or anodizing.
- Aesthetic Appeal: Available in a plethora of colors and finishes, they can also serve decorative purposes while providing protection.
Polymeric coatings are a cornerstone in various industries, constantly evolving with innovations in material science and technology to enhance their efficiency and sustainability.
Surface Treatments
Surface treatments encompass a wide array of methods aimed at altering the surface characteristics of materials to improve resistance to corrosion, wear, and other forms of degradation. This can include techniques like etching, plating, and polishing, each with its own unique set of benefits and applications.
Some well-known surface treatment methods include:
- Anodizing: Primarily used for aluminum, anodizing enhances corrosion resistance while allowing for dyeing capabilities, making it popular in architectural applications.
- Galvanization: This process involves applying a zinc coating to steel, creating a barrier that protects against rust.
- Nitride Coating: Used widely in the automotive industry, this method significantly improves wear resistance and extends the life of components.
Surfaces treated in these ways often exhibit improved hardness and durability, leading to enhanced lifecycle performance of the materials in their respective applications. With advances in technology, new surface treatment methods are frequently refined, opening possibilities for even better application outcomes.
Materials Commonly Subjected to Passivation
Passivation plays a significant role in the protection and longevity of a variety of materials, particularly metals, semiconductors, and biocompatible substances. The sheer diversity of applications and the different environments these materials inhabit necessitates a thorough understanding of passivation processes. Grasping how specific materials respond to passivation can unlock solutions to many industry challenges, ranging from corrosion prevention to enhanced electronic performance.
Metals and Alloys
Metals, including iron, aluminum, and stainless steel, are perhaps the most common candidates for passivation. The main essence of passivating metals is to safeguard them against corrosion and oxidation. When exposed to harsh environments, these materials can deteriorate rapidly, leading to structural failures or diminished functionality. The passivation process generally forms a protective oxide layer on the metal's surface. For instance, stainless steel is notably resistant to rust due to the chromium oxide layer that forms when chromium reacts with oxygen in the atmosphere. This passive layer can repair itself if damaged, thus ensuring long-term protection.
In practical terms, industries like construction, automotive, and aerospace rely heavily on passivated metals to enhance product lifespans and ensure safety. With corrosive materials often being the enemy of structural integrity, passivation becomes a necessary step in manufacturing processes. Moreover, using passivated alloys can lead to less maintenance over time, ultimately saving costs.
Semiconductors
Semiconductors such as silicon, gallium arsenide, and indium phosphide, while fundamentally different from metals, also require effective passivation techniques. These materials form the backbone of modern electronics, and their performance can be severely influenced by surface states and defects. Just as metals are subject to corrosion, semiconductors are vulnerable to contamination and dielectric breakdown. Passivation here serves to reduce trap states on surfaces, enhancing electrical performance and device efficiency.
A common method of passivating semiconductors is through atomic layer deposition (ALD) or chemical vapor deposition (CVD). These processes deposit thin layers of passivation material, like silicon dioxide or silicon nitride, on the semiconductor surface. For example, in photovoltaic cells, a well-executed passivation can lead to significant efficiency gains by preventing electron-hole pair recombination. In essence, well-passivated semiconductors contribute to better functioning devices in consumer electronics, renewable energy technologies, and telecommunications.
Biocompatible Materials
In the realm of medical devices and biotechnology, biocompatible materials such as titanium, polymers, and certain ceramics also require passivation. The surface interactions between these materials and biological systems are critical. Passivation helps to create non-toxic, bioinert surfaces, which minimizes adverse reactions when implanted in the human body.
For instance, titanium implants undergo passivation to form a thin oxide layer, making them compatible with living tissue and greatly reducing the risk of inflammation or infection. Furthermore, the passivation processes used in these materials must comply with stringent health regulations, emphasizing the importance of quality and consistency.
"Understanding the specific needs of these materials in terms of passivation is key to developing safe and effective medical devices."
In summary, recognizing the types of materials frequently subjected to passivation and their unique requirements is crucial. This ensures improved performance, increased durability, and enhanced safety across multiple sectors, including construction, electronics, and healthcare.
Factors Influencing Passivation Performance
In the realm of passivation, understanding the various factors that affect its performance is paramount. These elements can mean the difference between a successful protective layer and a failure that leaves materials vulnerable to corrosion and degradation. By exploring environmental conditions, surface preparation techniques, and passivation timeframes, one can gain a clearer picture of how to optimize passivation processes for various applications.
