Electrode Machines: Applications and Future Insights
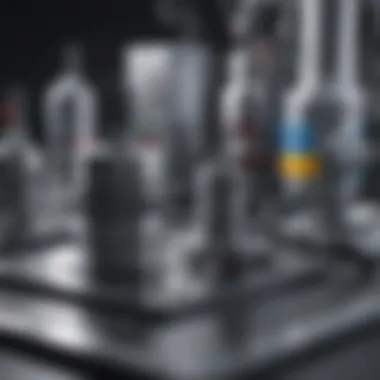
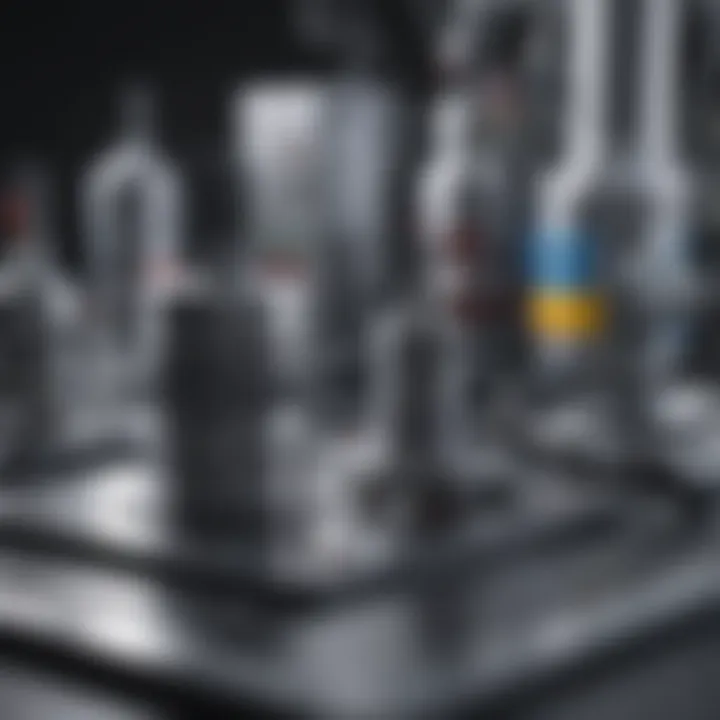
Intro
Electrode machines represent a pivotal component in modern engineering, with their influence extending across various sectors including manufacturing, healthcare, and environmental technology. Understanding their mechanisms, applications, and future directions is vital for students, researchers, educators, and professionals keen on innovation and technology.
The operational principles of electrode machines are rooted in fundamental scientific concepts. These machines utilize electrical currents to induce various mechanical effects, making them valuable in a wide range of applications. In todayโs world, where efficiency and precision are paramount, electrode machines have emerged as efficient tools in processes such as electrochemical machining and material synthesis.
This article will unfold by examining the critical applications that electrode machines have in industry and research. Furthermore, it will delve into their mechanisms, explaining how they function and why they are designed a certain way. Finally, the discussion will lead to potential advancements that may reshape the landscape of electrode machines, offering insights into where this technology is headed in the future.
Prologue to Electrode Machines
Electrode machines play a pivotal role in various industrial and scientific applications. Their importance is underscored by their ability to manipulate materials at a granular level, which enhances efficiency and precision in production processes. Understanding the principles and functionalities of these machines is essential for students, researchers, educators, and professionals who aim to leverage them effectively in their respective fields.
Definition and Purpose
Electrode machines refer to a category of equipment used primarily to process materials using electrical energy. The primary purpose of these machines includes cutting, shaping, welding, and surface treatment of conductive materials. They operate through a process that varies based on the specific technology employed, such as electrolysis or electric discharge machining (EDM).
The fundamental principle revolves around the interaction between the electrode and the workpiece, where a controlled electric current is utilized to create the desired modifications. This technology enhances product quality while reducing the overall time and cost of production. The versatility of electrode machines extends to industries ranging from manufacturing to telecommunications, indicating their critical role in modern production workflows.
Historical Context
The history of electrode machines is intertwined with the advancement of electrical engineering. They emerged from the developments in electrical discharge phenomena during the late 19th and early 20th centuries. One notable milestone was the invention of EDM by Joseph Priestley in 1770, which has evolved significantly over the centuries. The potential applications of electrode machines were initially limited to specialized tasks but have progressively expanded due to innovations in materials and technology.