Environmental Conditions
The environment plays a crucial role in the effectiveness of passivation. Factors such as temperature, humidity, and the presence of pollutants can greatly influence the formation and stability of passive films on surfaces. For instance, higher temperatures may accelerate the oxidation process, potentially leading to more robust protective layers. However, excessive heat could also lead to film breakdown, negating any gains.
Moreover, humidity levels can affect the moisture content in the air, which can lead to an electrochemical environment that either supports or inhibits the passivation process. In areas where corrosive agents like salt or acidic contaminants are prevalent, the effectiveness of passivation might be compromised. It’s essential for engineers and scientists to consider these variables when designing passivation treatments, as they dictate how materials will perform in real-world applications.
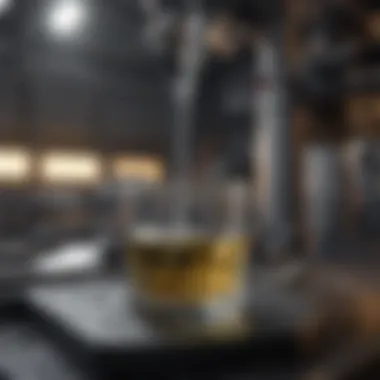
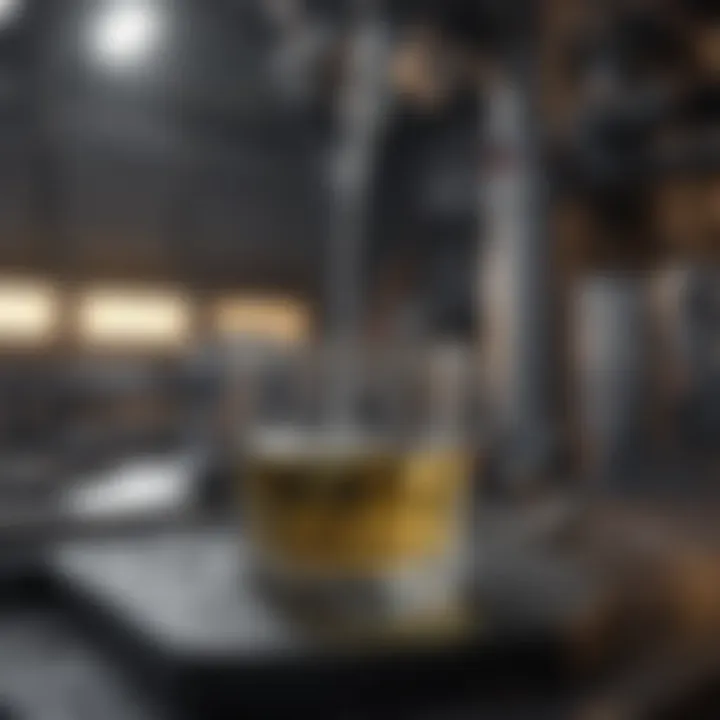
"Understanding the environmental context is like reading the fine print before signing a deal—the details can make all the difference in outcomes."
Surface Preparation Techniques
Another critical factor influencing passivation performance is the method used to prepare the surface prior to treatment. Proper cleaning and preparation ensure that the surface is free from contaminants, such as oils, dirt, or oxides, which can inhibit the effectiveness of the passivation layer. Techniques like sandblasting, chemical cleaning, or even ultrasonic cleaning can be employed to achieve optimal surface conditions before passivation.
Key surface preparation techniques include:
- Mechanical cleaning: Using abrasion methods to remove surface contaminants.
- Chemical cleaning: Utilizing acids or solvents to dissolve unwanted layers.
- Electropolishing: A process that removes material from a metallic surface using electrochemical reactions, resulting in a smoother finish.
The specific technique selected often depends on the material type and the intended application, guiding how well the passivation will perform long-term.
Passivation Timeframes
The duration for which materials are exposed to passivation agents also significantly influences the outcome. This timeframe can dictate the thickness and quality of the passive layer formed. Short exposure might not allow sufficient time for a strong protective film to develop, while overly prolonged exposure can cause unwanted reactions or compromises in material integrity.
For example, certain stainless steel types require a specific soaking time in nitric acid to achieve optimal passivation. Too little time might result in inadequate corrosion resistance, while too much could lead the surface to become overly saturated, affecting its desired properties.
Understanding and optimizing these timeframes is essential for achieving the desired balance of protective properties and material performance. Without meticulous attention to duration, even the best passivation strategies can fall short, leading to failures that could be prevented with informed decision-making.
Applications of Passivation
Passivation plays a vital role in an array of industries, enhancing both the longevity and functionality of materials. By creating a protective layer, passivation helps prevent corrosion and degradation, crucial for extending the life cycle of components. Understanding the applications of passivation allows scientists, engineers, and researchers to harness this process for various practical purposes. Not only does it improve material performance, but it also fosters innovation in design and technology. Let's take a closer look at specific sectors where passivation is making a significant impact.