By the mid-20th century, the industrial sector began adopting these machines more extensively, especially as automation technology gained traction. The introduction of computer numerical control (CNC) in the 1970s revolutionized machining processes, further solidifying the role of electrode machines in industrial settings. Today, they continue to evolve, integrating advanced technologies such as artificial intelligence and robotics, which promise to shape their future significantly.
This evolution demonstrates not only the adaptive capabilities of electrode machines but also their increasing significance in addressing complex manufacturing challenges.
Principles of Operation
Understanding the principles of operation is crucial to grasp the functionality and efficiency of electrode machines. This section addresses the core mechanics involved in their operations. Recognizing these principles helps in assessing why specific machines are chosen for particular tasks. The basic mechanisms set the foundation for various applications, which influences both design and innovation. Thus, comprehending these principles is key for anyone involved in engineering, manufacturing, or research.
Basic Mechanisms
The basic mechanisms of electrode machines primarily revolve around electrical discharge, which can be classified into different forms. One fundamental mechanism is the generation of an electric arc, which occurs when electrical current passes through a gas or between two electrodes, resulting in a high-temperature plasma. This process enables significant energy transfer and heat production, essential for cutting or welding materials effectively.
Another critical mechanism involves electrolysis, where an electrical current drives a chemical reaction. This method is vital for surface finishing or coating processes. By understanding these mechanisms, one can better appreciate the versatility and efficiency these machines bring to various applications in manufacturing and material science.
Types of Electrode Machines
Different types of electrode machines have evolved to meet the diverse needs of industries. Each type has unique features that contribute to specific operational goals.
Conventional Electrode Machines
Conventional electrode machines, often regarded as the backbone of traditional manufacturing processes, play a pivotal role in tasks like welding and cutting. Their main feature is the straightforward operation, which employs a simple electrical feed to generate the required discharge. This effectiveness makes them a common choice in workshops and fabrication units.
The main advantage of using conventional machines lies in their low initial cost and ease of use. Many technicians find them familiar, reducing the learning curve involved for new operators. However, the disadvantages include limitations in precision and adaptability when compared to modern systems. As industries demand greater precision, conventional machines may not meet the evolving needs as effectively.
Computer Numerical Control (CNC) Machines
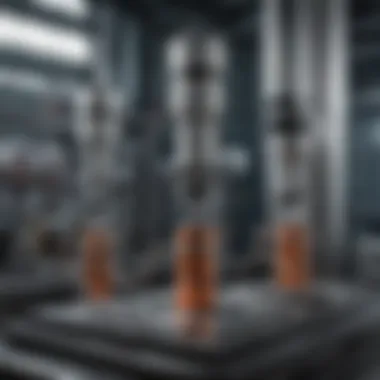
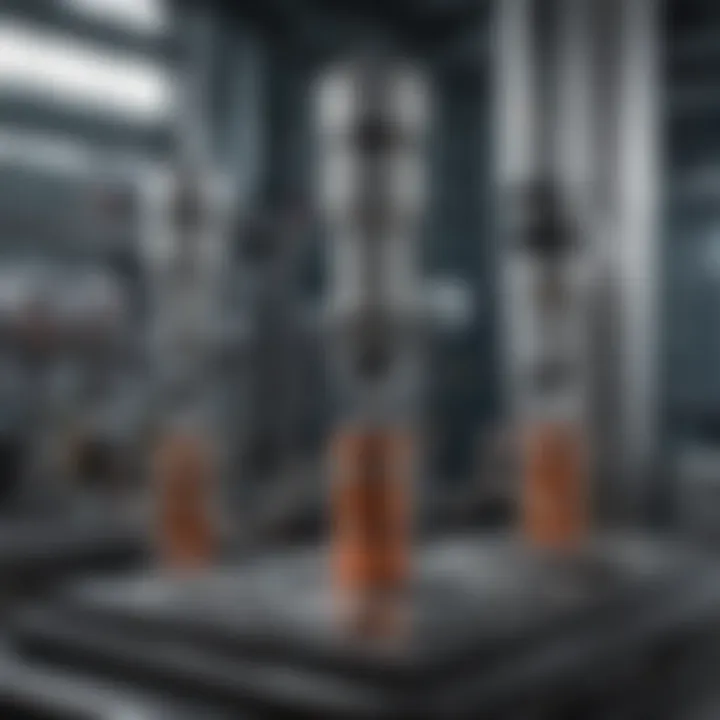
Computer Numerical Control (CNC) machines represent a significant advancement in electrode technology. One of their key aspects is programmability, allowing for intricate control over machining processes. This adaptability contributes greatly to highly precise and repeatable results, which are vital in today's competitive market.