Electronics and Semiconductor Devices
In the electronics realm, passivation is indispensable. The semiconductor industry, especially, relies heavily on passivation processes to enhance device performance. The primary function here is to minimize surface contamination which can hinder electrical properties. For example, silicon wafers are often treated with silicon dioxide or silicon nitride layers. These materials serve as barriers, protecting against moisture and pollutants that can interfere with the circuit's integrity.
Moreover, passivation aids in improving reliability by reducing leakage currents. The best part? It allows for smaller, more efficient devices, leading to advancements in everything from mobile phones to laptops. In essence, without passivation, many modern electronics might just not perform as reliably or last as long as we expect.
Structural Engineering
In structural engineering, passivation is critical, particularly for structural steels and other metals exposed to harsh environments. The protective layers formed through passivation can dramatically reduce the rusting that often plagues these materials when subjected to moisture and varying temperature conditions. Think about bridges or buildings; these structures require materials that can resist environmental attacks, and that's where passivation steps in.
For instance, when carbon steels are passivated, the oxides formed act as shields against further corrosion, preserving the integrity of the structure for years on end. Not only does this mean lower maintenance costs, but it also enhances the overall safety and longevity of engineering projects. A well-passivated structure translates to trust in its durability.
Biotechnology and Medical Devices
When it comes to the biotech industry and medical devices, passivation offers unparalleled benefits. Medical instruments, implants, and devices must meet stringent cleanliness and safety standards. Here, passivation ensures that metals like titanium and stainless steel are not only biocompatible but also resistant to wear and corrosion from bodily fluids.
For instance, titanium implants achieve passivation through chemical treatments that enhance their ability to avoid reactions with human tissues. This is crucial for instances such as dental implants or orthopedic devices, where long-term performance and biocompatibility are of utmost importance. The implications of effective passivation in this field are broad, impacting patient outcomes and device success rates.
"Passivation is not just a protective measure; it's a foundation for safety in medical applications."
Challenges in Passivation
Understanding passivation isn’t all sunshine and rainbows. It comes with its own set of hurdles that can complicate the process and affect overall performance. Identifying and addressing these challenges is crucial, especially when passivation plays a vital role in many applications. Whether it’s metals, semiconductors, or biocompatible materials, knowing the limitations helps researchers fine-tune methods and improve results.
Inconsistent Results
One of the most arduous challenges about passivation is achieving consistent results across various materials and environments. It’s like trying to bake the perfect loaf of bread. One minute you think you've got the recipe nailed, only to find out that the yeast was too old, and the loaf flops.
In the context of passivation, discrepancies can stem from a multitude of factors:
- Surface Preparations: Not every surface is created equal. Variations in cleanliness or surface roughness can greatly influence how passivating layers form.
- Environmental Conditions: Factors like humidity, temperature, and even air quality can lead to different passivation behaviors. If the surrounding environment behaves like a raucous teenager on sugar, it can produce unpredictable results.
- Material Composition: Different alloys or coatings respond uniquely to their surroundings. A bit of nickel mixed in might change the whole game. Sometimes, researchers may find themselves battling with the complexities of the materials they work with.
"In passivation, results can swing wildly, stumping even seasoned experts. It's not just about applying a coat; it's about creating an ideal environment."
The result of all this inconsistency can be a challenging reliance on trial and error, with some methods yielding success while others fall flat, leaving researchers scratching their heads.
Limitations of Current Methods
The methods and techniques used today for passivation are not foolproof. Every approach comes with its benefits and downfalls, making it essential to weigh the pros and cons.
For instance, traditional methods like chemical treatment can be effective but often lack versatility.
- Chemical Treating: While it works wonders for certain types of metals, chemical treatments might not adhere well to others, leading to patches where the passivation is weaker.