CNC machines commonly integrate advanced software that takes care of the operational sequence, which leads to reduced human error. The programmability of CNC machines provides substantial flexibility, making it possible to accommodate various designs with minimal downtime. However, the complexity of these machines sometimes leads to higher operational costs, particularly in training and maintenance.
Robotic Electrode Systems
Robotic electrode systems signify the peak of automation in machining. Their key characteristic is the integration of robotics with electrode processes, allowing for high-speed operation and efficiency. This combination enhances productivity and ensures consistency across multiple repetitive tasks.
A unique feature of robotic systems is their ability to access hard-to-reach areas, which traditional machines cannot easily handle. However, one must consider the initial investment and setup complexity involved in implementing these systems. Their operational efficiency can largely outweigh these challenges if used in high-volume applications.
Applications in Industry
The application of electrode machines is critical within various industrial settings. These machines enhance efficiency, precision, and versatility in numerous tasks. Their roles span from manufacturing processes to complex electrochemical applications. Understanding how electrode machines are used in industry allows professionals to optimize workflows and foster innovation.
Manufacturing and Assembly
In the realm of manufacturing, electrode machines play an essential role in the production of components and systems. They provide accurate and repeatable results, which is crucial for high-volume production. The profiling and shaping capabilities of these machines allow manufacturers to create intricate designs with tight tolerances.
Key benefits of using electrode machines in manufacturing include:
- High Precision: Electrode machines can achieve minimal tolerances, ensuring that components fit together perfectly.
- Speed of Production: Automation through CNC systems reduces production times significantly.
- Material Reduction: The ability to create components from a single piece minimizes waste, benefiting the environment.
However, companies must consider certain factors like the initial investment cost and the need for skilled operators. The benefits often outweigh the challenges, leading to improved profitability and product quality in the long run.
Electrolysis and Surface Treatment
Electrode machines also have a prominent role in electrolysis and surface treatment processes. Electrolysis is fundamentally important in various applications such as metal plating, refining, and separation of substances. These machines facilitate controlled environments, where specific parameters can be adjusted for optimal results.
Some uses of electrode machines for electrolysis and surface treatment include:
- Plating and Coating: This enhances properties like corrosion resistance and aesthetics of materials.
- Anodizing: It increases the thickness of the natural oxide layer on the surface of metals, improving durability.
- Surface Cleaning: Electrode machines efficiently remove contaminants from surfaces, preparing them for further processing.
The engineering behind these machines allows for customizable setups to meet diverse industrial needs. Adjustments in voltage, current, and chemical concentrations can significantly influence outcomes.
Welding and Joining Techniques
Welding and joining techniques are equally important applications of electrode machines in various sectors. They provide robust methods for connecting different materials, which is often necessary in construction, automotive, and aerospace industries.
Electrode machines utilized in welding can be classified into several categories, including:
- Resistance Welding Machines: These apply pressure and heat through electric current, making them suitable for spot welding.
- Arc Welding Machines: They generate an arc between the electrode and workpieces, melting the material to form a bond.
- Laser Welding Systems: Offering high precision, laser welding machines are ideal for delicate components.
Using electrode machines for welding enhances joint strength and integrity. They also help reduce human error, leading to consistent quality in products. It is crucial, however, to ensure proper training for operators to maximize safety and efficiency in these operations.
Electrode machines have transformed various industries by providing reliable, precise, and efficient solutions to complex tasks. Their role in manufacturing, surface treatment, and welding highlights their indispensable nature in modern production scenarios.
Advancements in Electrode Technology
The realm of electrode technology is evolving at an unprecedented pace. This section discusses how advancements not only enhance performance but also expand the scope of application. As industries demand higher efficiency and sustainability, innovations in electrode machines are critical. Understanding these advancements paves the way for enhanced processes across a variety of sectors. Key elements include material innovations, integration with artificial intelligence, and the rise of automation and robotics.

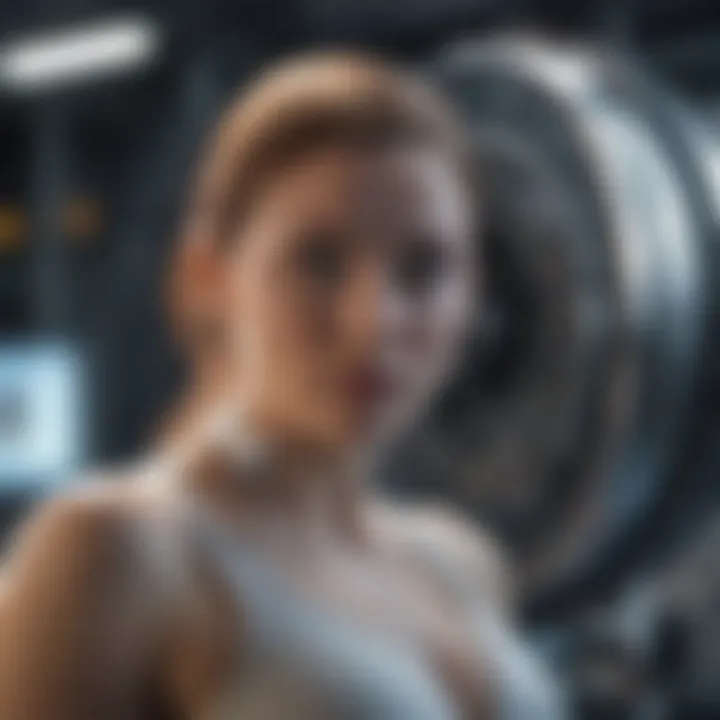
Material Innovations
Material advancements are at the forefront of electrode technology. New compositions exhibit improved conductivity, durability, and resistance to corrosion. For instance, titanium and nickel alloys are proving effective in high-temperature environments. Furthermore, the development of nanomaterials has introduced electrodes with superior performance metrics. These include higher surface areas and greater catalytic activity. Manufacturers are now better equipped to design systems that can handle more demanding applications without compromising efficiency.
- Benefits of Material Innovations:
- Enhanced durability in extreme conditions
- Improved energy efficiency
- Greater range of applications, enabling novel uses
Notably, these materials enable electrode machines to perform in environments that were once considered unsuitable. Thus, industries can capitalize on these innovations for new product development and to meet stricter environmental regulations.
Integration with Artificial Intelligence
Artificial intelligence (AI) is transforming electrode machines. By incorporating machine learning algorithms, these systems can now monitor and optimize operations in real-time. Predictive maintenance, for example, is a key benefit. Electrode machines equipped with AI can anticipate failures, reducing downtime and enhancing productivity. Moreover, AI-driven optimization allows for precise adjustments, leading to improved product quality.
- Considerations for AI Integration:
- Requires substantial initial investment
- Continuous need for data management and analysis
However, the long-term savings and efficiency gains typically outweigh these challenges. Industries are increasingly adopting AI solutions to stay competitive in a rapidly evolving marketplace.
Automation and Robotics
The rise of automation and robotics alongside electrode technology cannot be overlooked. Automated systems streamline production processes and reduce human error. Robots can handle precise tasks that are often too intricate for manual operation, enhancing consistency in production. This leap in technology is reflected in sectors such as manufacturing and materials processing.
- Advantages of Automation:
- Increased accuracy and precision
- Reduced labor costs
- Ability to operate in hazardous environments
A landscape filled with robotic systems executing complex tasks will redefine factory floors. As a result, companies can reach higher levels of output while adhering to safety and quality standards.
Integrating material innovations, artificial intelligence, and automation marks a significant transition in electrode technology. This evolution is not simply about enhancing one aspect but transforming the entire landscape of manufacturing processes.
Challenges and Limitations
Understanding the challenges and limitations of electrode machines is crucial. This analysis not only provides insight into the operational hurdles but also illuminates the economic and environmental considerations involved. Recognizing these factors can assist industry professionals and researchers in navigating the complexities of deploying electrode technology effectively.