Furthermore, the developments in electrochemical passivation techniques are impressive, yet they do not come without challenges:
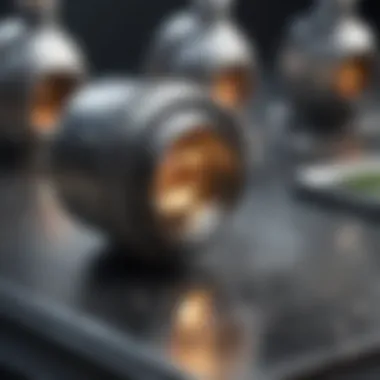
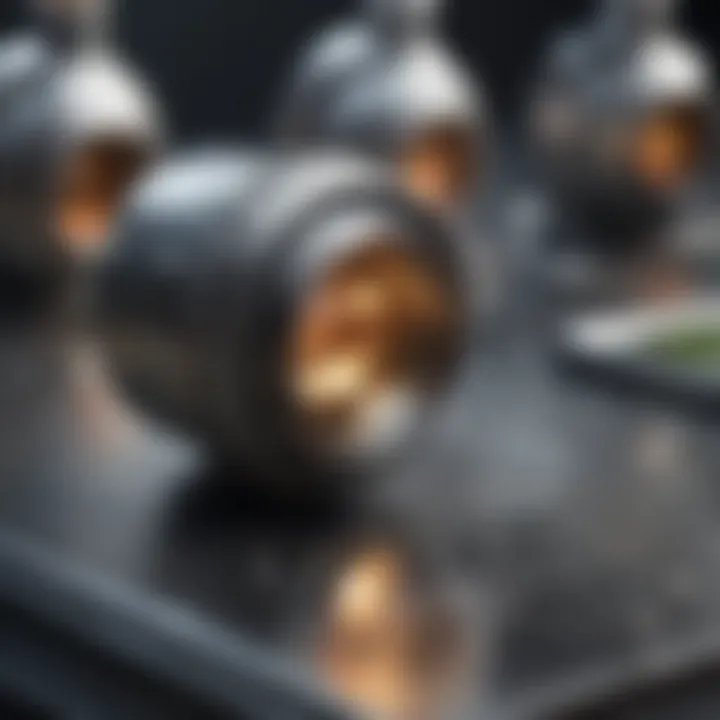
- Complex Equipment: A top-notch electrochemical setup can be quite costly and complex to operate, making it less accessible for smaller institutions.
- Difficulties in Scale-Up: What works well in a lab doesn’t always translate to larger manufacturing processes.
Moreover, the rise of smart materials with self-passivating properties holds promise, but they’re still largely in the experimental stage. Achieving consistent performances in real-world conditions is a knot that needs untying.
In sum, while current passivation methods have led to significant advances, they have limitations that researchers must continually navigate. This exploration of challenges lays the groundwork for future developments and innovations in the art and science of passivation.
Recent Advances in Passivation Research
Recent developments in the realm of passivation research have opened up new vistas for materials science, spotlighting innovative methodologies that promise enhanced performance and durability. The significance of these advances cannot be overstated, as they play a pivotal role in addressing the challenges found in various industries, from electronics to biomedicine. Understanding these modern innovations not only enriches our knowledge but also empowers researchers and professionals alike to make informed decisions in their specific areas of expertise.
Nano-coatings and Innovations
Nano-coatings represent a transformative leap in passivation technology, marrying the principles of nanotechnology with traditional passivation methods. These ultra-thin films, often measuring just a few nanometers in thickness, offer unique properties that can dramatically improve the surface characteristics of materials. For example, they enhance corrosion resistance while minimizing weight.
Some advantages of nano-coatings include:
- Improved Protection: The small size and uniformity of nano-coatings create a robust barrier against environmental aggressors such as moisture, salt, and pollutants.
- Enhanced Adhesion: The nanoscale structure allows better bonding with substrates, which can improve the longevity of coatings.
- Aesthetic Appeal: These coatings can be engineered for specific aesthetics, offering useful applications in consumer electronics.
Notable innovations in the field involve the use of materials like graphene and carbon nanotubes. Their inherent strength and conductivity pave the way for applications difficult to achieve with conventional coatings, especially in the electronics sector. As researchers continue to explore these materials, we may find unforeseen breakthroughs in passivation strategies, ultimately leading to smarter, more resilient products.
Smart Materials with Self-Passivating Properties
Self-passivating materials represent another frontier in passivation research. These advanced substances have the remarkable capability to spontaneously generate protective layers in the presence of environmental factors. This characteristic not only simplifies the passivation process but also promotes sustainability through reducing the need for external protective measures.
Self-passivating materials offer various benefits:
- Auto-regeneration: The ability to form protective layers when subjected to corrosive environments can significantly reduce maintenance costs and efforts.
- Flexibility in Application: These materials can potentially be used in a range of applications, from structural components to medical implants.
- Environmental Resilience: Many smart materials can adapt to changing conditions, offering steadfast protection where it’s most needed.
A prime example is the exploration of titanium alloys, which can exhibit self-passivation by forming stable oxide layers upon exposure to air. Such developments promise to revolutionize not only how materials are protected but also their application across diverse fields like aerospace and biocompatible devices.