Technical Challenges
Technical challenges in electrode machines can manifest in various forms. One significant issue is the precision of the machines. Ensuring high accuracy during operations is vital for achieving desired outcomes. Variability in material properties, machine calibration, and environmental conditions can introduce errors. Furthermore, the wear and tear of electrodes can affect performance and reliability.
Another technical challenge relates to the integration of advanced technologies, such as artificial intelligence. Aligning these systems to work harmoniously with existing machinery presents difficulties. Ensuring software and hardware compatibility often requires extensive testing and fine-tuning, which can lead to increased downtime and costs. There is also the challenge of optimizing energy consumption, as electrode machines can be power-intensive. Energy efficiency plays a crucial role in both operational cost and sustainability.
Economic Considerations
The economic landscape surrounding electrode machines is complex. Initial investments for advanced systems can be substantial. Companies must evaluate the cost-versus-benefit ratio carefully. High-quality machines may offer enhanced productivity but require a significant upfront investment. Companies may hesitate to adopt newer technologies due to financial constraints or uncertainty about return on investment.
Moreover, ongoing maintenance and training for personnel can add to the overall costs. As technological advancements occur rapidly, organizations must continuously invest in training staff to keep pace with developments. This can strain budgets, especially for smaller businesses. Notably, fluctuating market demands can impact the demand for electrochemical processes and subsequently influence pricing strategies.
Environmental Impacts

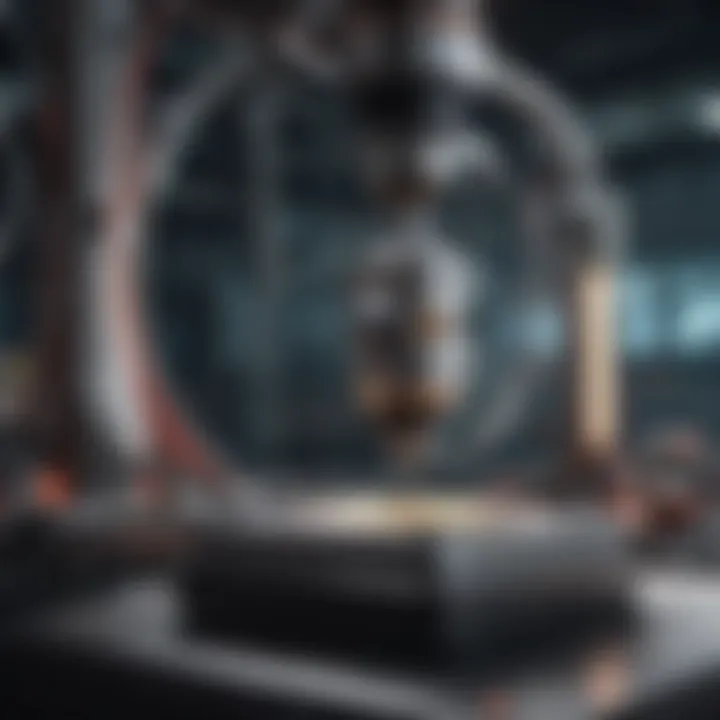
The environmental impacts of electrode machines warrant attention. The production processes can generate waste materials, which require mindful handling. Efforts to recycle or manage these by-products can influence operational practices and add layers of complexity to sustainability initiatives.
Additionally, energy consumption during operation can contribute to carbon footprints. Industries must explore renewable energy options to mitigate these effects. Implementing changes to operational practices aimed at reducing emissions and increasing energy efficiency is becoming imperative. Environmental regulations are also evolving, and companies must stay compliant to avoid penalties.
Understanding the challenges and limitations of electrode machines is fundamental for industries that rely on them. Addressing these issues can lead to improved performance, economic viability, and reduced environmental impacts.
Future Trends
Understanding future trends in electrode machines is critical for anticipating how these technologies will evolve and impact various industries. As advancements continue across multiple sectors, electrode machines will undergo significant transformations. These changes will be driven by emerging applications, new technologies, and shifts in societal needs. Recognizing these future trends can provide insights into the opportunities and challenges that lie ahead.