"Recent advances in passivation research highlight the confluence of innovation and practicality, enabling materials to either protect themselves or be enhanced to provide superior performance."
In summary, the exploration of nano-coatings and self-passivating materials points to an exciting era in passivation techniques. By leveraging these advancements, scientists and engineers have the potential to fabricate more robust, efficient, and sustainable products that stand the test of time and environmental challenges.
Future Directions of Passivation Studies
The field of passivation is on the brink of significant evolution. As technology advances and environmental challenges loom large, researchers are contemplating new methodologies and applications that promise to revolutionize the standards by which passivation is understood and applied. This section delves into futuristics aspects of passivation studies, with a specific emphasis on sustainability considerations and the integration of artificial intelligence in passivation techniques.
Sustainability Considerations
Reflecting on the global push towards greener technology, sustainability in passivation has taken center stage. Traditional methods of passivation often involve toxic chemicals, which pose risks not only to human health but also to the environment. New sustainability-oriented practices are being discussed and developed. For instance:
- Bio-based passivation agents: Researchers are looking into using natural extracts like plant derivatives that can serve the same function as synthetic agents. This approach can reduce the carbon footprint associated with passivation processes.
- Recycling passivation solutions: Systems that enable the reuse of passivation solutions can help minimize waste, aligning with circular economy principles.
- Energy-efficient processes: Investigating low-temperature treatments or photocatalytic processes can yield substantial energy savings while maintaining performance standards in various applications.
Implementing sustainable practices will not only cater to regulatory demands but will also appeal to the growing conscious consumer market. The prospect of greener passivation holds significant promise for industrial capacities, offering long-term benefits both economically and environmentally.
Integration of AI in Passivation Techniques
In an increasingly data-driven world, the adoption of artificial intelligence in passivation research shows great potential. AI can streamline the development and application of passivation techniques in several ways:
- Predictive modeling: By analyzing existing datasets on materials and their passivation responses, AI can predict optimal conditions and agents that would lead to the best results. This is particularly useful in selecting passivation treatments that might not be immediately apparent from empirical studies.
- Process optimization: AI algorithms can monitor and adjust conditions in real-time during passivation processes, ensuring efficient use of resources and reducing waste, thus enhancing the overall efficacy of the treatment.
- Material discovery: Machine learning can accelerate the discovery of new passivation agents by identifying compounds with similar properties to known effective agents. This opens avenues to innovate and potentially develop novel, more effective agents that hold promise for specific applications.
Adopting AI tools in passivation can yield faster, more accurate results while concurrently minimizing human error. It's a win-win situation that could significantly advance the field, paving the way for discoveries that transform current understandings of passivation.
"Embracing new technologies and sustainability in passivation isn't just about following trends—it's about leading them."
In summary, the future of passivation studies seems bright. By prioritizing sustainability and embedding AI into research methodologies, stakeholders can make strides towards a more effective, environmentally friendly, and technologically advanced approach to passivation.
Closure
The conclusion section serves as a pivotal part of the article, synthesizing comprehensive insights on passivation. It holds significant importance, as it not only reinforces the key findings discussed throughout the text but also highlights implications for future explorations. In essence, this summarization becomes an anchor for readers, pulling together the various elements of passivation and providing clarity on its role in various disciplines.
Summary of Insights
To recap, passivation is not merely a technical term; it encompasses a variety of mechanisms and applications that reshape our understanding of material resilience. From its historical roots to modern applications in electronics and biocompatible materials, it shows how critical passivation is in enhancing device performance and longevity. By enabling protective layers, passivation combats corrosion, increases the lifespan of materials, and opens doors to innovations yet to come.
Key points include:
- Diverse Mechanisms: Understanding chemical, electrochemical, and physical paths that lead to effective passivation.
- Variety of Agents: Recognition of oxides, polymeric coatings, and surface treatments, all serving to enhance durability.
- Material Focus: Specific application on metals, semiconductors, and biocompatible materials shows the versatility of passivation.
Overall, the revelations about passivation deepen our appreciation of materials science and encourage further exploration of its potential benefits.
Implications for Future Research
Looking towards the future, the implications of passivation research extend far beyond the current knowledge. Prioritizing sustainability, the quest for eco-friendly passivation techniques is becoming increasingly essential. New approaches that minimize waste and environmental impact while maintaining or enhancing effectiveness are required.
Furthermore, the integration of artificial intelligence in passivation could revolutionize how we assess and develop these processes. AI could assist in predicting outcomes, optimizing conditions, and even personalizing treatments based on specific material needs. This level of customization will likely become crucial as industries evolve to demand materials that are not only more durable but also adaptable to changing environmental conditions.