Emerging Applications
Electrode machines are finding new roles in fields previously untouched by this technology. The rise of electric vehicles has increased the demand for efficient battery production, where electrode machines will play a vital role in manufacturing components. Furthermore, in the medical industry, they are being used for the precision fabrication of medical devices, ensuring high levels of accuracy and safety. Some other notable applications are:
- Microelectronic fabrication: Elecrode machines are crucial in producing semiconductor devices, where precision is paramount.
- Additive manufacturing: Utilization of electrode machines in 3D printing is revolutionizing the production methods across different industries.
- Renewable energy: Electrode machines are increasingly employed in the production of equipment for solar energy and wind power.
These applications underscore the versatility and necessity of electrode machines in addressing modern industrial challenges. It highlights the importance of continuous research and innovation to meet growing demands.
Research Directions
Research is essential for the future development of electrode machines. Focus areas include:
- Material science: Innovations in conductive materials can enhance performance and efficiency, leading to more energy-efficient electrode machines.
- AI and machine learning: Integrating artificial intelligence can optimize the operation of electrode machines, improving their precision and reducing downtime.
- Sustainability: The demand for eco-friendly manufacturing processes calls for research into minimizing waste and energy consumption in electrode technologies.
Research collaborations among universities, industries, and independent researchers can expedite these advancements. Initiatives aimed at developing new technologies will create pathways for engineers and scientists to explore the potential of electrode machines further.
"Emerging technologies are creating a new generation of electrode machines, pushing boundaries in efficiency and environmental sustainability."
Epilogue
The conclusion of this article encapsulates the significance of electrode machines within both industrial and scientific landscapes. Through understanding the multifaceted roles these machines play, one can appreciate their impact not only in applications but also in advancing technological boundaries.
Electrode machines are pivotal in areas such as manufacturing and surface treatment. As they evolve, they become indispensable tools that drive efficiency. Economic benefits are significant as these machines reduce production costs while improving product quality.
Additionally, the exploration of advancements in electrode technology has shown promising directions. The integration of artificial intelligence and automation is enhancing precision and productivity. Therefore, the implications of these trends stretch beyond mere machinery. They herald a new era of innovation that is set to address larger societal challenges, such as sustainable production practices and energy efficiency.
"The future of electrode machines lies not just in their current applications, but in their potential to shape entire industries."
Summary of Key Points
- Definition and Purpose: Electrode machines facilitate essential operations in manufacturing and treatment processes.
- Principles of Operation: Understanding mechanisms is crucial for effective applications.
- Applications in Industry: These machines are employed across various fields, significantly impacting efficiency and product quality.
- Advancements in Technology: Innovations in materials and integration with AI are reshaping the landscape of electrode machines.
- Challenges: Addressing technical, economic, and environmental constraints is critical for the future.
- Future Trends: The emergence of new applications and research directions indicates a promising horizon filled with potential.
Implications for Future Research
Future research on electrode machines is essential for several reasons.
First, as technology evolves, understanding the limitations and challenges faced in current applications can refine future designs. Expanding research in materials science can yield more durable and efficient electrodes.
Moreover, as industries increasingly embrace automation, research into improving computer numerical control systems will enhance precision and applicability.
Research must also consider environmental impact. Innovations that lessen ecological footprints will become a priority.
Ultimately, guiding policies and ethical frameworks around the advancing technologies will shape how electrode machines are utilized in sustainable ways.
Advancements in these areas promise not only to enhance operational capabilities but also to ensure that the benefits of electrode machines are harnessed for positive societal outcomes.
Cited Works
The listed works in this section reflect a diverse spectrum of studies related to electrode machines, underscoring their applications, mechanisms, and future directions. These include, but are not limited to, the following types of references:
- Academic Journals: Peer-reviewed articles provide foundational knowledge and recent advances in the field.
- Books: Comprehensive sources documenting historical context and theoretical frameworks.
- Industry Reports: Up-to-date data from respected institutions offering insights into current trends and future implementations.
- Technical Standards: Specifications and guidelines from organizations that shape industry best practices.
Each citation contributes to the readersโ ability to substantiate claims or survey additional contexts, enhancing the overall quality of their learning experience. By engaging with these works, one can uncover how different machines evolve and adapt in response to technological demands.
"References are not merely obligatory sections in scholarly writing; they are gateways to new knowledge and understanding."